Bolts are critical components in structural steel connections that effectively govern their performance, particularly during fires where robustness becomes an important factor. In this article we explore the fundamental ways in which bolted connections can fail and some of the options available to achieve better performance.
Background
During a fire, the ability of the beam elements in a structure to develop catenary action is largely governed by the rotational capacity and strength of their connections. Investigations carried out on different connection configurations have shown that their failure temperature can be increased by avoiding the premature failure of the bolts.
There exists a substantial body of research that focuses on specific aspects of bolt assembly performance at ambient temperatures (e.g. friction between mating threads, nut tolerance class, number of threads in the grip, pretension force, etc.). This work underpins the current international design regulations. At elevated temperatures the picture is substantially less complete, with many of these parameters remaining unevaluated.
Prior to 1995, national design standards did not assess the behaviour of steel joints under fire conditions because the thermal mass of the joint area is much greater than that of the incoming structural members. However, observations from full-scale fire tests have subsequently shown that steel connections occasionally fail at elevated temperatures, particularly their tensile components.
Bolt Assembly Failure Modes
Applied tension forces
There are two dominant tensile failure modes at elevated temperatures: necking failure and stripping failure. The former is a ductile failure mode due to substantial plastic deformation occurring in the bolt shank (typically in the threaded part). Stripping failure occurs when the engaged threads experience large shear deformations that eventually result in the nut disengaging and often occurs in a brittle mode. Necking failure is preferred in practice as it provides a ductile connection with appreciable rotational capacity.
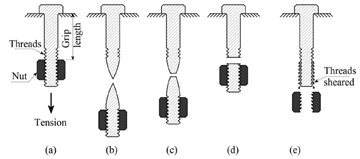
In most practical applications, partially-threaded and fully-threaded bolts are the most widely used. Partially-threaded bolts have a grip length below the bolt head free of threads while fully-threaded bolts have threads that run from just under the head all the way to the tip. Stripping failure results in the complete loss of bolt tensile strength, thus certain precautions should be considered to reduce the likelihood of this mode of failure. For partially-threaded bolts this can be achieved by using a nut with tighter tolerance class or a nut with higher class property. Additionally, the strengths of the bolt and the nut threads should be similar as it is shown that differences can result in the stripping of low strength threads. For fully-threaded bolts, stripping failure is highly likely to occur even with these precautions; avoiding stripping failures in this context is the subject of ongoing research.
The use of coatings, are essential for protecting high strength bolts in corrosive environments, such as offshore installations. However, such coatings and finishes can lower the coefficient of friction between mating threads at elevated temperatures, increasing the propensity of a stripping failure. This is due to the protective coatings having a lower melting point than the parent material of the bolts. A common coating is zinc which melts completely at 420°C. As such, the use of coated bolts at temperatures exceeding half the melting point of the coating is not recommended. It is also noted that molten coatings are a primary cause of liquid metal embrittlement. One feasible solution is to use material that has inherent-corrosion resistant characteristics such as stainless steel.
Applied shearing forces
Failure of shear connections at elevated temperatures can occur in various ways, including the shear failure of the bolts, bearing failure of the plate against the bolts, and rupture of the plates. Shearing forces typically result in brittle failure modes at ambient temperatures, however tests have shown that the ductility of shear connections increases at elevated temperatures. Whilst stripping failure is not commonly observed in shear connections, tension forces arising due to plate prying action have been observed. Thus, bolts under shear may experience considerable tensile forces depending on the connection configuration and flexibility of the connected plates, which can reduce the shear capacity of the bolt due to a combined stress effect.
Metallurgical failures
There are numerous metallurgical failure modes including corrosion (general, pitting and crevice), stress corrosion cracking, galvanic corrosion, liquid metal embrittlement, temper embrittlement, and hydrogen embrittlement. The latter three types are particularly affected by elevated temperatures.
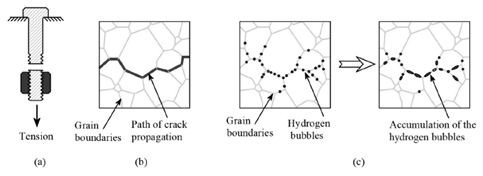
Liquid metal embrittlement (LME) failure is due to the instability of platings and coatings at high temperatures. LME of galvanized steel bolts occur when there is a simultaneous application of stress and high temperature. A surface layer of liquid zinc is present and when a tensile stress sufficient to cause surface cracks is applied to a galvanised steel bolt, the liquid zinc flows into the crack tips. This weakens the cohesion of grain boundaries, enabling the cracks to propagate easily into the steel matrix as seen in Figure 2(a) above. Accordingly, the bolt then fails instantly in a brittle manner.
Temper embrittlement (TE) is an intergranular failure caused by the reduction of the cohesion along grain boundaries, ultimately leading to a brittle failure mode; Fig 2(b). It is a characteristic failure for alloy steels that are tempered or heated in the range of 375−575°C and then continuously cooled at a slow cooling rate. The susceptibility of bolts to fail by TE is also affected by the alloying elements. In particular, the most widely used alloying elements such as nickel, manganese, and chromium, enhance TE failure. When bolts containing these alloying elements are exposed to elevated temperatures in this range and then continuously cooled, they may still be susceptible to brittle failure even if the bolt strength has not been affected. Thus, despite it being well-documented in the literature that the ductility of the bolt increases with increasing temperature, TE shifts the ductile-to brittle transition temperature to a significantly higher temperature, which can result in a brittle failure during a fire event.
High strength bolts are susceptible to failure by hydrogen embrittlement (HE). A source of hydrogen is required for HE to occur, which can be secured during the zinc electroplating process for galvanised high strength bolts or exposure to elevated temperatures in hydrogen containing environments. The tensile capacity and ductility of the high strength bolts significantly deteriorates due to the pressure exerted by the hydrogen bubbles that form on the metal grains as seen in Figure 2(c). The bubbles result in the formation of microcracks that grow and propagate with or without externally applied loads, with eventual failure occurring anywhere between hours or years after the bolt was first fabricated.
Fire Effects on Bolted Connections
Thermal loading
The damage to a steel bolted connection is largely controlled by how much heat is absorbed by its components. Predicting the extent of this thermal loading is challenging due to both the relative complexity of connection assemblies and the difficulties arising from modelling the heat source. The high thermal conductivity of steel ensures a high degree of heat transfer from the fire to the connection components. However, due to the relatively high mass concentration at the joint and the presences of gaps between plates, connection assemblies typically exhibit an uneven temperature distribution. Moreover, the fire location with respect to the connection is important for accurate thermal analysis, considering that the heat transfer is mainly radiative when the fire reaches its peak value.
The forces that develop in bolts during a fire depend on the type of connection and the fire phase (heating or cooling). Figure 3 illustrates the typical forces on bolts during the heating and cooling phases for moment and shear beam-to-column connections. For moment connections, the tensile force in the bolts tends to reduce with increasing temperature due to the incoming beam undergoing expansion and exerting an opposing compressive force on the connection. For shear connections on the other hand, the force on the bolts tends to increase with the temperature, providing that the gap between the beam and the column flange is larger than the beam elongation during fire. Thus, the bolts in connections designed to carry only shear are more vulnerable to failure during the heating phase and before developing catenary action. In some scenarios, other factors such as the elongation of the bolt holes within the beam web and an increase of the bolt ductility with temperature may improve the connection shear behaviour.
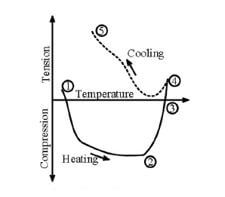
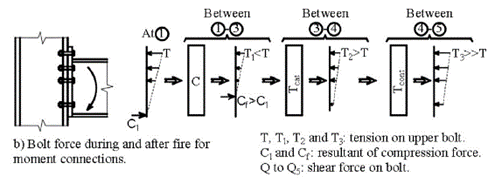
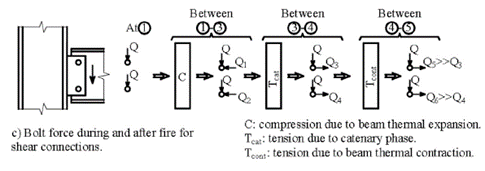
If the fire is extinguished prior to any connection failure, the contraction of the steel beam during the cooling phase results in considerable tensile forces developing in the connection and the bolt. Whilst it is arguable that the full bolt strength is restored as the temperature decreases, this is based upon the incorrect assumption that the residual strength of high strength bolts is reversible because of cooling. However, the residual strength of bolts depends upon various factors including the maximum attained temperature, the duration of the fire, and the cooling rate, all of which ultimately control the metallurgical phase transformation. This frequently results in a significant reduction in bolt capacity even after the fire is extinguished.
Effect of bolt failures on connection performance
Experimental work carried out on moment-resisting beam-to-column connections has shown that bolt stripping results in a premature failure of the connection, significantly compromising its rotational capacity, which is important for developing catenary action. In tests it has been observed that premature connection failures by stripping can occur at a rotation of 1.5°; when stripping failure is avoided (e.g. by using a double nut bolt configuration) the rotation capacity increases to approximately 7°. For shear connections, researchers have observed that the failure mode transitions from plate bearing at ambient temperatures to bolt shear at temperatures beyond 500°C.
Final Remarks and Summary
The structural fire performance of bolts is a complicated subject with limited formal guidance being available in British and European codes and standards (Eurocode 3 Part 1.8). These rules provide simple temperature-dependent reduction factors, but they do not consider modes of failure. Additionally, special bolt grades (e.g. high strength) and materials (e.g. stainless) are available for use at ambient temperatures, but these are not yet accounted for in current design rules. In summary:
- There are two predominant modes of bolted connection failure at elevated temperatures: stripping and necking.
- Necking failure is a ductile failure mode and is desired as this promotes a robust connection capable of sustaining the tensile forces that develop from the beams acting as catenaries during a fire.
- Partially threaded bolts are less susceptible to stripping failure than fully threaded bolts.
- Care should be taken when specifying bolts with special coatings, such as zinc, in fire critical regions of a structure.
- After a fire, a bolt may not exhibit the same material characteristics as it did prior to the fire. Furthermore, significant stresses may remain locked into the connection due to permanent deformations in the connected structural components.
About the Author
Andrew is a Chartered Engineer (CEng) with the Institution of Civil Engineers (MICE) and the Institution of Structural Engineers (MIStructE). Whilst working at the Earthquake and People Interaction Centre (EPICENTRE) he undertook ground-breaking research into tsunami loading on buildings, developing a set of new force equations for design.
He was an elected member of the Engineering and Physical Sciences Research Council (EPSRC) Early Career Forum in Engineering and remains an elected member of the EPSRC Peer Review College in Engineering. He is an invited reviewer for numerous leading international journals, including Thin-Walled Structures, Structures and the ASCE Journal of Structural Engineering. Andrew is the author of 25 scientific articles, all of which are published in internationally leading journals. He is an external PhD examiner for the University of London and UCL.
Andrew’s recent focus has predominantly been working on existing bridges, performing structural assessments, producing concept designs, and developing repair solutions. Work included the Hammersmith Bridge, for which he was the modelling lead for the concept design to be implemented.
Further reading
Behaviour of stainless and high strength steel bolt assemblies at elevated temperatures—A review.
MA Shaheen, ASJ Foster, LS Cunningham, S Afshan
Fire Safety Journal 113, 102975
A numerical investigation into stripping failure of bolt assemblies at elevated temperatures.
MA Shaheen, ASJ Foster, LS Cunningham, S Afshan
Structures 27, 1458-1466
Performance of axially restrained carbon and stainless steel perforated beams at elevated temperatures.
MA Shaheen, S Afshan, ASJ Foster
Advances in Structural Engineering 24 (15), 3564-3579
Bolt stripping failure and ductility of end plate beam-column connections at ambient and elevated temperatures.
MA Shaheen, LS Cunningham, ASJ Foster
Journal of Structural Fire Engineering 14 (2), 167-184
Selecting Suitable Bolt Parameters to Achieve Ductility at Elevated Temperatures.
MA Shaheen, ASJ Foster, LS Cunningham, S Afshan
ce/papers 4 (2-4), 1191-1195