Flexible braided stainless steel hoses (flexihoses) are generally used for the connection of taps and WC cisterns to the incoming water supply. The flexible nature of the hoses means that they provide an easily made connection, making them popular with the DIY market. They have been produced for plumbing since the early 1990s, after the technology was established in the aerospace and automotive sectors. However, the insurer AIG reported that in 2016 flexihoses caused around 20% of water damage claims in Australia.
Flexihoses are generally found either under the kitchen sink, under the bathroom washbasin or connecting the toilet cistern to the water supply. Because they are popular for use as tap connectors, they often carry hot or cold water at mains pressure. This means that if the hose fails, a large amount of water can escape very quickly, due to the driving force of mains pressure pushing more water into the pipe.
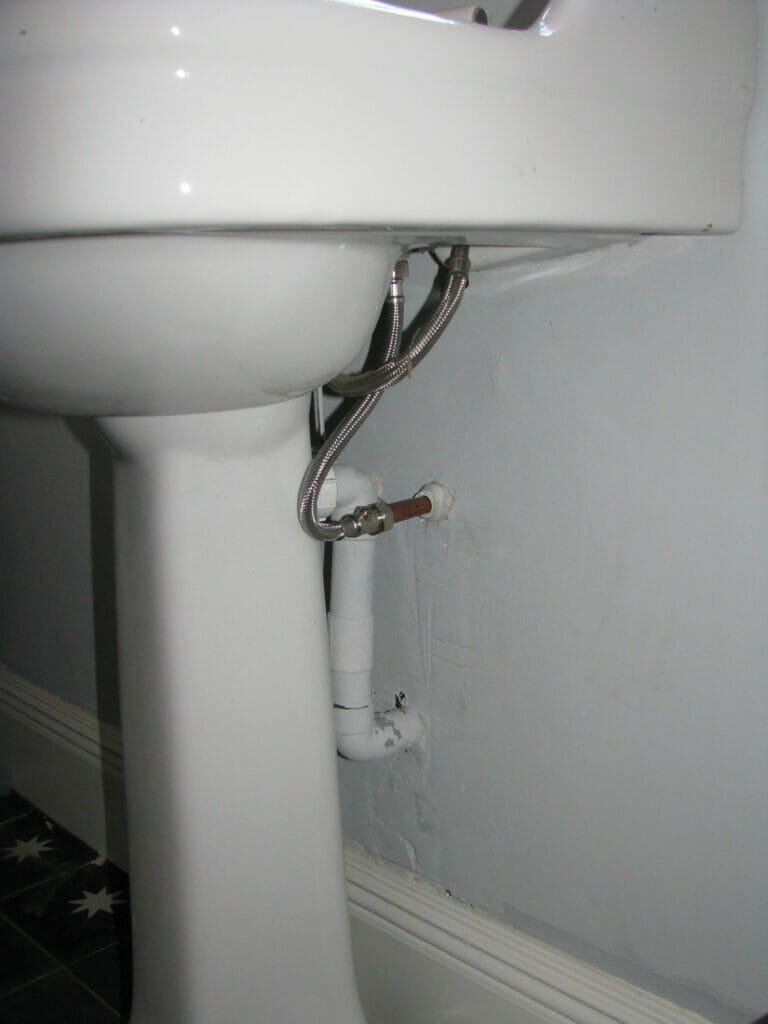
The hoses consist of: an inner rubber hose, which carries the water; an outer stainless steel braid, which supports the inner tube; and end fittings that provide easy connection to existing pipework and fittings. The inner rubber hose alone is not designed to be capable of withstanding the pressure exerted by the water within it. Instead, the outer braided sheath provides support for the rubber hose whilst enabling the assembly to remain flexible.
Flexible hose failures mainly occur as a result of corrosion of the stainless steel braid wires. If a sufficiently large break of the braided sheath occurs, the rubber hose within is no longer supported, and the water pressure causes it to bulge out through the gap. As the rubber is stretched thinner in the region of the bulge, a rupture of the hose occurs, allowing water to escape.
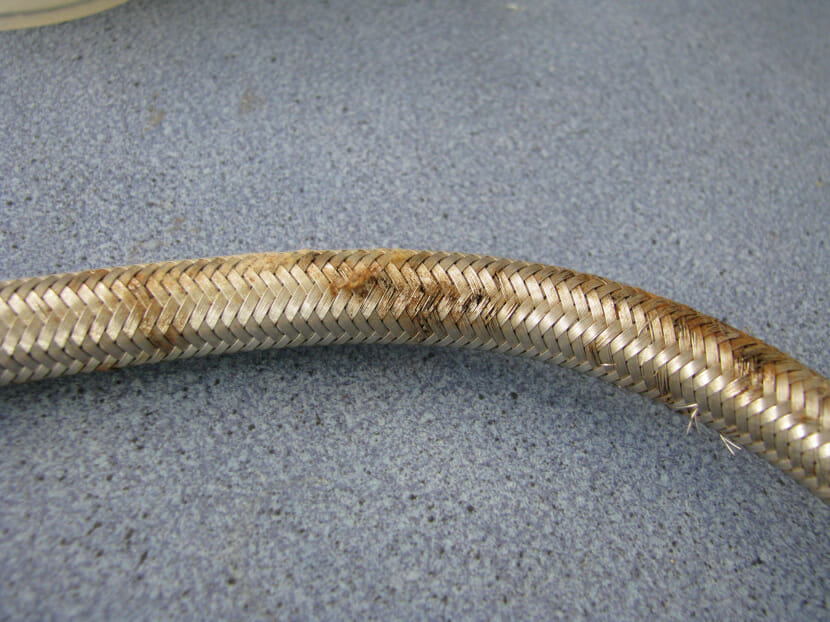
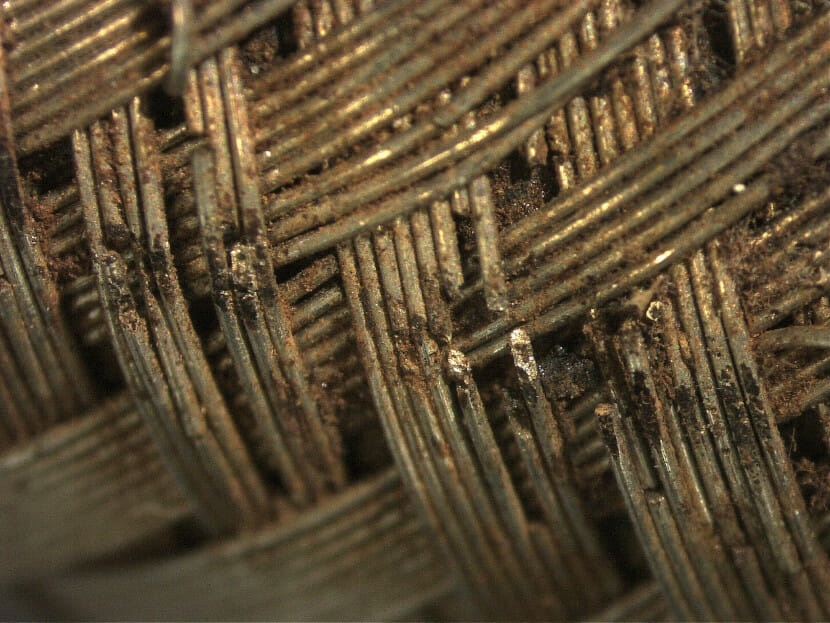
Corrosion of a Flexihose’s stainless steel, magnified on the right
Although stainless steel is more corrosion resistant than plain carbon steel, it is still vulnerable to corrosion in the presence of certain chemical elements, such as chlorine. Chlorine is commonly found in household cleaning products, such as multi-surface sprays, toilet cleaners and bleach. Flexihoses can often be exposed to these products during cleaning, particularly if the product is not rinsed off. In addition, if the flexihose is located in a cupboard under a sink, where cleaning products are stored, leaving the cap off a product can also produce a high concentration of chlorine in the enclosed cupboard space, which can then settle on the wires of the hose’s braid. Another source of chlorine is the water itself, which is often disinfected using chlorine by the water supplier. If the hose becomes wet, the water evaporates away leaving a higher concentration of chlorine trapped amongst the braid.
Stainless steels are also susceptible to a corrosion mechanism known as crevice corrosion. When the design of a component leaves a fold or a crevice at the surface, liquid is drawn down into it by capillary action. Because liquid cannot circulate out of the crevice easily, conditions at the bottom of the crevice become more and more corrosive, leading to a localised attack of the material. In the case of a flexihose, the gaps between the overlaid stainless steel braid wires can act as crevices, increasing the susceptibility of the material to any corrosive substances that are present.
Between 2010 and 2015, the majority of the flexihose failures that Hawkins investigated occurred within 5 years of their installation. Chemical analysis of the stainless steel braids revealed that the failed hoses were manufactured from cheaper grades of stainless steel. These grades contained less chromium and nickel than the more widely used 18/8 grades. Chromium and nickel are added to the stainless steel to provide corrosion resistance, therefore a reduction in these elements increases the likelihood of corrosion occurring.
Since 2015, Hawkins have also seen an increase in the number of failures of hoses with braids manufactured from 18/8 stainless steels, such as AISI 304. It appears that the vulnerability to corrosion is not limited to the low cost grades, and may be an inherent risk of the hose’s design.
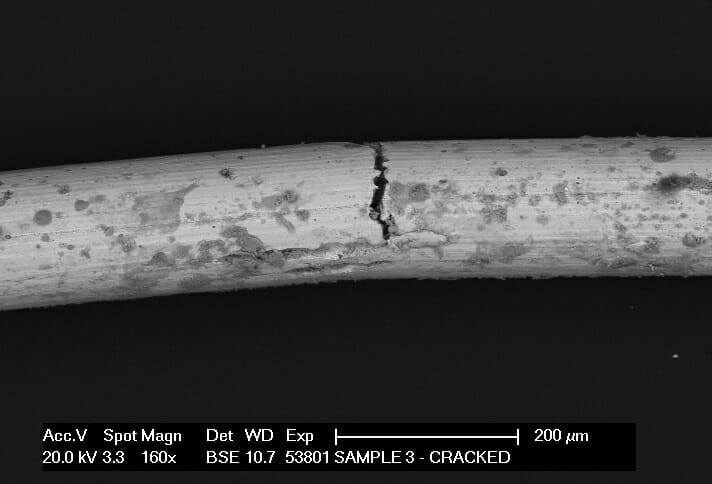
The first sign of corrosion damage is the fracture of individual braid wires. This breakage can occur without any visible signs of corrosion or rusting. If you find a flexihose with either broken braid wires or areas of rust, it would be prudent to consider replacing it, to prevent any potential escapes of water in the future.
If you would like to instruct a Hawkins engineer to determine the cause of a either hose’s failure, or of an escape of water as a whole, please contact us.