What is a Cobot?
The 1980’s saw the rapid deployment of industrial robots for mass-production in a drive to reduce costs and improve quality. Industrial robots were typically seen in production lines, sparsely populated with technicians; or robots in cages, both designed to prevent a collision between humans and machines. Whilst the argument for utilising robots in terms of ‘a labourer that never sleeps’ and ‘improvement in quality through consistent output’ is well established, they also lack the dexterity and adaptability of a human worker. The last decade has seen a surge in demand for cobots (collaborative robots), that is, robots that have been designed to work alongside human workers, to combine the skillset of robots and humans whilst maintaining the safety of the human worker.
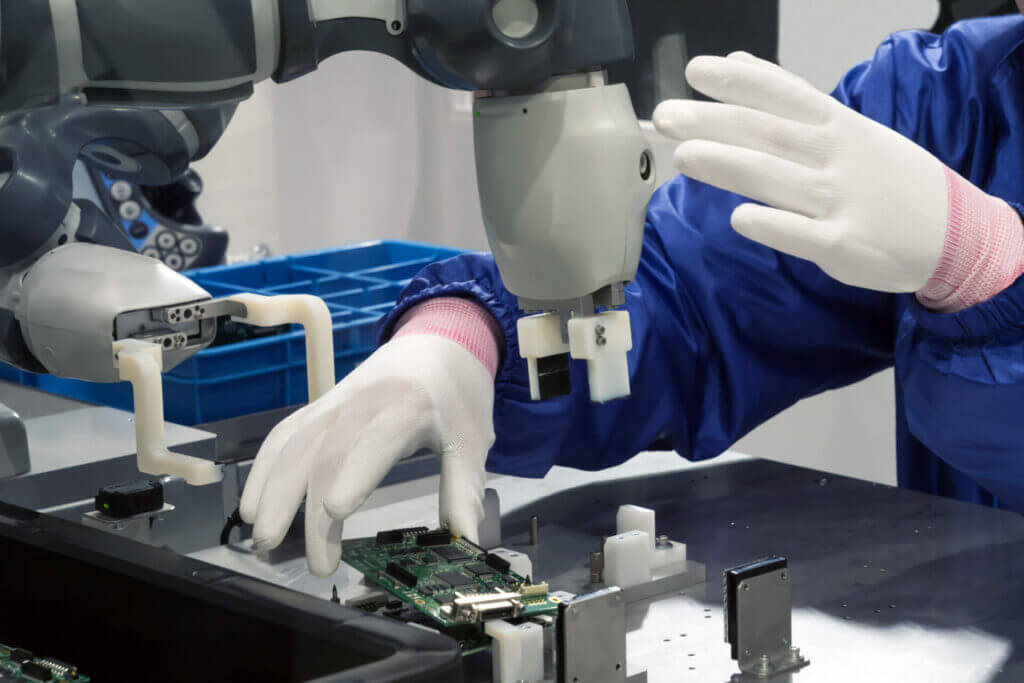
In 2023, the estimated annual sales of cobots globally was in the order of USD 1 bn, and some market research companies predict a rapid growth of up to USD 11.4 bn by 2030. A multi-billion dollar market, growing at between 15% to 32% annually led Allianz Global & Corporate Speciality insurers to identify the growth of cobots as an important trend in their industry in the next 15 years (reported in Sept 2019).
Cobot Variations and How They Work
There are significant differences in cobots, compared to the familiar industrial robots, which are intended to mitigate the risk to human safety during close interaction.
In the late 2000’s, Kuka Robotics and Universal Robots, world leaders in the design and manufacture of industrial robots, released the first generally available production cobot models. Kuka Robotics released the LBR 3 and shortly afterwards Universal Robotics released the UR5, both of which were cobot versions of the familiar articulated arm robot (arm sections referred to as links, joined together with rotational elbow or wrist type joints). Unlike their robot predecessors, which relied on external sensors such as light curtains and proximity switches to activate safety protocols (e.g., to stop or slow down), cobots rely on physical differences and internal sensors for safety. The articulated-arm cobots are typically lightweight in comparison to robots and are limited to small payloads (typically 3 kg in early models) in order to reduce their inertia and the energy transfer to the co-worker when a collision occurs. They commonly employ sensitive torque sensors at each joint to detect a collision with a co-worker, enabling them to respond rapidly according to their control system.
The YuMi dual arm cobot, manufactured by ABB, was released in 2015 and is probably the highest profile cobot, as far as public awareness is concerned, and is considered to be state-of-the-art in the cobot sector. It was designed to work side-by-side or opposite human co-workers on precision tasks such as electronic component assemblies. YuMi incorporates many of the safety control systems employed by the earlier articulated arm models, with the addition of cameras that view the workspace – also used to adapt to changing situations such as picking up misaligned parts. YuMi has also adopted padding on its arms and has removed all pinch-points so that its co-worker’s fingers cannot become trapped.
We can assume then, that collisions are expected to happen, and so systems must be in place to minimise the severity of the injury to the human co-worker.
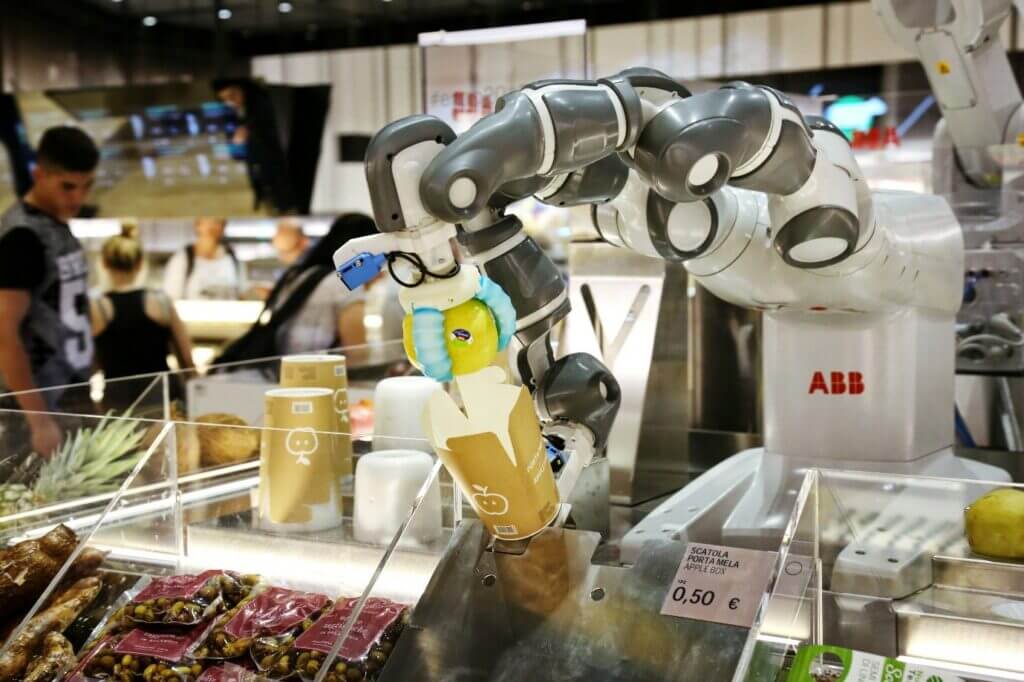
Safety Systems and Industrial Standards
There are numerous ways in which workers interact with cobots. Some cobots operate independently, but in close proximity to workers; others are guided by hand to provide the operator with increased strength and stability. The safety systems employed are required to be designed to reflect the cobot’s intended use. ISO 10218-1:2011 provides a specification and guidelines for the safe design of robots (including cobots), and describes basic hazards associated with them. ISO/TS 15066 is a technical specification, and a supplement to ISO 10218, which provides guidance on risk assessment of robots in collaborative applications i.e., cobots.
From a forensic investigation perspective, when investigating a human-cobot collision, one consideration is likely to be the system response. When a cobot’s internal sensor detects a collision, the system should produce a response based on a stopping category. IEC 60204-1 (and EN 60204-1) describes three stopping categories: 0, 1 and 2 for electrical machines. Universal Robotics defines most of its cobot collision safety systems (referred to as safeguarding) as stopping category 2 (stopping with power left available to the robot i.e., slows quickly to a standstill, but remains powered) and also specifies the maximum stopping time for different responses, which can be referred to by the investigator.
Summary: What Does This Mean for Insurers and Investigators?
The rapid growth of industrial, human-robot, collaboration tasks has the potential to lead to an increasing number of personal injury cases relating to human-robot collisions Large variations in cobot solutions means that determining whether a failure is a result of a manufacturing or software design defect, or other cause, will be a challenge for both the insurer and investigator. Awareness of the developments in this sector, in particular, how the system was designed to respond to a collision between cobot and human co-worker, may be key.
About the Author
Dr Ian Jeavons is a mechanical engineer with over a decade of experience in a range of manufacturing environments. His involvement with industrial robots and cobots stems from his doctorate research whereby he used machine learning and laser tracker measurements to improve the accuracy of an industrial robot for machining purposes.