
This article was also published in Issue 9 (page 52) of The Marine Insurer. Click here to read more about their publication and see other issues.
When transported or stored in bulk, coal can be hazardous because:
- it can create a flammable atmosphere
- it can self-heat
- it can deplete the oxygen concentration and,
- it can corrode steel structures
All of these properties are especially hazardous in a marine context and as such the International Maritime Organisation Solid Bulk Cargos (IMSBC) Code provides specific guidance for ship Owners and Masters on the safe carriage of coal. Central to the Code and the safe carriage of coal is regular and reliable monitoring of the gas within the cargo holds and surrounding spaces. The IMSBC Code requires that vessels transporting bulk coal should carry appropriate instruments for remotely measuring the methane, oxygen and carbon monoxide concentrations within a cargo space, i.e. without requiring entry into the cargo space. (The Code also requires the ship to carry equipment to measure the pH of cargo space bilge samples).
GAS DETECTION AND MONITORING EQUIPMENT
At Hawkins, we use a range of detection and monitoring equipment, the most popular and modern of which is the Draeger X-AM 8000. However, it is also expensive both to purchase and to maintain. Therefore, the devices commonly used on most coal carrying ships are the less expensive handheld gas detectors, similar to the BW Gas Alert Max XT II, pictured below.
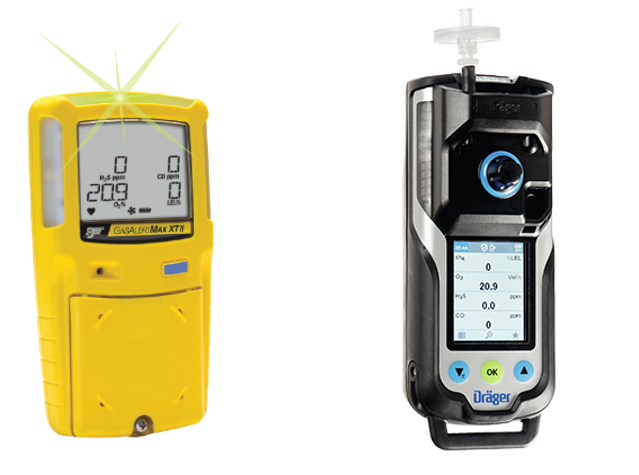
The sensors employed by these gas detectors are fitted into the body of the device and the gases are sampled either by diffusion or through a flexible tube and a length of spark-proof metal tubing fitted with a collar. The metal tubing is to make inserting the tube into the gas sample port as easy as possible; the collar is to seal the port opening against the tube to reduce the risk of erroneous readings (often a damp rag is used rather than the collar to seal the tube into the sample port).
Correct insertion of the tube is important to enable a representative sample to be obtained from the cargo hold. Ideally, the gas detector and/or the tube should incorporate an in-line particle and water contamination filter to prevent damage to the sensors.
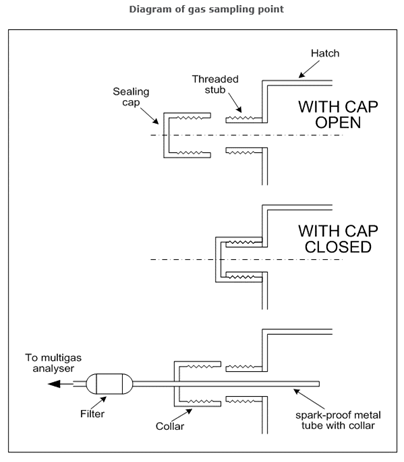
In accordance with the IMSBC Code, the gas detector used when transporting coal must be fitted with at least oxygen (O2), flammable gas (LEL), and carbon monoxide (CO) sensors. Most of the modern handheld devices will also include a hydrogen sulphide (H2S) sensor.
The O2, CO and H2S sensors are “wet” electrochemical cells, which utilise a chemical reaction inside the cell between the target gas and chemicals (reagents) contained in the cell. Electronics in the cell detect changes in the chemistry as the reaction of the wet reagents with the target chemical occurs; that signal is then translated into a digital display, typically displayed in parts per million (ppm) or percentage volume (%.vol) on the screen.
Chemical sensors that are marketed as being for a particular gas, are often not actually target-gas specific and can react to the presence of other gasses or vapours and as a result display a false reading. Therefore, it is important for a user to be aware of the possible cross sensitivities of their detector’s sensors to avoid relying on such false readings. This information should be detailed in the instruction manual provided with the gas detector.
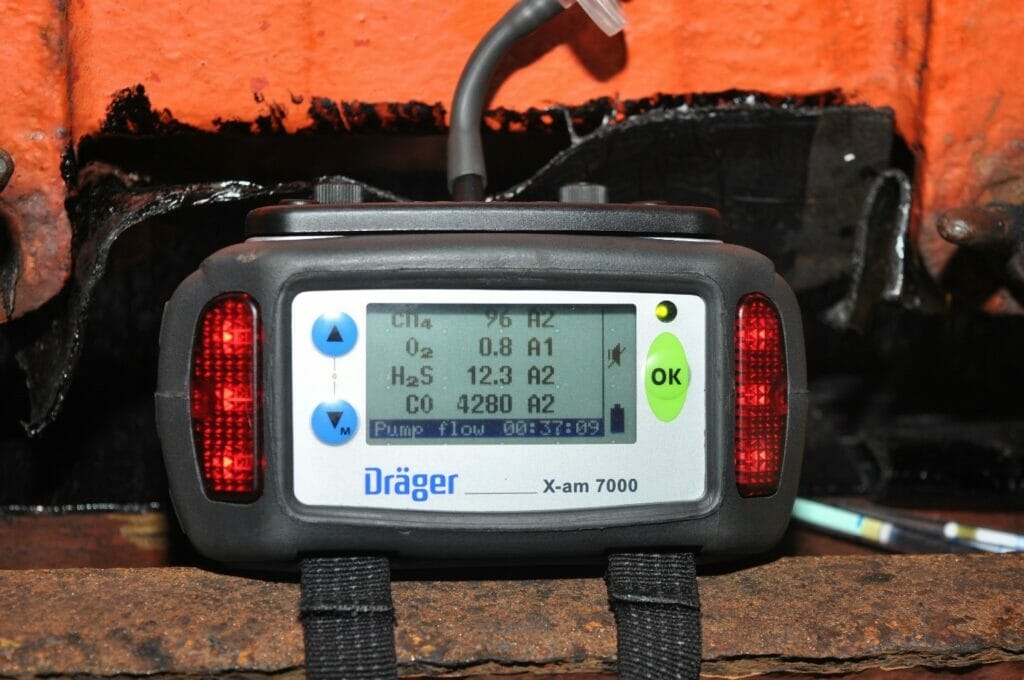
Chemical sensors are prone to damage caused by both poisoning and saturation. Poisoning occurs when a non-target gas or vapour attacks the wet chemicals inside the sensor cell and alters the cell chemistry. Once poisoned, the effected sensors will often need to be replaced.
Each sensor will have a specified ‘range of detection.’ This indicates the lower limit of detection of the target gas and also the maximum concentration of the target gas the sensor should be exposed to. Over-exposure can cause sensor cells to become saturated. A saturated cell might ‘clear’ in fresh air, or after re-calibration, but that is not always the case, as over-saturation can damage a cell to the extent that it would need to be replaced.
LEL sensors used to detect hydrocarbon gasses can use two different types of sensor technology, the most common and cheapest is the catalytic type, which uses a pellistor in an electrical measurement circuit known as a Wheatstone Bridge.
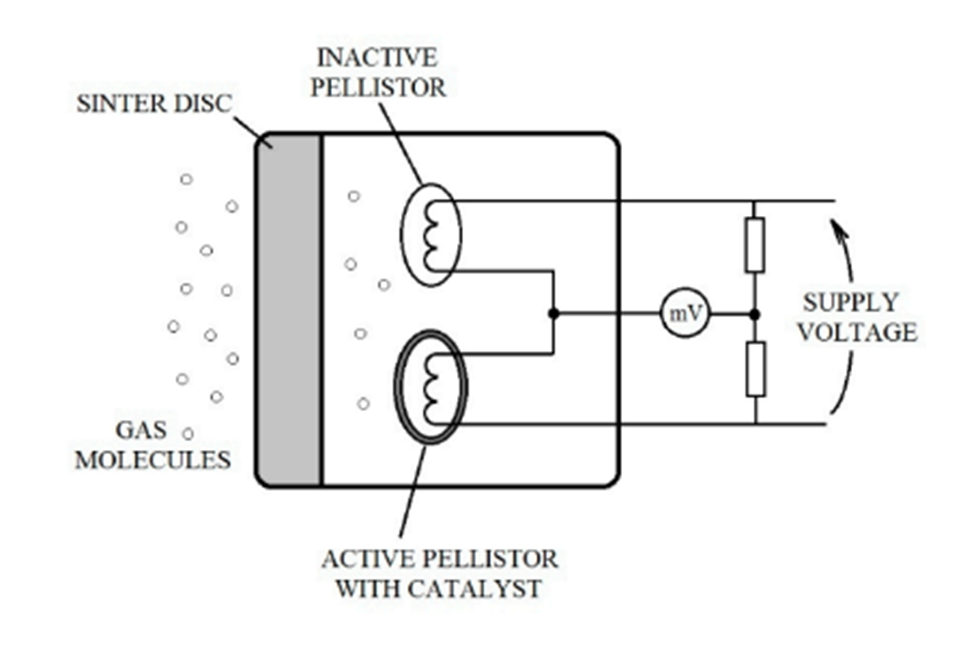
The working elements of a pellistor comprise two ceramic beads, both of which encase platinum wire coils. The sensor heats both platinum coils to a known temperature and then constantly measures the resistance of the coils. One of the beads (the ‘active’ bead) is treated with a catalyst, which lowers the temperature at which the hydrocarbon gas close to the surface of the bead reacts. The additional heating of the active bead due to the reaction of the hydrocarbon gasses is detected by the electronic measuring circuit as a change in the resistance of that platinum wire coil relative to that encased in an inactive bead of plain ceramic. The change in resistance is translated to a read out on the display, normally in % LEL (Lower Explosive Limit of methane). Pellistor sensors have been used widely and safely for many years, they are intrinsically safe so can be used in a flammable atmosphere, and they can also detect hydrogen. However, there are several limitations to be aware of, which are outlined below:
- A pellistor LEL sensor will only operate correctly and produce reliable results if there is sufficient oxygen present (>10%).In a depleted oxygen environment, LEL readings will become inaccurate.
- Pellistor LEL sensors are not able to discriminate between combustible gases and will only provide an indication of the presence of a flammable gas (or vapours), be it hydrogen, carbon monoxide, methane, ethane, gasoline or diesel fumes etc. They have different sensitivities for each flammable gas, and as such, even if the detector indicates a flammable atmosphere is present, it might not always necessarily be the case.
- LEL sensors are usually calibrated using methane, and if another flammable gas is present, then the reading given by the instrument will often be incorrect (either erroneously high or low). This is why it is important to know what gases are being evolved by a cargo.
- Pellistors are prone to damage from poisoning from compounds containing silicone, lead, sulphur and phosphates which could be found in some unexpected places on a ship. For example, cleaning products such as furniture polish will often contain silicones. Therefore, users should exercise caution when dealing with these compounds, and perform regular checks to see whether the sensors have become unreliable.
- A pellistor can also be damaged by saturation, i.e. exposure to high concentrations of hydrocarbons.
Therefore, when using a pellistor LEL sensor, the gas detector will need to be calibrated regularly so that any damaged sensors can be replaced.
An alternative LEL sensor technology utilises the infra-red (IR) absorption properties of hydrocarbons.
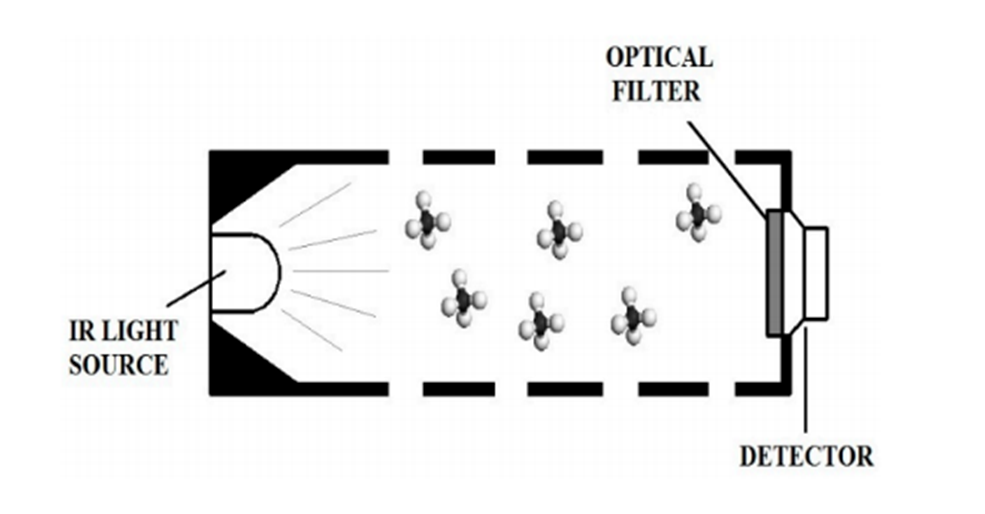
These sensors are typically more expensive than pellistor sensors, but they are not prone to either poisoning or saturation. The IR LEL sensors will operate reliably in a depleted oxygen environment, as they are not reliant on heat from a combustion reaction as the detection method, but they will not detect hydrogen or acetylene as these gases do not absorb IR at the frequency used by the sensors.
GOOD GAS MONITORING TECHNIQUE
- If safe to do so, ensure the cargo hold to be monitored is not ventilated for 4 hours prior to sampling.
- Ensure that the sampling tube is clean and free from condensation, that the metal portion of the tube is spark proof, and that it is detached from the gas detector. Check the inline filter (if fitted) is clean and dry.
- Switch on the gas detector in clean air (e.g. in the ship’s office) and let the unit run for about 5 minutes before going outside to take measurements.
- Ensure that your gas detector has been calibrated recently (i.e. it is “in date”) and that all of the sensors pass the unit’s self-test function, which runs when the unit is switched on.
- Open the cargo hold sampling port on the leeward side. Insert the spark proof metal tube so that the tube is inside the cargo hold and seal the sample port with the tube collar or a damp rag.
- Re-attach the sampling tube to the gas detector and draw a sample of the cargo hold atmosphere through the tube, using the aspirator, until steady readings are obtained. This could take several minutes.
- Log the results on a suitable form and records cargo space, date and time for each measurement.
- Detach the sampling tube from the gas detector, remove the tube from the sample port and let any condensation drain out by holding the tube vertically (i.e. uncoiled).
- Put the sealing cap back on the sampling port.
- Repeat steps 5 to 9 for each hold to be monitored.
CARING FOR YOUR GAS DETECTOR
A gas detector is an expensive scientific instrument. Please read the manufacturer’s instructions regarding its use, and care.
In general, the gas detector should be kept clean and treated with care. Clean the outer casing with a damp cloth. NEVER use any cleaning chemicals, detergents or solvents to clean it as they can adversely affect / poison the sensors. Detach the sampling tube when not in use and hang it vertically to let any condensation drain out. Keep the gas detector charged. Store it in a secure location where it will not be tampered with or exposed to chemicals or fumes. If your gas detector allows, you have the equipment, and your situation allows (i.e. you don’t have to travel with the kit by air), carry out a “bump test” calibration in accordance with the manufacturer’s instructions at regular intervals.
A bump test, or function check, with a proprietary mixed gas-test cylinder is the only way to ensure the gas detector is working properly. It is performed by exposing the sensors in the detector to a gas mixture that contains gases at concentrations that exceed the lower alarm set points of the detector. Ultimately, it is used to confirm that the sensors respond to the target gas; it also verifies that the display reacts and the audible alarm sounds. Bump tests are qualitative in nature; they do not provide information on the accuracy of the device’s measurements, and therefore they do not act as a method for calibrating the gas detector.
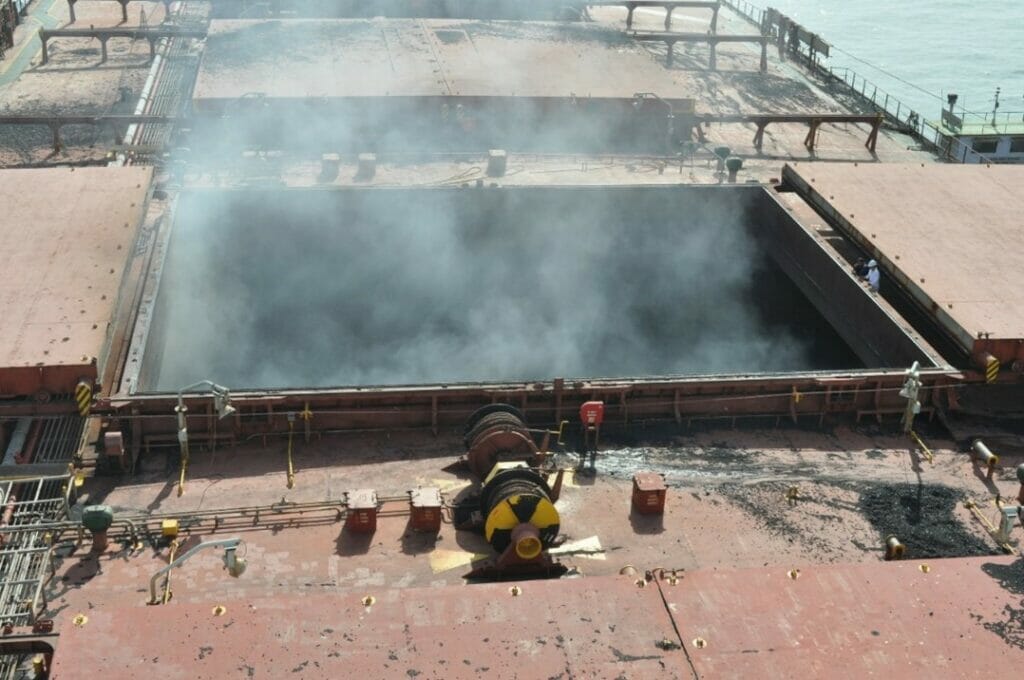
VENTILATION OF A COAL CARGO
Common problems associated with the transportation of coal in bulk include self-heating and generation of flammable gas (i.e. methane).
SELF-HEATING:
Self-heating normally occurs in localised hot-spots within a bulk cargo, so temperature measurements of the atmosphere above the cargo (i.e. taken through the gas sampling ports) are unlikely to identify problems. However, when coal self-heats it produces carbon monoxide (CO), so measuring the concentration of CO in the cargo hold is the most effective method of identifying a self-heating cargo. The atmosphere in each cargo hold should be monitored, at least daily, not only for carbon monoxide (CO), but also hydrogen sulphide (H2S), oxygen (O2) and flammable gas (LEL – methane). If the holds are being ventilated, then if safe to do so, ventilation should be stopped at least 4 hours prior to gas measurements being taken.
WHEN TO VENTILATE:
The International Maritime Solid Bulk Cargoes (IMSBC) Code requires that the holds are ventilated for 24-hours after loading. However, unless expressly instructed to the contrary, coal cargoes should not be ventilated following this 24-hours period, as unnecessary ventilation can cause the coal to begin to self-heat. Once a self-heating reaction has started, further ventilation will provide oxygen, which will worsen the self-heating and could lead to ignition of the cargo.
Only if the LEL levels begin to rise, should ventilation be considered, and only for the minimum period necessary to remove any accumulated methane. As detailed in the IMSBC Code, if LEL levels reach 20% or more, then the ventilation should be maintained continuously (except, where safe to do so, for the purpose of gas monitoring).If the LEL level continues to rise after ventilation has been carried out continuously for a period of 24 hours, or if CO levels begin to rise, then expert advice , such as can be provided by Hawkins, should be sought as a matter of urgency.
IF THERE IS A FIRE OR HIGH LEVELS OF CO, THE VESSEL SHOULD:
- Close hatches and cease all ventilation to the holds. Seal the holds by closing the ventilation covers and using RAM-NEK tape (or similar bitumen-mastic tape) around the hatch openings and ventilation covers to provide an airtight seal.
- Ensure all spaces adjacent to the holds are gas checked prior to entry and that no-one enters confined spaces without confirming that it is safe to do so by testing the atmosphere inside.
- Consider boundary cooling of the affected holds and locate the nearest ports of refuge
- Notify Owners and the P&I Club without delay
- Provide Owners and the P&I Club with all temperature and gas monitoring records for the voyage
The IMSBC Code provides mandatory requirements for the loading and carriage of coal. Of particular note are the following:
- The cargo declaration should state whether the cargo has a history of self-heating and whether it has a tendency to emit methane (self-heating is almost always encountered when Indonesian coals are carried).
- Coal should not be loaded if its temperature exceeds 55°C; this is especially important for self-heating coal as a temperature above 55˚°C is indicative that the coal is already at an advanced stage of self-heating. Although not required by the IMSBC Code, an infrared thermometer can greatly assist the crew in checking the surface temperature of the cargo prior to and during loading.
Despite the risks associated with the transportation of coal cargoes, the majority of vessels carry coal without incident. Adhering to the requirements and recommendations in the IMSBC Code greatly reduces the risk of fire. Hawkins has many years of experience in assisting Owners and P&I Clubs to prevent an incident from becoming a major casualty. If the Master only allows cargo below 55˚°C to be loaded, and regularly checks it during passage, then problems can be identified at an early stage and prevented from escalating to the point where the ship and her crew are potentially in danger.
ABOUT THE AUTHOR
Paul Willis has a degree in Chemistry. He joined Hawkins in 2012 as a fire and explosion investigator and investigates a broad range of incidents in the UK and internationally. Paul is a member of Hawkins specialist International and Shipping Incidents team and has travelled worldwide to investigate ship fires involving bulk cargos, containerised cargo, and engine room machinery and equipment. Paul also regularly provides remote assistance with live incidents involving bulk cargos, containerised cargos and hazardous materials.