Chemical flux in plumbing systems is ubiquitous in the formation of most plumbing systems.
Flux is an aggressive, acidic paste that is applied to the surfaces of copper pipes and fittings prior to soldering. Soldering is a process by which two metal pieces are joined together using a filler metal, aptly named solder.
The purpose of flux is to remove the natural oxide layer that is present on the surface of copper. If this layer is not removed, it will prevent the solder from adhering to the copper, and so prevent the formation of a satisfactory joint. If flux is either not properly flushed out from the pipes after installation, or becomes entrapped in the solder, then corrosion of the copper pipe may occur, and cause pin-holing over time. To prevent this, flux should be used sparingly, and the pipes should be flushed with water as soon as possible after completion of the pipework.
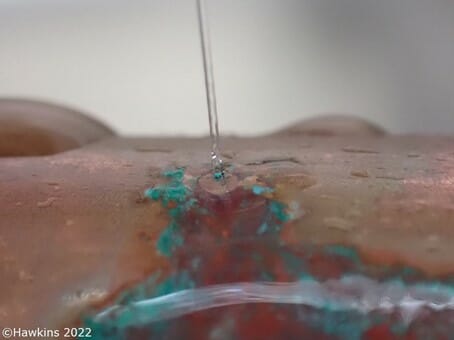
The Water Supply (Water Fittings) Regulations 1999[i] states that, “Every water system shall be tested, flushed and where necessary disinfected before it is first used”. The “Solders & Fluxes” guidance available from WRAS (The Water Regulations Advisory Scheme) states that:
“The internal pipe work and fittings should be flushed as soon as reasonably practicable to remove any flux residues or filings. Factors that should be taken into consideration when determining what is reasonably practicable include:
– Whether or not there is likely to be debris in the system
– The complexity of the system, and whether it would be appropriate to consider staged flushing
– The possibility of the flux drying out.”
All pipework should be commissioned in accordance with the Regulations and WRAS guidance, and particular care should be taken to flush out any excess flux from soldered pipework to avoid corrosion in years to come.
When copper pipework is installed, and is put into regular service, copper reacts with oxygen to form a mixed layer of copper oxides and copper carbonates on the inside surface of the pipe. This layer protects the copper pipe from corrosion or dissolution. However, if this protective layer fails to form, copper can start to degrade, and degradation issues may arise. Poor plumbing practices, such as the over-use of fluxes whilst making solder joints, can exacerbate such degradation issues.
Corrosion of copper pipework due to flux often takes many years and occurs near to soldered joints, either within the joint or on the metal solder run lines leading away from joints.
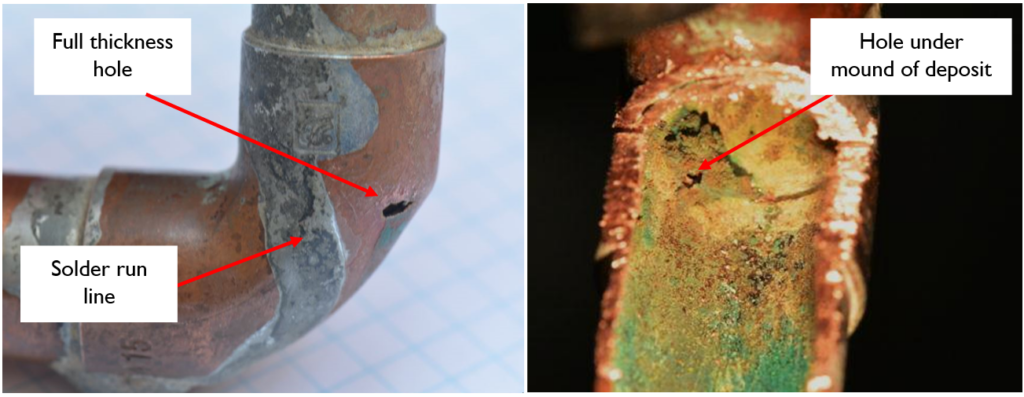
Common fluxes in the current market are based on either zinc chloride, ammonium chloride or hydrochloric acid. Fluxes can contaminate copper pipework both in the vicinity of the joint, and further away from it, due to the rapid evaporation of the flux when it is heated to make the joint.
In the following case study of an escape of water, after the cause of the escape was discovered, the pipe sample was viewed using a scanning electron microscope (SEM) and examined with energy dispersive X-ray spectroscopy (EDX).The results indicated that the protective copper oxide layer had formed on the inside of the pipework. However, crystalline deposits were seen directly on the surface of the copper pipe.
Chemical analysis of these crystals showed that they contained high concentrations of chlorine, the most common constituent of solder flux, often in the form of zinc chloride or ammonium chloride. Both of which are, by their nature, aggressive to copper.
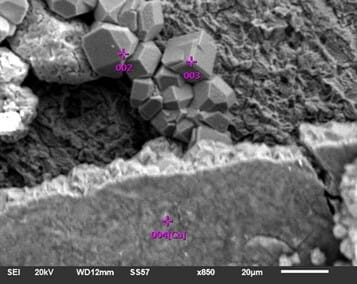
The location of the deposits, directly on top of the copper pipe and not on the protective layer, suggests that these chlorine-containing deposits came into contact with the pipe both before it was put into service, and before the protective layer had time to form (i.e. the chlorine containing particles were deposited when the solder joint was made, prior to commissioning of the pipework).Contamination of the copper pipe from excess flux would cause the copper pipework to corrode and over time can cause pin-holing.
Copper pipework is not the only material that can be damaged by flux. Flux can also cause catastrophic damage to steel components, such as flexible steel gas pipes and plastic components if it is allowed to come into contact and contaminate them.
Polymers comprise long molecular chains which can be affected by aggressive chemicals (such as flux, acids, alkali and amines etc).Depending on the type of chemical and polymer, the degradation can take different forms, such as:
- Chain scission—which reduces mechanical properties
- Depolymerisation—which leads to crazing and crack formation
- Hydrolysis—which causes the polymer to break down
- Oxidation—which results in chain scission and property loss
All of these degradation mechanisms can be catastrophic to the polymer and can lead to a complete failure of the object in question.
Our next case study image shows a plastic push fit fitting made of acetal polymer which is in close proximity to copper soldered joints. In this case there was evidence to indicate that flux had run down the pipework towards the plastic joints and had also been dripped onto the fittings, most likely during the soldering process. The subsequent degradation of the polymer after exposure to flux and normal water pressure, caused the end of the fitting to fracture and break off from the main body. As a result the fitting was no longer watertight nor mechanically secure. The flux degraded the polymer bonds, weakening them such that there was general material loss and that the fitting cracked and broke under normal water pressure.
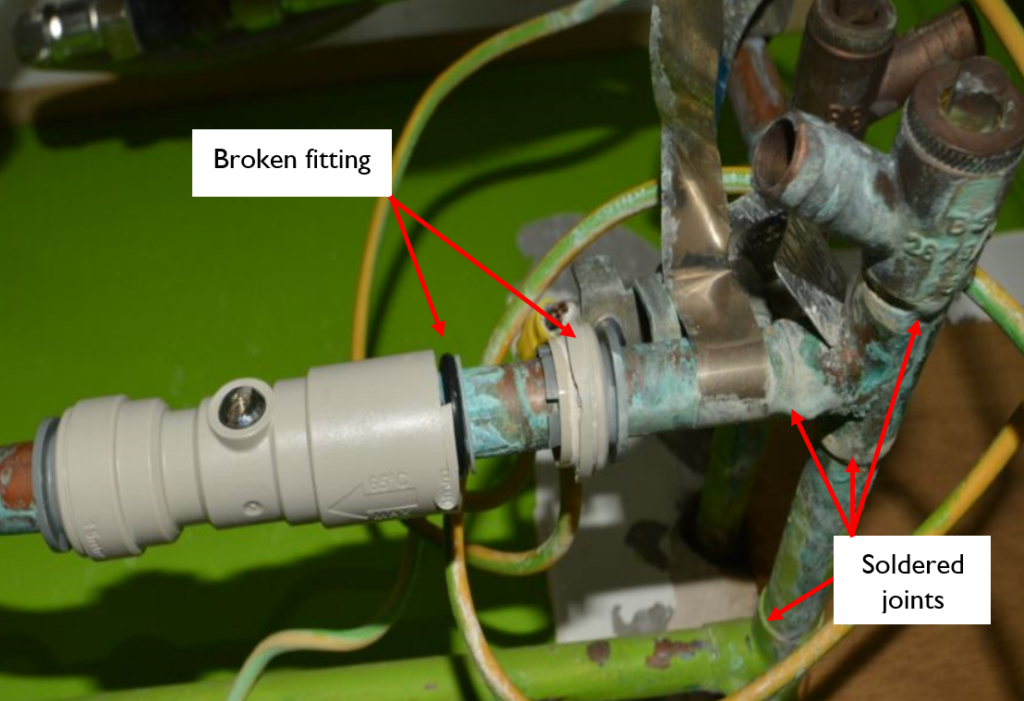
In a further case study, another type of plastic push fit fitting had flux dripped on it when a soldered joint was installed nearby. In this scenario, flux dripped down into the joint and degraded the collet (a collar in the fitting), which contains backward-facing metal teeth and provides mechanical security to this kind of joint. The degradation of the collet caused the fitting to fail, because the mechanical security was lost, and an escape of water then resulted.
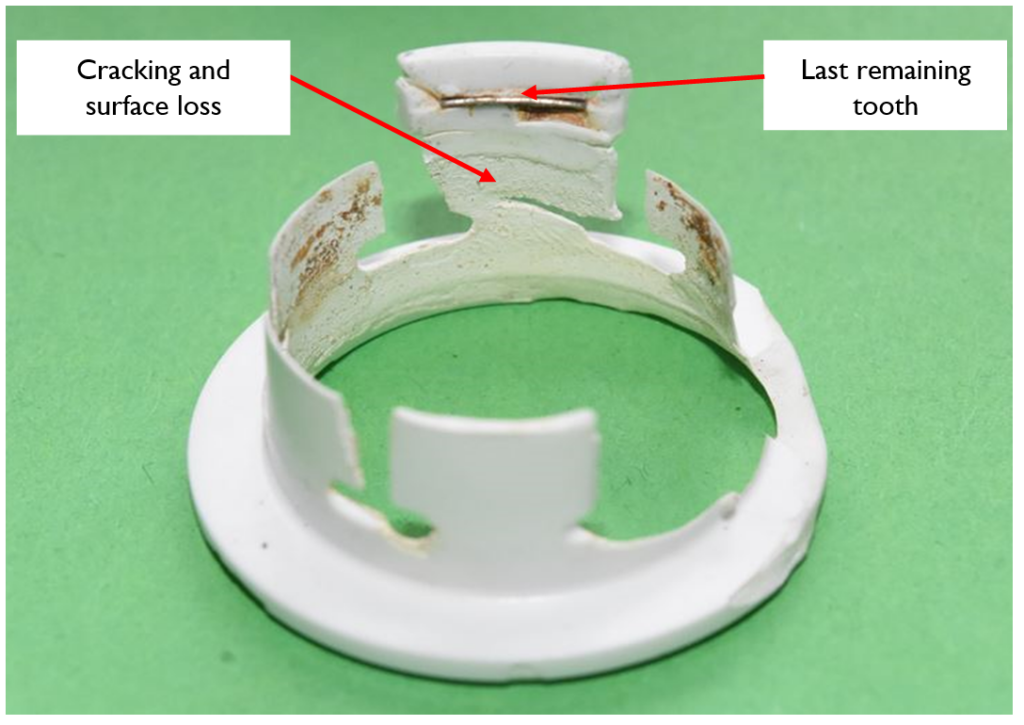
In all the examples discussed here (both metals and polymers) the items have failed due to contamination with chemical fluxes. It does not follow that all fluxes are aggressive to polymers and metals. Many chemical fluxes still contain either zinc chloride or ammonium chloride, which are known to be aggressive. To this end, many manufacturers will stipulate the importance of preventing contamination from such chemicals, and the onus is on the installer to ensure both that plumbing systems are flushed, and that contamination is limited. If contamination occurs, installers must ensure that the affected parts are thoroughly cleaned to prevent either degradation or escapes of water, fuels or gasses. In cases such as these, recovery is often very easy to achieve, providing the evidence has been protected. If you ever come across a situation where you think that there might have been chemical contamination of a product, which has led to degradation, I would be more than happy to discuss the case with you.
ABOUT THE AUTHOR
Dr Eleanor Jay is a Fellow of the IOM3, Chartered Engineer and Chartered Scientist who has a background in materials science and specialises in material failures. With Hawkins, Eleanor has specialised in investigations of material failures (ceramic, glass, polymers, metals), metallurgy, escapes of water, oil and other fuels, mechanical system failures, and personal injuries.