Plastic welding is a technique that many people seem to misunderstand. To the casual observer, it seems to be quite simple; you heat a plastic surface until it softens, push it against another plastic surface, and wait for the bond to cool. Job done?
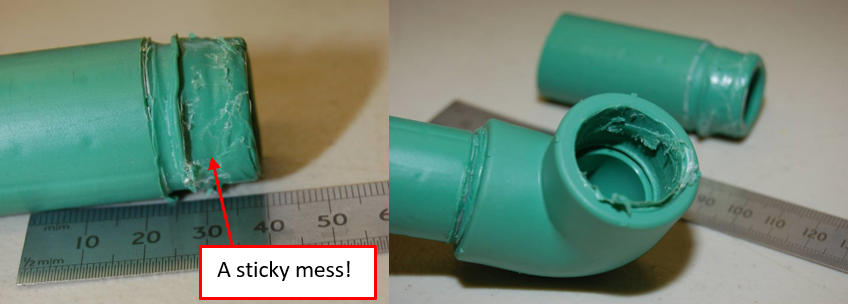
Not quite. There are many different plastic welding techniques, and each has its own intricacies, features and details that must be considered and understood, if the welding is to be done successfully.
Plastic welding is used in many industries and for numerous applications, but one of the most important is in plastic (polymer) pipework. From Hawkins’ perspective, this is also probably the most common application of plastic welding for which we investigate and report on the cause of failures.
For a forensic engineer, the key to finding the cause of failure in a plastic welded joint is a proper understanding of how that weld could have been made successfully. This knowledge gives us a good idea of what to look for, to then explain why a weld did not perform as expected. The first part of this article will be a brief introduction to common plastic (pipe) welding techniques and the keys to getting them right. The second part of the article will describe some typical failure types and present some examples Hawkins has seen in our investigations.
SUCCESSFUL WELDING OF PLASTIC PIPES
Fundamentally, the simplistic view of how plastic welds are made, described in the first paragraph of this article, is correct. It is a process that involves softening and combining the surfaces of the materials or parts (pipes), to create a joint. There are numerous available techniques, which can achieve the softening of the plastic surfaces in two ways:
- The application or creation of heat
- ‘Dissolving’ the polymer at the bonding surface with a chemical solvent
Plastic welding is only used with thermoplastic polymers (not thermosets). This means that the materials to be welded will soften at high temperatures and harden at low (i.e. normal) temperatures. A good weld should create a ‘perfect’ mixture of the polymer ‘chain’ molecules, in a blended region formed from the surfaces of the two parts.
The ability of thermoplastic polymers to be both softened (or melted) and hardened, without any permanent changes to their properties, enables hot-melt, or thermal welding techniques to be used. Two plastic surfaces are pushed or pressed together after being softened by heat. They are then held together as the plastic cools and hardens, eliminating the boundary between the two parts. However, a variety in methodologies can be found in thermal welding techniques. Some of the common procedures are briefly described in the following section.
In solvent welding, the chemical solvent mingles with the polymer ‘chains’ in the plastic surface, which gives those polymer chains more freedom to move around each other and to mingle with those of an adjacent part. After two parts are pushed together, the solvent evaporates and then the blended polymer surfaces harden again over a short period of time (typically, a few minutes).
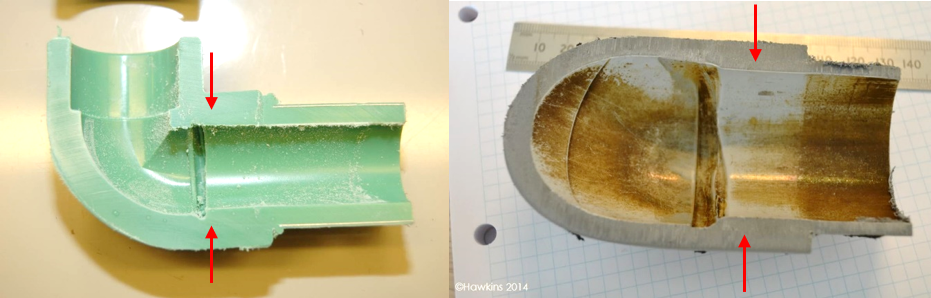
COMMON THERMAL PLASTIC WELDING TECHNIQUES
Heat sealing: A common technique in which heat is applied directly to the bonding surfaces, using a heated die or tool (sometimes a ‘bar’) to melt the pipe surfaces. This is common for plumbing-type pipework, where there will be a heated ‘male’ tool for the sockets of fittings such as elbows or couplers, with a ‘female’ tool for the pipe ends (see below).
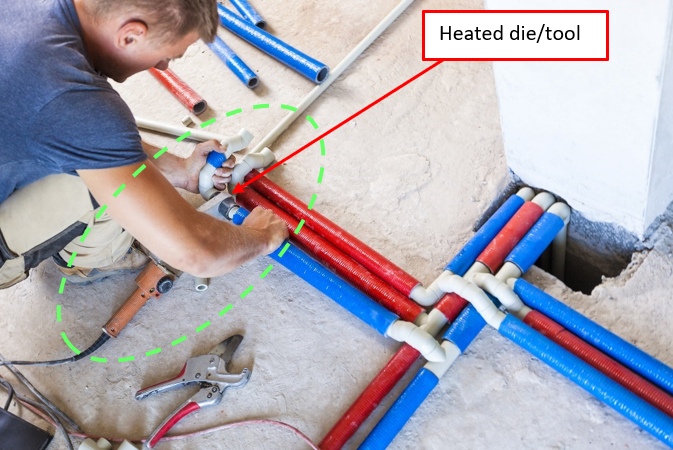
Hot plate welding: This technique is often used for relatively large or bulky parts, such as large diameter plastic pipes. The two parts (e.g. pipe ends) are placed in a tool on either side of a heated ‘plate’. Contact with the hot plate softens the pipe ends and the plate is then removed, so that the pipe ends can be pushed together before they cool. This creates a ‘butt’ joint between two lengths of pipe.
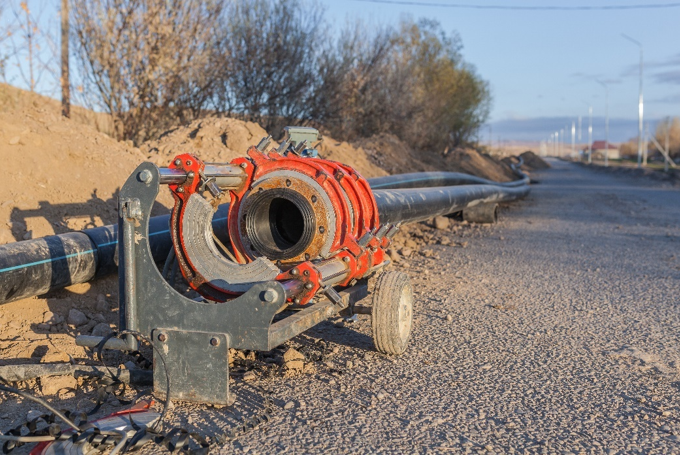
Electrofusion welding: This is another technique that is often used to join sections of plastic pipe. The pipes ends are placed into an electrofusion ‘welding socket’ or ‘collar’ (similar to a coupler fitting), which contains fine metallic wires that are heated with an electric current. A machine is then connected to the collar by a pair of cables that convey the electric current into the wires. The machine processes the weld automatically, by monitoring the temperature and time.
The following link illustrates electrofusion welding in a video clip (published to YouTube by KPS Petrol Pipe SystemTM): https://youtu.be/CIXvfBfrByw
Speed tip welding: In this technique, the welder uses a hand-held tool that is visually similar to a soldering iron to melt the plastic surface. The tool is fed with a plastic ‘weld rod’ (often through a tube), which adds filler plastic material between the surfaces to be bonded. This technique is commonly used for repairs (see below). Though it is often used with pipes, it is equally applicable to other plastic parts.
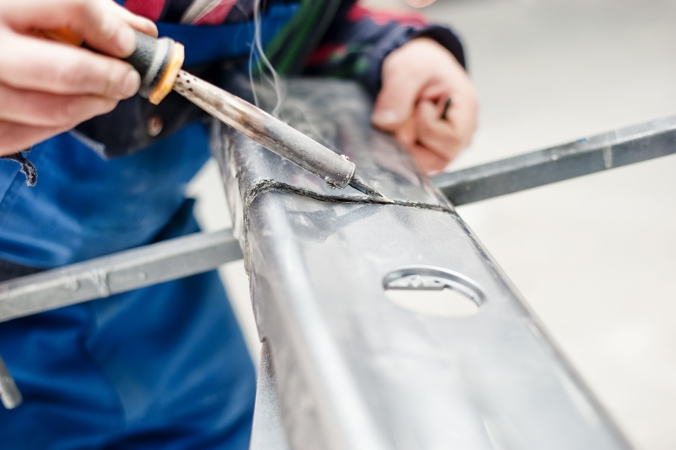
Infra-red / non-contact welding: This is broadly similar to hot plate welding, but it uses an infra-red (non-contact) heat source to soften the pipe (or part) surfaces. The lack of direct contact removes the risk of material being lost by ‘sticking’ to the hot plate, but this process typically uses more energy than a comparable direct-contact heating method.
Hot gas / hot air welding: This is another ‘non-contact’ thermal welding technique, which uses a hot air (or gas) ‘gun’ to soften the plastic surfaces, as well as a filler rod, to add material to the joint. This technique is also often used for repairs, as an alternative to speed tip welding.
Extrusion / injection welding: These techniques are used for large/bulky parts and they are usually conducted using a hand-held tool that ‘extrudes’ or ‘injects’ a stream (often called a ‘bead’) of molten polymer into the weld. Extrusion welding is usually used to weld the surfaces of large, bulky parts, whereas injection welding is primarily used for repairs. The ‘injector’ tip is usually narrower than an extruder’s and it forces molten polymer into a void, or a crevice, to fill it and effect a repair.
KEY CONSIDERATIOS FOR SUCCESSFUL PLASTIC WELDING
Successful plastic welding requires some knowledge, experience, and suitable planning; this is the case whether you are welding pipes, or any other parts. Firstly, the correct technique must be selected for the parts in question. For example, of the techniques described above, heat sealing is excellent for making many joints between relatively small diameter pipes, such as for plumbing in either a commercial or a large domestic building. By comparison, electrofusion, or a solvent-based technique might be more suitable for larger diameter pipes, such as the waste pipes in a commercial building. Hot plate welding would be more appropriate for large, regional water or gas distribution pipes. The details of the welding process must be considered, along with other concerns such as labour and energy costs.
From a technical point of view, there are some fundamental factors that must be considered to achieve successful plastic welding. These can be briefly summarised as:
- Weldability: some types of thermoplastic materials are inherently more ‘weldable’ than others.
- Selection of materials: dissimilar polymers do not usually blend well. The same, or very similar, types of plastic should be used to be successful.
- Surface preparation: dust, oil, grease, dirt, and moisture will inhibit the blending process. Oxidised or degraded surfaces might need to be removed before welding.
- Location and conditions of welding: difficulty of access to the parts (for example, when placed in narrow recesses or under high ceilings) can make successful welding very difficult to achieve. Also, the ambient conditions (e.g. hot/cold, humid/dry, windy, etc) will have an effect on the welding parameters, such as the time to reach a suitable welding temperature, as well as the time needed for the material to cool after joining.
Once the materials and the technique have been selected, and the preparation, conditions and parameters have been planned for, there are three primary factors to achieving a successful weld:
- Time: Sufficient time must be allowed for the welding surfaces to reach the correct temperature, to allow blending, as well as for the parts to cool again.
- Temperature: Sufficient temperature must be reached to achieve the correct degree of softening. However, too high a temperature might cause molten polymer to flow away from the joint, or cause bulk damage or deformation to the pipes/parts being welded. Each type of plastic and each individual component has a specific temperature range that should be worked in.
- Pressure: Sufficient pressure must be applied between the parts to promote mixing of the surfaces, but not so much as to either force the material away from the working area, or to damage the parts.
TYPICAL FAILURES OF PLASTIC WELDED JOINTS
Failures of plastic welded joints can be broadly categorised as:
- Cracks and cavities
- Inclusions
- Deformation
- Joint separations
Cracks and cavities: These can be caused by degradation of the polymer material; for example, by either exposure to heat, during or after the welding process, or by chemical exposure, such as from a solvent-welding technique. Such exposure might not cause immediate failure, but it might initiate a process of either slow crack growth, or one in which the generic properties and integrity of the plastic pipe deteriorate over time. If plastic pipework fails in this way, at or close to a welded joint, then one of the challenges for Hawkins’ forensic engineers is to determine whether the damage was caused or initiated either during the welding process, or afterwards, while the pipe was in service.
Slow crack growth is a relatively common failure mode in plastic pipework, by mechanisms such as environmental stress cracking (ESC). The example shown below is of a pipe that was thought to have failed by ESC, initiated by exposure to a chemical in the water that the pipes carried (after installation). However, similar-looking failures can be initiated by exposure to other chemicals, such as those used in solvent welding.
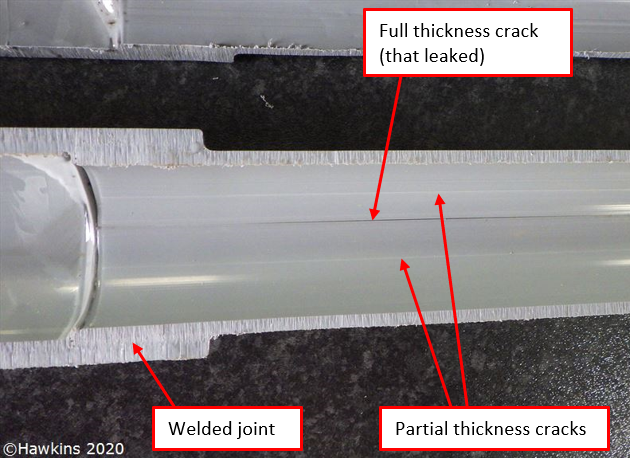
Inclusions: This refers to ‘foreign objects’ that become trapped within the weld material, while the plastic is softened. They are most commonly a result of poor surface cleaning and preparation, or can also be due to an unclean environment during the welding process. For example, it would be very difficult to avoid sand particle contamination if plastic welding was being conducted on a windy beach, or in a desert, without significant protection. Foreign particles can act as stress concentration and/or crack starter points, so if the pipework is exposed to a stress whilst in service, it can promote a mechanical (overload)-type failure. The presence of foreign particles will also reduce the overall strength and quality of a welded joint, so a diligent technician should take care to keep the welding material as clean as possible.
Another type of inclusion can be a ‘bubble’ of gas or air that becomes trapped in the weld material. This has a similar effect to a foreign particle, both by acting as a potential crack starting point, and also by reducing the overall strength of the weld.
Deformation: This type of failure comprises two main types. In the first instance, a joint can be overheated during the welding process, causing the bonding surfaces, and sometimes also the bulk material of the pipe to soften and become deformed. Secondly, two parts (e.g. a pipe and a fitting) might not be correctly aligned when they are welded, so this either forms an incorrect angle or position, or causes the pipe to not be inserted to the full depth of the fitting. Deformation failures are not always catastrophic, but they might cause problems by either disrupting the flow of liquid through some pipework, or by causing difficulties of fitting or application.
Joint Separations: This is one of the more common failure types in all pipework, including where it is joined by plastic welding. Separations are most often the result of an error during the welding process, which prevents a full-strength weld from being made. For example, the polymer surfaces might have been under-heated, either due to incorrect or incomplete contact with a heating tool (such as in heat sealing), or the parts might have been removed from the heat source too soon, before the correct temperature was reached.
The example shown in the introduction to this article was such a case. Insufficient heating prevented the pipe from being fully inserted into the elbow socket, and this meant that the component surfaces did not blend correctly. The images below illustrate the effect of that lack of heat on the integrity and durability of the joint, when a section of a failed joint was ‘crushed’ in the jaws of a vice and the same test was applied to a well-made elbow joint. In the well-made joint (on the left) remained intact, despite the pipe walls being pressed ‘flat’. However, the insufficiently heated joint (on the right) failed despite being deformed significantly less than the well-made joint. The lack of heat applied to the joint on the right meant that the bond strength was much lower than it should have been, due to incomplete blending of the polymer surfaces.
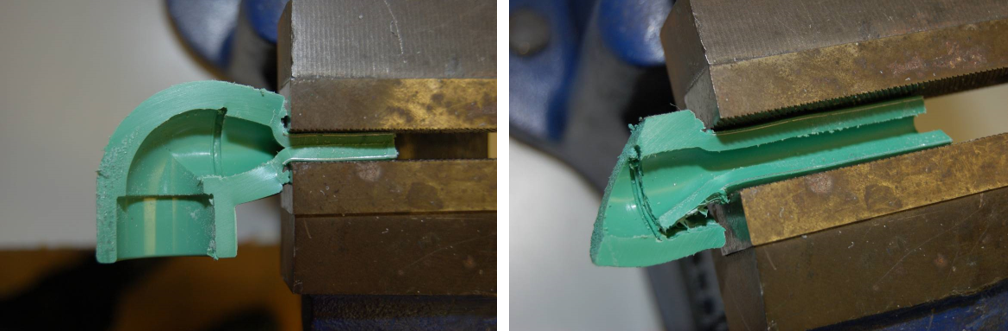
In another example of joint separation, a number of joints failed in ABS pipework that was carrying hot water in an industrial building. The joints had been made by solvent welding, and it was found that several of the joints had either fully, or partially separated at the mid-point of the welded joints (see below). However, no defects were visible there, when the joints were sectioned. At the heart of solvent-welded joints, there is often a ‘solvent affected zone’ (SAZ), where remnants of the solvent are still present, within the polymer material, as they have not fully evaporated.
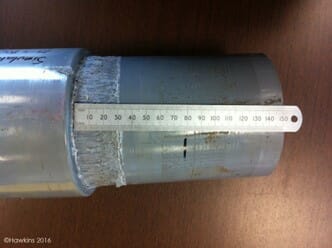
After investigation in this case, it was found that the glass transition temperature (Tg) of the ABS polymer was significantly reduced in the SAZ, compared to that of the ‘bulk’ material. In polymers such as ABS, the Tg is the temperature above which the material changes from a relatively hard and rigid material, to become soft, viscous, and ‘rubbery’. In parts of the pipework where the water temperature was highest, the Tg in the SAZ was exceeded, causing the joints to soften, so the internal pressure of the water pushed them apart.
Similar failures to that shown above can also occur where insufficient cooling (or evaporation) time is allowed before a joint is put into service. If the weld is not fully ‘set’ then (for example), the application of internal pressure might push a joint apart.
In conclusion, I hope this article has demonstrated that the welding of plastic pipes is a versatile process with numerous benefits. Those benefits include reductions in weight and cost (compared to the use of fasteners, or metal pipes), as well as aesthetic and water/gas tight joints that are strong, flexible and durable. However, achieving all of these benefits relies on good decisions being made about the materials and processes to be used, as well as correct and consistent execution, to create successful welded joints. Bad decisions and poor technique will lead to disappointment, and when plastic welded joints fail, the result is often a very sticky (and costly) mess! Hawkins’ engineers can provide expert assistance in determining the cause of these failures, as well as helpful guidance to prevent costly failures from reoccurring.
ABOUT THE AUTHOR
Jonathan Emm is a Chartered Materials Engineer, who investigates materials failures in metals, polymers and composites. He also investigates escapes of water and oil, personal injuries, forced entries, and fires. He has investigated several major loss incidents caused by the failure of welded plastic pipework in industrial and commercial buildings. Before joining Hawkins in 2007, Jon worked on aerospace materials engineering projects including radar absorbent coatings (stealth technology) and composite material structures for clients including Airbus, Lockheed Martin and AgustaWestland.