Fracture can lead to the failure of almost any object, product or component that is subjected to some sort of mechanical loading. Sometimes the fracture is mildly irritating, leading to cosmetic impairment or slight loss of functionality. However, fracture can also lead to catastrophic failure, which can cause inconvenience, expense, or in the worst case, loss of life.
Fractures can occur slowly (progressively) or instantaneously; the former often occurs by way of fatigue (slow crack growth). Instantaneous fracture usually occurs at the time the load is applied, but can also occur (under special circumstances) at some time after the load was applied. In most cases, as far as the user or observer is concerned the fracture is sudden and unexpected.
Fatigue
Fatigue is a well-used term, and its origins suggest something that is worn out, but in the case of failures in materials, the term relates to gradual growth of cracks in response to a repeated (cyclic) load; often the loads in question are fairly modest.
This sort of fracture takes place in stages; first we have ‘initiation’, during which there are no outward signs of a problem and certainly no visible cracks. However, on a microscopic scale, damage is accumulating within the component, which will ultimately lead to the crack at the end of the initiation stage. The initiation stage can make up a large part of the life of the component.
The second stage is crack growth, in response to a continuation of the cyclic loading. The crack will grow a little further every time the load cycle is applied. This leads to a very characteristic appearance of the fracture, which helps to diagnose the cause, after the event. An example of such marks on a steel bolt is shown below.
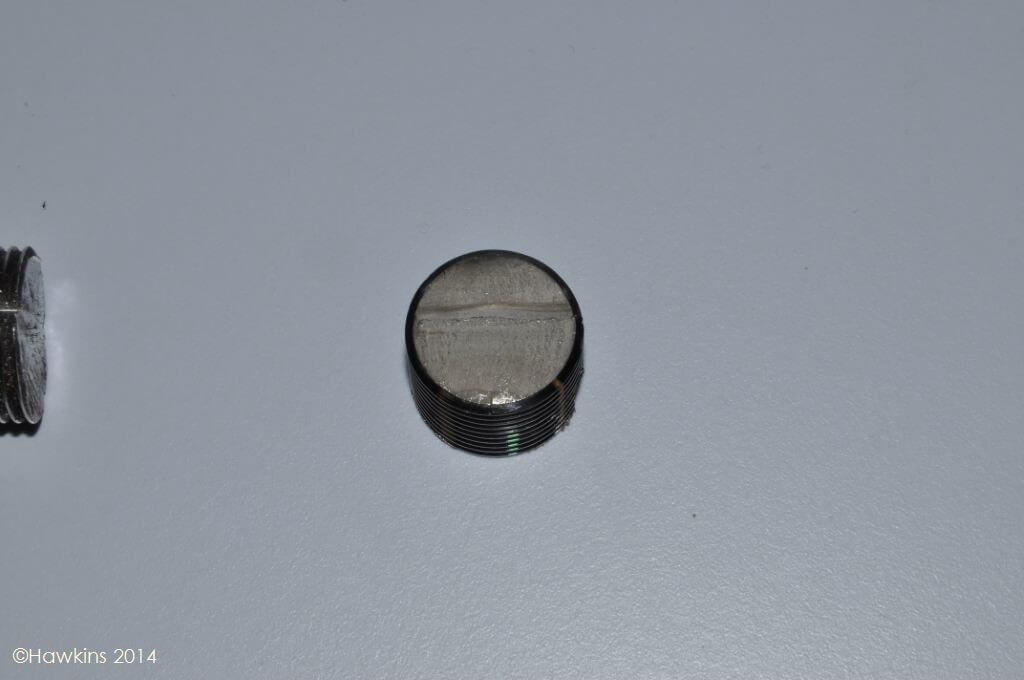
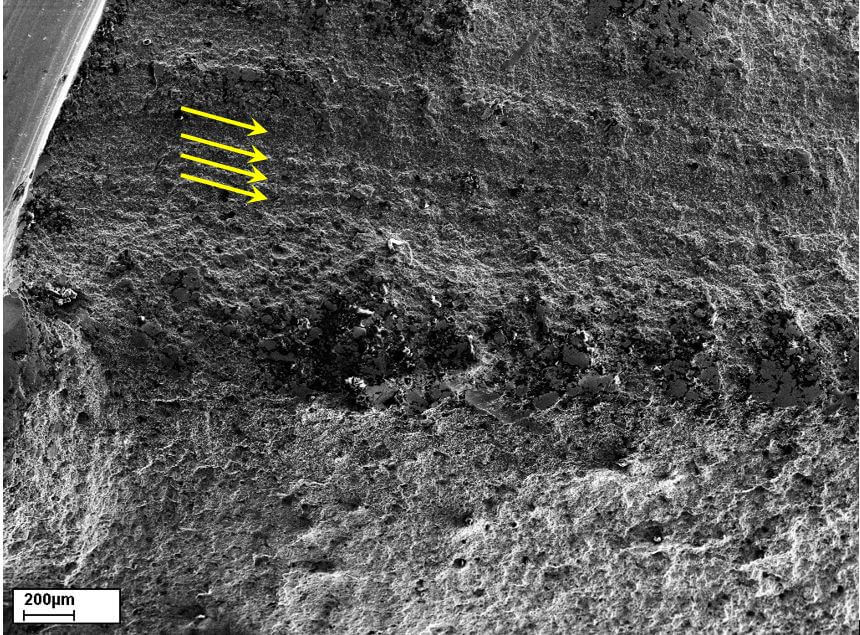
While the crack is growing in service, it may become visible. In some cases, it is necessary to use special fluorescent dye to soak into the crack and make it more noticeable. This is known as a dye penetrant inspection.
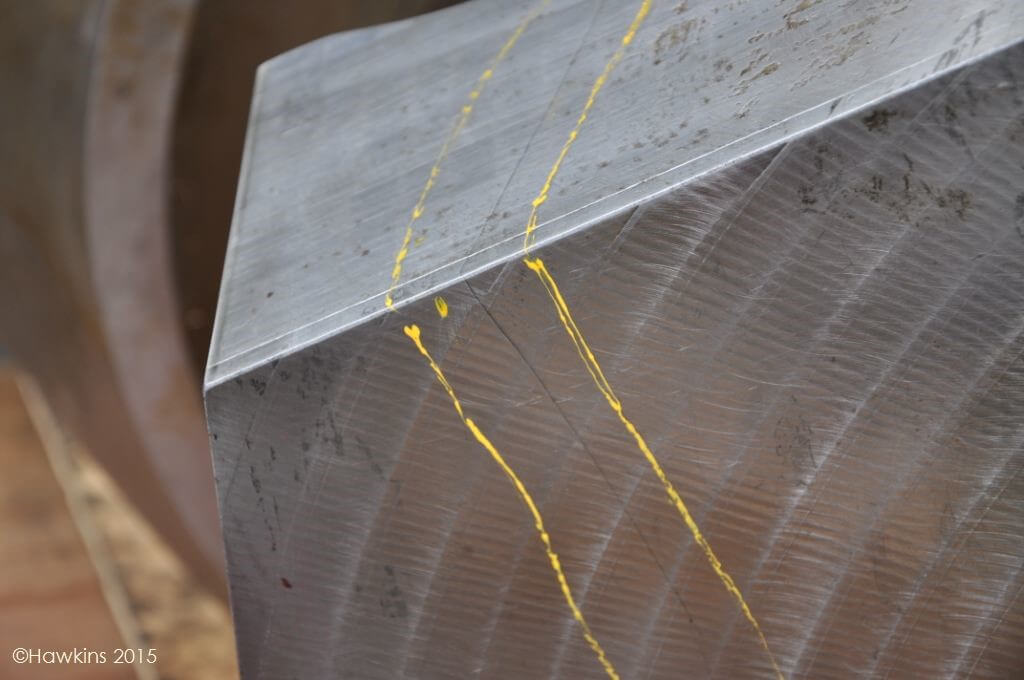
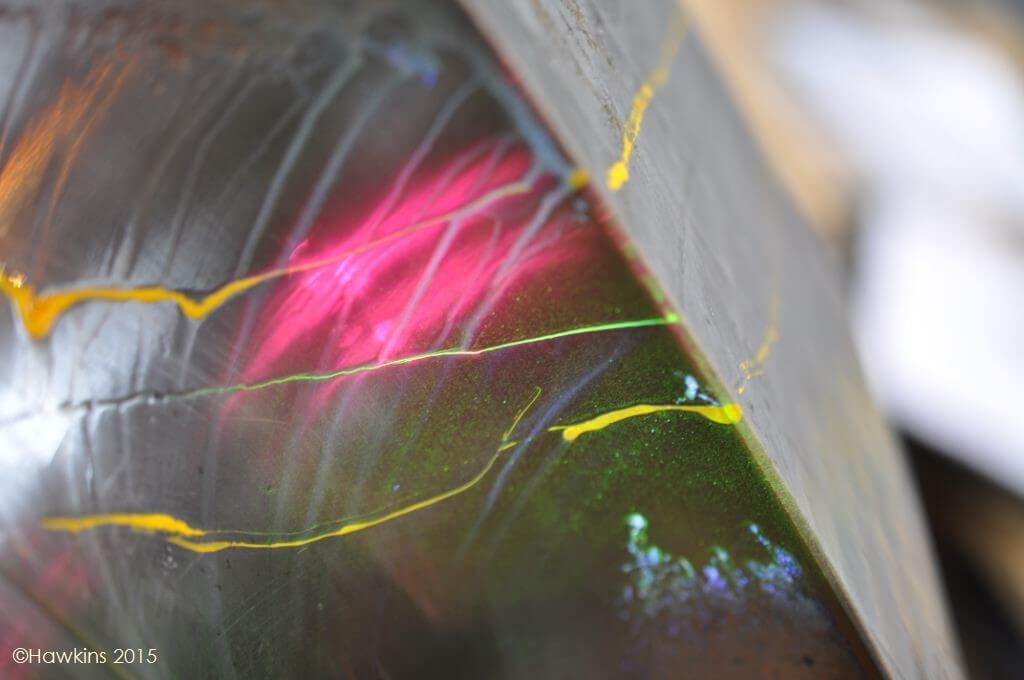
As the crack grows, the remaining component thickness reduces and consequently, causes the effective stresses to increase, even under the same load. Eventually the remaining (uncracked) component cannot withstand a single further load cycle. At this point the crack grows to completion, usually with catastrophic results.
The damage typically initiates at a stress concentration; a part of the component where the stresses are highest. Stress concentrations can result from the overall shape of an object; for instance a change from a thick section to a thin section or a bend. In more detail, fatigue cracks usually initiate at an imperfection like a rough feature on a surface or a material defect. In the examples above, the fatigue initiated at machined features (threads and holes) in components with high cyclic loads. Those features are deliberate (i.e. not ‘defects’), but the components were subjected to excessive cyclic loads.
Sources of Defects
One of the most famous examples of a catastrophic fatigue fracture is the Comet aircraft, three of which disintegrated in the air, leading to total loss of life. In that instance, the fatigue was caused by a poor understanding of the stress in the aircraft that originated from the pressurisation of the fuselage, and deficiencies in both design and manufacturing.
The Cohen Committee was established to examine the causes of the Comet crashes. The subsequent inquiry report includes the following images which depict testing being carried out on a Comet G-ALYU and a failed fuselage. The report highlighted that the fuselage frames did not have sufficient strength to prevent the crack from propagating, after initiating at bolt and rivet holes.
[1] Cohen Inquiry Report figures 6 and 7 showing a Comet G-ALYU in the water tank for pressure tests. The fuselage had ripped open at a bolt hole, forward of the forward left escape hatch cut out.
Many common defects that originate in the manufacturing process can initiate fatigue fractures. Cast metal components can contain voids (individual, sometimes large holes) or porosity (spongy groups of smaller holes) that occur as the liquid metal solidifies in its mould. Porosity acts as a stress concentration (and represents an absence of load-bearing material) and can be difficult to avoid. It is usually accommodated by making the component thicker. Some critical components are checked using non-destructive testing (NDT) techniques such as X-Ray or ultrasonic testing to look for defects early in the manufacturing process.
Unexpected (either too large or in the wrong place) porosity is a good candidate for initiating fatigue cracks in objects like engine components. In special cases such as aircraft engines, porosity can be minimised by enveloping the component in hot, high-pressure gas (‘hot isostatic pressing’) which effectively squashes the voids closed, thus removing the stress concentration.
Conclusion
In practice, defects are unavoidable in mass-produced products. Defects can exist without problems if the manufacturer understands the sort of defects that could occur, and accounts for those defects in the design. Measures such as NDT can be used to check components for serious defects.
However, mistakes are made, and defects can slip through even the tightest of controls; hence the occasional unexpected fracture will be a fact of life for the foreseeable future.
About the Author
Dr Nick Wright is a materials scientist with a background in Formula 1 engine development and power generation consultancy. He has investigated a large number of international claims relating to failures in industrial gas and steam turbines from all of the major manufacturers. Cases investigated include turbine blade and vane failures, compressor blade and vane failures, combustion hardware failures, efficiency/performance degradation, premature component degradation, shaft failures, gearbox and bearing failures. He has also investigated failures involving large reciprocating diesel engines and pumps and is available to attend site worldwide at short notice.
[1] https://reports.aviation-safety.net/1954/19540408-2_COMT_G-ALYY.pdf