Steel is one of the most commonly used construction materials, due to its wide availability and good strength-to-weight ratio, both in tension and compression. The development and mass production of modern steel began during the time of the Industrial Revolution in the 18th century. Steel’s flexibility and versatility allows it to be used in many challenging structures that would be either difficult or impossible to achieve with other common construction materials, such as concrete.
Steel is an alloy composed of iron with a small percentage of carbon. Other elements may be added to improve its strength and fracture resistance. Steel is normally a ductile material, meaning it can sustain significant deformation before failure. The yield strength is perhaps the most important characteristic of structural steel; it behaves elastically in the linear range when subjected to a load below its yield strength, and also recovers fully on unloading. When subjected to a load beyond its yield strength, however, it undergoes plastic deformation, which is irreversible and permanent.
The yield strength varies significantly with the chemical constituents of the steel, the most important being carbon and manganese, both of which increase the yield strength. The yield strength also varies with the heat treatment used, as well as with the amount of working that occurs during the rolling process. Thus, sections of steel which are more worked have higher yield strength.
Structural steel is available in many grades with yield strengths varying from 175 MPa to 670 MPa (1 MPa is short for 1 megapascal, equivalent to the pressure exerted by 100 tonnes on a square meter), with all having a Young’s modulus[1] of about 205 GPa. A full explanation of these grades and their relevant mechanical properties can be found in the European structural steel standard EN10025:2004.
In general, steel structures require greater attention during both the design and construction stages, when compared to monolithic construction. There are six basic mechanisms of failure for steel structures: ductile yielding, brittle fracture, buckling, fatigue, stress corrosion cracking, and creep.
YIELDING
Yielding is a ductile failure mode in which the elastic limit is exceeded, and the components undergo plastic (i.e. permanent) deformation, before reaching the steel’s ultimate tensile strength. This can result in visible deformation as steel is stretched or bent. Large amounts of energy absorption can occur prior to yielding failure. Yielding fracture is often irregular in appearance, with shear lips and localised thinning of the cross-section. The appearance of the adjacent painted surfaces or mill scale may also indicate yielding failure. Due to its brittle nature, paint or mill scale cracks can occur in bands perpendicular to the direction of the local principal stress if a steel structure experiences inelastic deformation.
Conventional code-based design methods can be used to prevent the yielding failure with complete certainty. Therefore, yielding failure is the least common failure mechanism in steel structures, unless the design is either inadequate or the design is not followed. Hence, excessive deformation associated with yielding failure is usually the result of the failure rather than the cause.
BRITTLE FRACTURE
Brittle fracture can occur at stress levels below the yield strength, or even below design allowable stress levels. In most cases, it occurs with little or no deformation and, therefore, with little or no warning. Brittle fractures can result in significant structural damage, catastrophic failure, and serious injury. Brittle fracture is typically characterised by flat fracture surfaces with no plastic deformation. Additionally, brittle fracture surfaces exhibit features like V-shaped chevron marks, which can be used to determine the direction of fracture propagation and, more importantly, the location of fracture initiation based on their orientation.
Typically, brittle fractures initiate from stress concentrations, such as weld flaws or bolt holes. They can occur when the local constraint is severe, for example at the junction of beam connections where thick plates are intersecting. Thick steel components are generally more prone to brittle fractures than thin steel components, because the way the thick sections are produced leads to both excessive grain size as well as weakness in the centre, where the cooling was slower than at the surface.
Low temperatures and high loading rates are other factors that can cause brittle fracture. This is because they both generally result in smaller inelastic zones and, therefore, more brittle behaviour. The risk of low-temperature brittle fracture can be controlled by the specification of a steel with adequate toughness.
BUCKLING
Buckling, or instability of steel structures, is the failure mode that is dependent primarily on the structure’s geometry. This might happen due to either: a lack of bracing/lateral support, higher-than-expected loading, or other factors that were not considered during the design. It is the only failure mode that is primarily caused by local compressive loading, whereas most other failure modes occur largely under tensile loading.
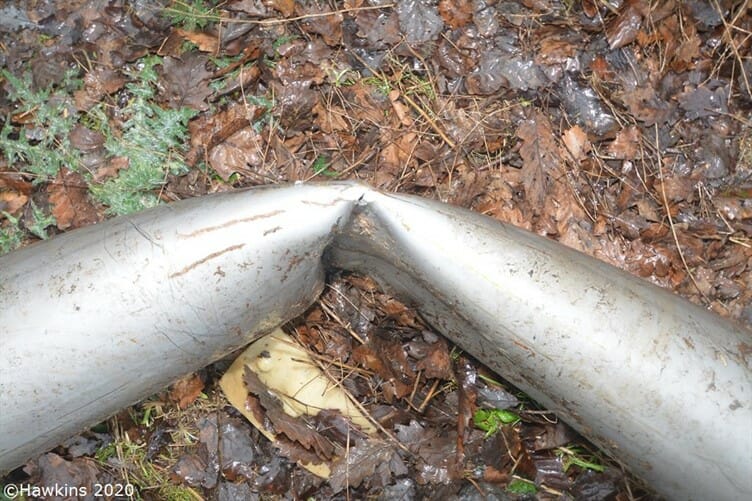
Buckling occurs mostly in long, slender elements, such as long columns or plates with large width-to-thickness ratios. Eccentric loading and accidental impact are two of the common causes of buckling failure. Other than the slenderness and eccentricity, the amount of fabrication-induced residual stresses on the steel is another important factor that influences a member’s buckling strength; the effect of residual stresses creates an uneven stress distribution, thereby causing eccentric loading in the member and eventual instability under external compressive loading.
FATIGUE
Most structures are subjected to repeating loads of varying magnitude, most often below yield strength and design-stress levels. The initiation and propagation of cracks in a material due to cyclic loading is referred to as fatigue. Fatigue can occur in structures such as wind turbine towers or bridges, which are constantly subject to cyclic loads such as wind loads or vehicular loads.
Structural steel may fracture at relatively low tensile stresses after many cycles of load. Cyclic loading generates microscopic plastic damage at regions of local stress concentration (e.g. a fillet weld toe, flame cut penetrations, bolt holes, etc.). If sufficient plastic damage accumulates, then a small crack develops, which then propagates through the structure by the subsequent load cycles. Fatigue crack growth will continue until the effective cross-section is reduced to a level wherein overload failure of the member occurs.
Fatigue failure is typically characterised by flat fracture surfaces and crack growth bands (beach marks) on the fracture surface. In addition, fatigue fractures frequently exhibit markings, referred to as ratchet marks, which can identify the site of crack initiation. In particular, recent studies have revealed that the vast majority of fatigue failures occur at welded connections.
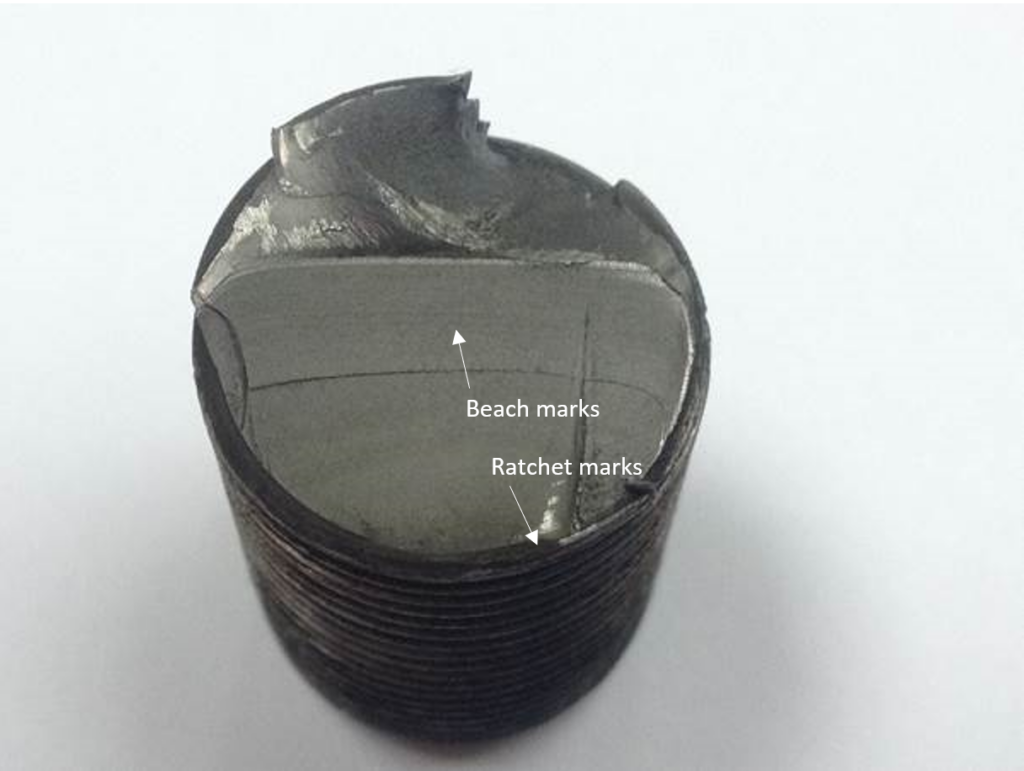
Steel, unlike metals such as aluminium, has a well-defined fatigue threshold for stress. Provided the cyclic stresses remain below that threshold, the structure will have an infinite fatigue life. Hence, fatigue in steel structures can be eliminated by good design and correct fabrication methods.
GENERAL CORROSION
Corrosion damage is perhaps the most prevalent failure mechanism in steel structures. The corrosion of structural steel is an electrochemical process that requires the simultaneous presence of an electrolyte (moisture) and oxygen. In the absence of either, corrosion does not occur. Structures subject to repeated wet-dry cycles are more susceptible to corrosion damage because the electrolyte thickness decreases during the drying process, allowing oxygen to diffuse into the interface of both electrolyte and steel more easily, thus accelerating the corrosion process. General corrosion is characterised by the formation of rust and broad thinning over a significant region of the structure. The main effect of the corrosion is the loss of material from the steel member’s surface, leading to thinner, and so weaker, structural sections.
Corrosion can be prevented by several surface treatment methods, such as paint coatings, hot-dip galvanising and thermally-sprayed metal coatings. Alternatively, good design that prevents the accumulation of water and dust can reduce the likelihood of corrosion damage to the steel structures. However, sections can also be overdesigned (oversized) to allow for some reduction in cross section over the lifetime of the structure.
CREEP
Steel slowly deforms inelastically under load at high temperatures, even if the stress is substantially below the yield strength. This damage accumulation, known as creep, is time-dependent and is a function of temperature and applied load. For structures that are both exposed to a constant load (e.g., processing pipes, boiler tubes, turbine blades), as well as undergo unrestricted deformation, creep results in the continuous accumulation of inelastic deformation and eventual fracture. However, creep is uncommon in ordinary steel structures, unless in the case of long burning fires.
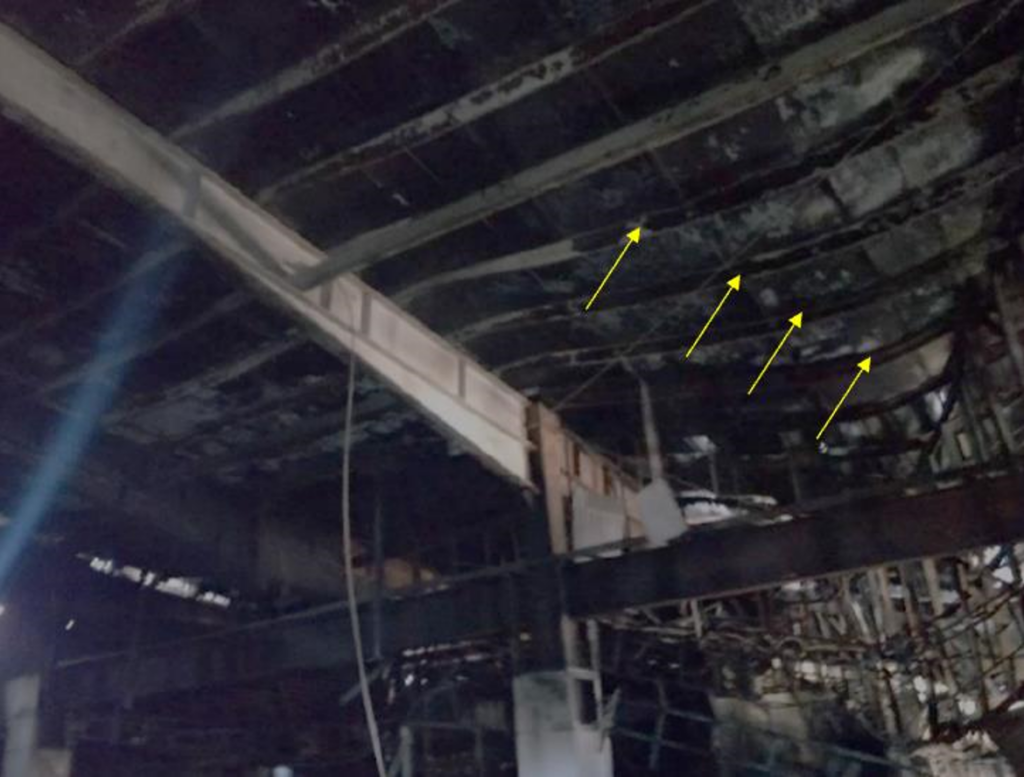
STEEL STRUCTURES FAILURE INVESTIGATIONS
Hawkins has investigated many cases involving failure of steel structures. Our knowledgeable and experienced team of forensic investigators can establish the cause of a failure by:
- Carrying out a detailed desktop or site investigation, including identifying and testing failed elements;
- Reviewing the design, including structural drawings and calculations, schedules of work and specifications;
- Comparing the design to the relevant codes, standards and guidance documents;
- Carrying out failure back-analyses using sophisticated software, supported by hand calculations.
Having established the cause, the investigation will normally reveal the responsible parties, so allowing the repudiation of a claim, a recovery action, a defence against a third-party claim and information to reduce risk of further losses.
If you’re interested in learning more, click here to read Part II: Case Studies.
[1] Young’s modulus is a measure of the stiffness of a material. It is defined as the ratio of stress to strain.
References
Trahair N S, Bradford M A, Nethercot D A, Gardner L (2008) The Behaviour and Design of Steel Structures to EC3, 4th edition
Ratay R T (2010) Forensic Structural Engineering Handbook, 2nd edition
Bull J W (2012) ICE Manual of Structural Design: Buildings
Mann A (2011) Cracks in Steel Structures. Proceedings of the Institution of Civil Engineers, Forensic Engineering 164(1): 15-23
Weck R (1965) Failure of Steel Structures: Causes and Remedies. Proceedings of The Royal Society 285: 3-9