Industrial boilers in power stations and petrochemical plants produce steam for use both in power generation and as process steam. In these types of plant, the boilers are often fuelled using coal, oil or gas. Burning coal and oil generates ash, which requires periodic removal from the boiler in order to maintain efficient boiler operation. Though boilers are built with systems to handle boiler ash, if ash is allowed to build up inside the boiler, it can lead to boiler performance issues.
Though oil-fired boilers are still used in the Middle and Far East, Europe has phased out the use of fossil fuels. Gas-fired boilers do not have a problem with ash, while coal-fired boilers have their own separate issues with soot and ash, although do not experience the corrosiveness of oil ash.
Large, oil-fired boilers that generate power of more than 100 megawatts (MW) use a tower design; the superheater and secondary reheater sections are usually laid horizontally inside the boiler. The best way to the think of a boiler, is to compare it to a kettle: the term ‘superheater’ refers to the boiler’s ability to raise the steam temperature to above the traditional boiling point of 100°c. There are two issues associated with oil ash: so-called ‘ash bridging’ and oil ash corrosion.
Ash bridging occurs if the boiler’s cleaning regime is insufficient, and the spacing between its tubes is narrow. Boilers usually have sootblowers installed to prevent the build-up of soot and ash. Sootblowers are devices that divert a portion of steam and/or water into the furnace space of a boiler, in order to blow the soot and ash away from the surfaces of boiler tubes. The devices are designed to be either fixed or retractable, and can be operated either manually or automatically. However, if the sootblowers malfunction, or their placement and function does not operate as per design intent, it can lead to the build-up of ash to form ‘bridges’ between the tubes. This insulates the tubes and causes them to overheat.
The term sootblower is a historical name for the device, when unburned fuel created a problem by turning to soot, rather than ash. Although it is a bit of a misnomer in present times, the sootblower creates a shockwave which shakes the ash off of the boiler’s tubes or water walls.
Oil ash corrosion is an issue caused by the formation, during combustion, of a brown/yellow solid called Vanadium Pentoxide (V2O5) and a white solid called Sodium Sulphate (Na2SO4). The two compounds can mix to form a new compound, which melts at a lower melting point than either of their original separate melting points. This is called a eutectic mixture. The eutectic’s lower melting point reacts with the magnetite scale (Fe3O4) that normally forms on a boiler’s steel tubes and acts as a protective layer. However, removal of the magnetite causes the boiler tube material to corrode faster, leading to premature tube rupture.
An illustration of how oil ash corrosion occurs. The intermediate layer dissolves magnetite on the tube surface and reacts with the underlying tube material. ¹
For horizontally-laid boiler tubes, ash-related corrosion issues are likely to occur on the tops, or ‘crowns’, of the tubes. At 530°C the ‘critical ratio of Vanadium to Sodium is typically 3:1, which causes the eutectic to form, but at higher temperatures, this ratio widens to become a range of values.
Tube thickness measurements using Ultrasonic Testing (UT) methods can confirm if metal loss has occurred, and if that is consistent with fireside corrosion, i.e. corrosion that occurs on the outside of the tubes. Metal loss causes the metal temperature to increase, promoting thickening of the bore oxide, which is a compound that acts as an insulator and inhibits heat transfer to the steam, exacerbating overheating of the metal. The thermal conductivity of magnetite is much lower compared to steel, which explains why magnetite hampers the transfer of heat from the flue gas into steam. In cases such as this, the tube’s temperature increases dramatically so reducing the tube’s life very significantly.
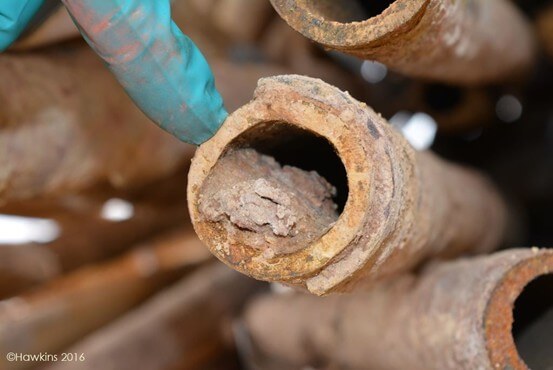
If the internal oxide builds up, it can cause partial steam starvation, leading to further tube overheating of the partially blocked tube and premature rupture. The thick bore oxide layer, which can also be measured using UT methods, can also indicate that the tube is running hotter than expected.
Boiler tubes are commonly made using low alloy carbon steels. If corrosion is an issue, one option is to replace the steel with a stainless steel. If this option is being considered, it should be done in the context of reviewing both boiler operation, and fuel oil use and treatment, in more detail.
In light of the worldwide trend towards a low or zero carbon economy, it is likely that oil-fired boilers will be phased out over time. However, it is prudent to make efficient use of fuel oil for power generation until renewable and low carbon energy solutions become increasingly prevalent.
About the Author
Paul Moody completed his undergraduate degree in Metallurgy and later completed his Doctorate, researching the fracture properties of welded structural steels in relation to the oxygen content of weld metals. Paul began his career at the Defence Research Agency as a Research Scientist, researching welding of high strength naval steels and investigations of failed components and moved on to become a metallurgist before joining Hawkins in 2017. Paul’s experience includes facilitating contract materials testing for the offshore oil and gas services industry, performing remanent life assessment on boilers for power plants and petrochemical sites, investigating failed components, and providing support on materials related issues.
¹ Source: https://www.powermag.com/the-role-of-fireside-corrosion-on-boiler-tube-failures-part-i/