Hawkins is often instructed to investigate escapes of oil products such as kerosene heating oil and diesel from storage tanks, and pipelines in domestic and commercial situations, as well as within and on the roofs of buildings. This article provides a brief overview of the different Regulations, Standards, and guidance that is applicable in these different locations. This article does not consider the storage of diesel or petrol at petrol filling stations or at tank farms where many thousands of litres of fuel are stored in large cylindrical tanks, as they are covered by different regulations and industry guidance.
Kerosene, or the more viscous gas oil, is often stored in above-ground metal or plastic tanks for use in space heating and the heating of water in rural areas or anywhere there is no mains gas supply. Diesel is similarly stored for use in standby generators. Metal or plastic pipes then convey the oil to a boiler or generator located within, or on the roof of, a building or in a weather-proof enclosure.
OIL STORAGE REGULATIONS
In England, the design and use of most oil storage systems is regulated by The Control of Pollution (Oil Storage) (England) Regulations 2001. Similar Regulations are present in Scotland from 2006, in Northern Ireland from 2011 and in Wales from 2016; copies of these Regulations can be found on the internet. These Regulations are largely legal forms of the guidance already provided by existing British Standards and guidance from the Oil Firing Technical Association (OTFEC). Separate guidance is also provided by the Environment Agency (including the equivalent organisations in Scotland and Northern Ireland). Oil fired appliance manufacturers also provide guidance on oil supply systems, as well as the design and maintenance of their own equipment.
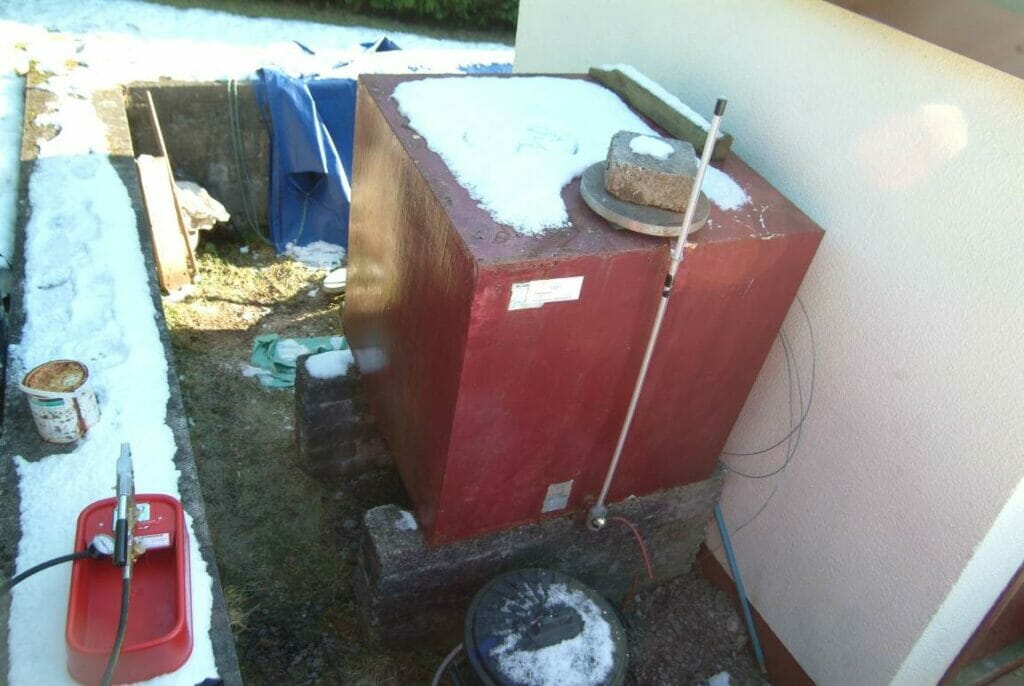
While there is a myriad of sources of information, they all tend to agree on the fundamental requirements, which are discussed below.
In general, the Regulations apply to any oil storage tank containing heating oil and the associated supply pipe, provided it is not in a building or totally underground, has a capacity of 200 litres or less, or serves a private dwelling. In England and Northern Ireland, the Regulations do not apply to tanks serving private dwelling that have a capacity less than 3,500 litres, the Scottish Regulations apply to domestic tanks with a capacity greater than 2,500 litres and the Welsh Regulations only apply to tanks installed after 2016 regardless of capacity. This means that in England and Northern Ireland a 2,500 litre tank serving a house is not covered by the Regulations, but the same system serving a place of business would be, and any tank with a capacity greater than 3,500 litres would have to comply with the Regulations.
Where applicable, the Regulations also require the tank, sight gauge, filter and vent pipe to be contained within an oil-proof bund that has a capacity of 110% of the tank. Any sight gauge must be properly supported and have a self-closing valve to isolate the sight gauge tube when not in use. Pipes should be adequately supported above ground and adequately protected from damage if buried below ground. No joints should be present on buried pipes unless the joint is accessible under a removable cover, and the pipe should either be fitted with a tested leak detection system, or be tested for leaks before it is put into service, and on a regular basis thereafter. Pipes should also be protected from physical damage and either be made from corrosion resistant materials, or be protected from corrosion.
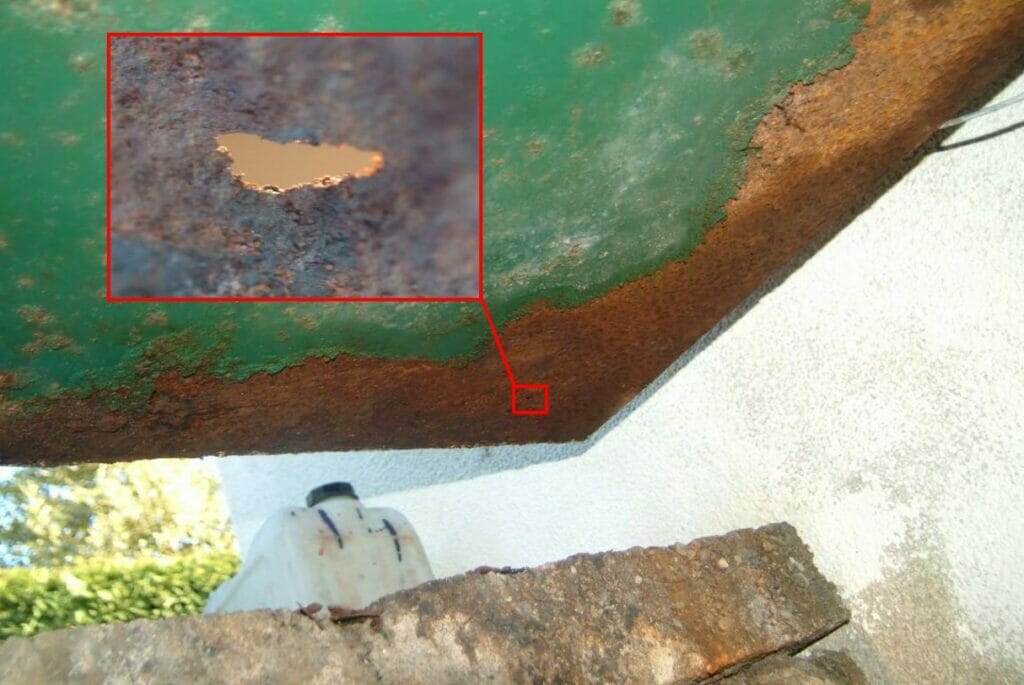
Since the late 1970s, pre-dating the Regulations, guidance on the design, installation and maintenance of oil fired appliances, and the systems storing and supplying oil to them, has been described for the whole of the UK in British Standard BS 5410 parts 1, 2 and 3. Part 1 covers most domestic-type installations, Part 2 covers larger commercial installations, and Part 3 covers industrial installations such as kilns, ovens, furnaces etc. These documents provide guidance similar to the Regulations, but also provide advice on the siting of oil tanks to reduce the risk of fire spread to the tank, how tanks should be supported and how the tanks, bunds and supply pipelines should be maintained. The recommendations in these standards are very similar to that provided by OFTEC and the documents often refer to each other.
INSPECTING OIL STORAGE TANKS
OFTEC provides guidance for the manufacture, installation and maintenance of oil equipment such as tanks, gauges and other fittings for use on oil storage and supply systems as well as for the installation and maintenance of oil fired equipment (e.g. boilers). This guidance is in the form of OFTEC Standards and Technical Guides. Of particular relevance is the section on the inspection of oil storage tanks, which states that all tanks should be inspected annually (often as part of an annual service of the boiler). Steel tanks should be inspected for signs of corrosion (See photographs 1 and 2) and distortion, as leaks can occur through both internal and external corrosion and the failure of welded seams.
While the above applies to technicians carrying out routine maintenance of oil storage and supply systems, contractors delivering oil to tanks also have a responsibility to ensure that the tank is suitable and safe to accept the volume of oil being delivered.
Plastic tanks (as displayed in the main image) should be inspected for signs of cracking, bulging, discolouration and the occurrence of a white “chalk-like” appearance and it is well known that some plastic tanks have cracked due to defects occurring from the manufacturing process (see photographs 3 and 4). The owner of the tank or the person responsible for the maintenance should be advised in writing about any concerns and tanks at risk of catastrophic failure should be replaced immediately.
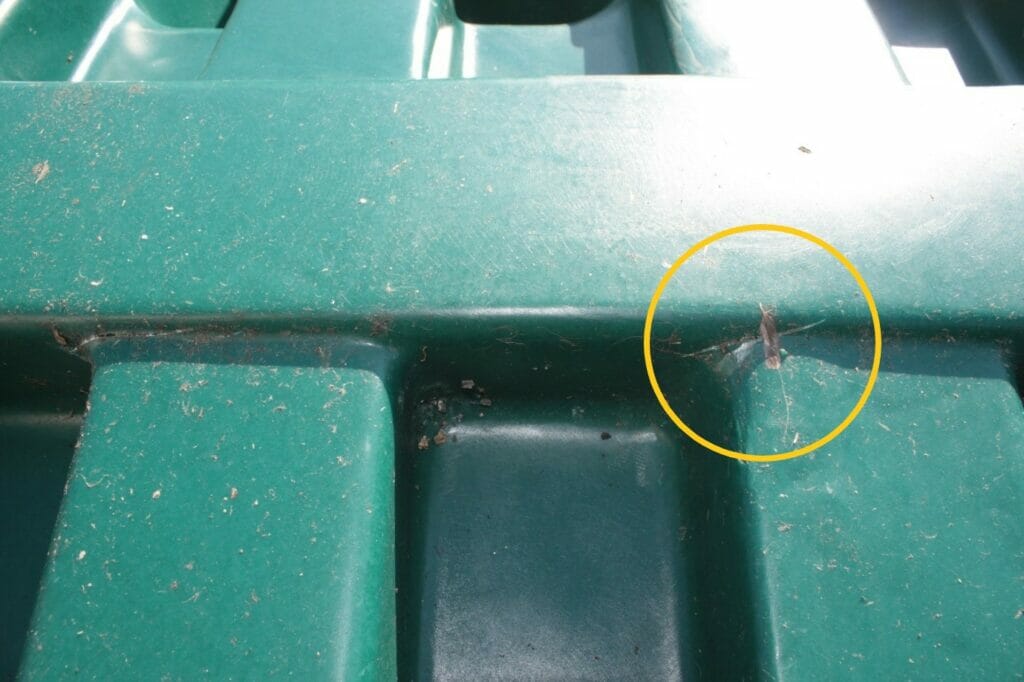
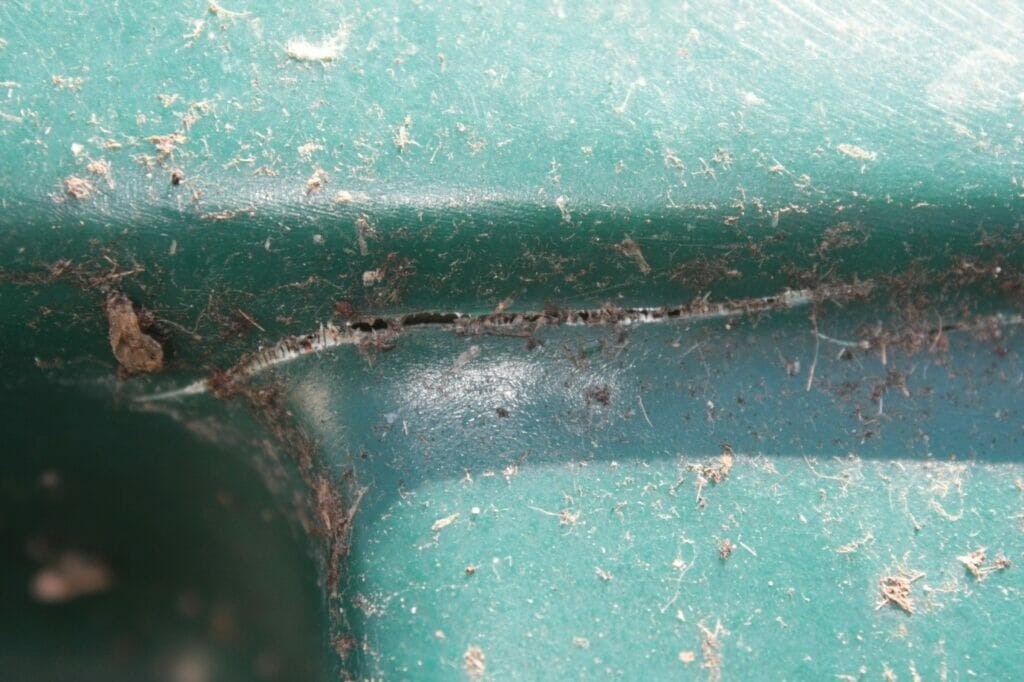
Photographs 3 and 4: Cracking at the corners on a typical plastic tank.
OIL TANKS STORED UNDERGROUND OR INSIDE A BUILDING
The use of underground tanks to store heating oil is unusual, but where this is necessary the British Standards recommend that the tank be protected from corrosion, be installed within a secondary enclosure to contain any oil that escapes from the inner tank, and arrangements be made to prevent the tank from floating should the ground water level increase. The Environment Agency also recommend that a monitoring system with an audible alarm be installed between the inner and outer tanks to detect the presence of any liquid (e.g. oil or water) and alert the person responsible for the tank. The use of underground tanks is common in petrol filling stations, but they are covered by separate regulations and guidance from the Local Authority and the Energy Institute (formerly known as the Institute of Petroleum).
Where oil tanks are sited in, or on, buildings, the requirements for fire resisting structures are described in the Building Regulations, OFTEC guidance and British Standards. The requirements cover the fire resistance of enclosures and the bunding of any tank sited within a building regardless of its capacity provided it is over 200 litres. Oil leaking from a tank or the pipework directly connected to the tank should therefore be contained within the bund and not spread into the building structure.
However, Hawkins has investigated several incidents at commercial premises where either heating oil or diesel serving a standby generator is stored at ground level in a large tank and is automatically pumped to smaller day tanks, either within the building or on the roof. Leaks have occurred on such installations where the pump system malfunctions and overfills the day tank, so that the oil escapes through vent pipes on the day tanks (Photograph 5). This generally passes unnoticed, as the system is automatic, so the escaping oil can fill the bund and overflow from it to contaminate the building fabric as well as any rainwater run off systems (e.g. gutters, downpipes and drains).
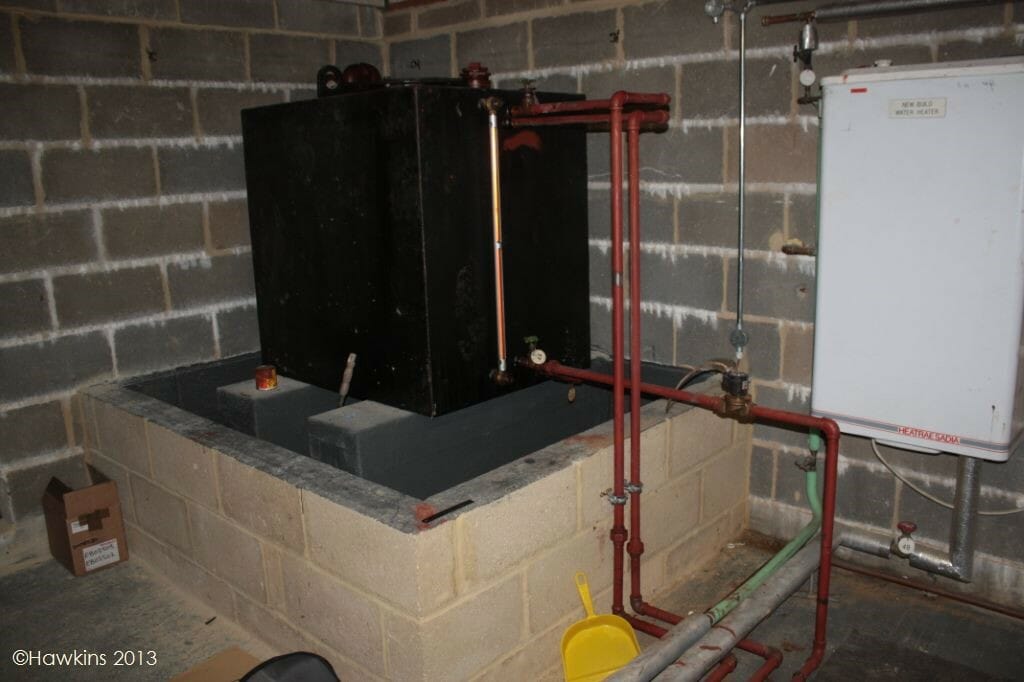
The design of pumped systems is covered by BS 5410-2 and essentially requires there to be an adequately sized overflow pipe to return surplus oil from the day tank to the main tank. However, these overflow pipes can become clogged through a lack of maintenance or left damaged from a lack of awareness of their purpose. There is also a recommendation that a float-operated switch be used to control the pumps and switch them off once a predetermined oil level in the day tanks has been achieved. However, such switches can malfunction or be bypassed, again through a lack of understanding on the part of a building owner or operator.
ABOUT THE AUTHOR
Patrick Barbour is a Chartered Mechanical Engineer, who has worked in the North Sea oil industry and in academia. He has over 15 years of experience of forensic investigations and has carried out many investigations where fuels such as diesel, kerosene or petrol have escaped from storage tanks and pipelines. These cases have involved domestic and commercial installations and tanks farms.