We rely on our infrastructure to provide us with hot water, gas, and oil. Often, we are only aware of how important these services are to us when we notice a problem such as a leak. This can be just as difficult for a homeowner dealing with water streaming through their kitchen ceiling, or a refinery finding steam piping leaks. When the leak involves flammable hydrocarbons, gas or oil the risk of fire and explosion makes the potential for damage and casualties much worse.
At both ends of the spectrum of leaking pipes and cylinders, it is often the joints where the investigator will seek and find the leak location. This does not always mean that the joints themselves are faulty (although this may be the case). In this article, I will reflect on some of the common themes that can lead to leaks and failures; from high integrity industrial sites to the pipework in your home airing cupboard. These fall into three categories: materials and methods, installation skill, and service conditions.
Materials and Methods
The materials that can be welded for high integrity pressure and piping applications range widely across low alloy steels, stainless steels, aluminium alloys, nickel-based alloys, and more. Pipes and fittings used for the UK domestic water supply must comply with the Water Regulations. Either copper or plastic pipe (polybutylene (PB) or polyethylene (PE-X)) are the main options for domestic water pipework, with fittings made from copper, brass, or plastic. However, common to both sectors is that the materials and fittings should conform to British, or equivalent, standards.
The materials properties and composition range for engineering materials are specified to a standard, for instance, British Standard BS EN 10025[1] for structural steel, or American Petroleum Institute specification 5L[2] for pipeline steel. Products are supplied with mill certificates, giving chemical analysis and tensile properties for the batch of material. In welded fabrications, the weld consumables (wire, rods, flux, and gases) also have their own certificates and standards. Copper pipe for plumbing is specified to BS EN 1057[3], while plastic pipes are given in BS 7291[4] part 1 for PE-X or part 2 for PB. Plumbing fittings are included in the relevant parts of BS EN 1254[5], which deal separately for fittings for soldered joints, threaded fittings, compression, push-fit, or press-fit fittings.
With materials specifications generally having a robust quality system, this leaves the method for making the pipe joints, open to the greatest scope for error.
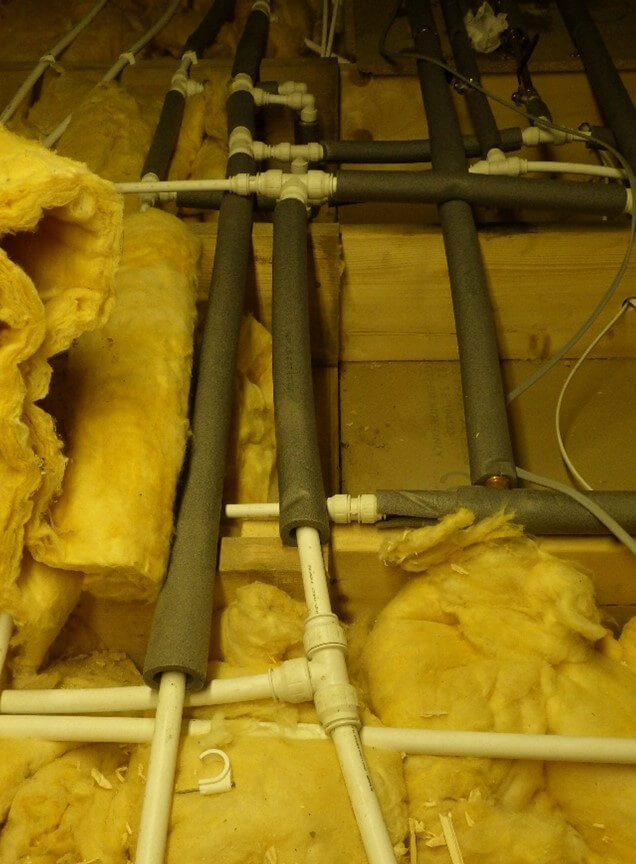
In industrial welding, the weld procedure specification, or WPS, is the ‘recipe’ to produce the weld. This lists the type of joint and alloy to be welded, the arc welding process including its current and voltage, and the welding filler metal that will make the joint. The method is qualified by making a test weld using the procedure, which is then subjected to a full program of destructive and non-destructive testing (NDT) to show that a satisfactory quality weld can be made.
All the welding records, material certificates, and test results certificates form the bundle of paperwork known as the weld procedure qualification record, or WPQR. This approach for ensuring weld quality is common across industries, whether it is a nuclear pressure vessel or a bridge that is being made. Any combination of material to be welded and the welding procedure can be qualified using this approach, following the methods provided in standards such as ISO 15614[6] or ASME BPV Part IX[7]. When performing an investigation into a failure involving any welded structure, a review of the WPS and WPQRs, as well as the welding and inspection records, will often be an important part of the work.
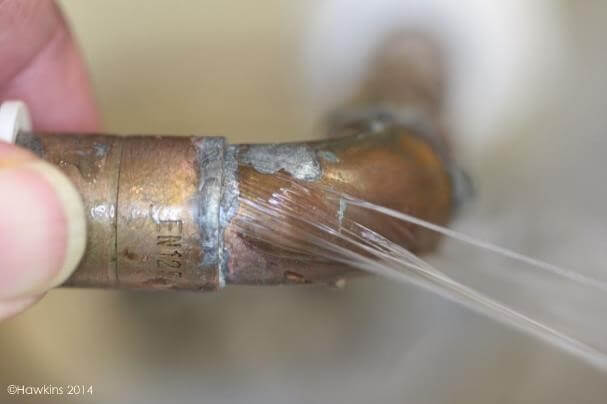
There is no equivalent approach in domestic plumbing installation, where methods have been developed for improving the speed of installation, or to reduce the amount of ‘hot work’ for fire safety. As an alternative to soldering, pressed joints made using a hydraulic tool can provide mechanical joint strength and leak tightness in copper pipes. Manual methods using compression joints and push-fit joints are also widely used and are considered relatively easy to fit. The method used in plumbing therefore is driven by the fitting type and the particular installation instructions for that fitting.
When materials and methods contribute to the cause of a failure, it is often due to a damaged or faulty component or fitting. Sometimes, a fabrication method has been used that is incompatible with the pipe material or fitting, or the fitting was damaged during installation. Less common, but not unheard of, is when rogue materials (with fraudulent paperwork or documentation) have been used in good faith, but are not fit for service. Sometimes the selection of material is inappropriate for the given service, causing corrosion issues later in service (for example), while the material used is the major contributing factor.
Installation Skill
The method for installing pipework is only as good as the skill of the person who does it. In both welding and plumbing, there are established ways that a technician can learn their skill and demonstrate their competency., such as on-the-job training and certification.
Welders are qualified on specific weld procedures and codes based on the quality of a test weld they have made, and they are usually qualified to ASME BPV Part IX or ISO 9606[8]. The qualification is based on the skill of the welder, rather than the mechanical properties of the weld (which are determined by the weld procedure parameters). The welder qualification usually also allows them to weld joints that are considered ‘easier’ than the one used for the test weld. This allows for a wider range of welds to be made from each welder qualification. An example would be a welder qualified on a single-sided joint could also weld double-sided, or a pipe welder could also weld plate.
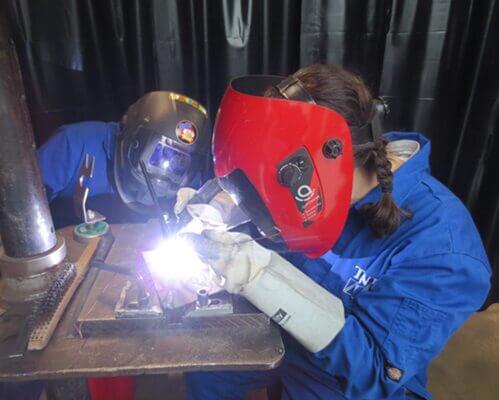
Alternatively, using mechanised or automated welding processes can reduce the number of parameters under the welder’s control and can ensure more consistent quality welds. A welder’s skill is continually assessed since their welds are subject to NDT so that defects can be cut out and repaired. Welders with high repair rates can be identified and given further training.
A plumber who consistently makes poor joints would not necessarily be identified so directly. Teams of plumbers in industrial fit-out or new-build sites can work in a similar manner to welders. However, in domestic settings, plumbing is perhaps more susceptible to installer error, since the plumber could be working on their own, without an independent pair of eyes to pick up on accidental oversights or check the finished work . Plumbing fittings and methods are developed to be ‘easy to install’, but this means that push-fit joints and compression joints that appear to be well-fitted, might not be, if the push-fitting is missing an O-ring, or the pipe is not pushed into the fitting far enough. Compression joints need to be tightened enough to deform the olive on the pipe to make the seal mechanically strong and watertight, but this cannot be determined just by looking at the joint.
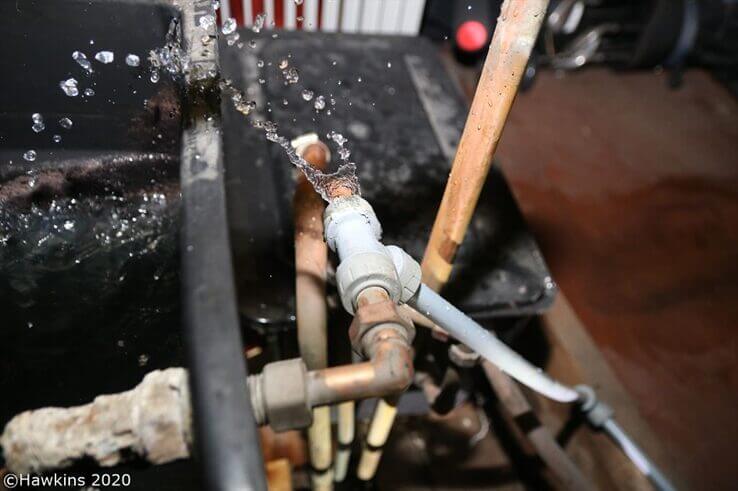
The main way to confirm the effectiveness of the plumber’s joint is by pressure testing it (although ultrasonic test methods exist that can be used on press-fit joints).
Once a plumber learns the basic skills from qualifications and on-the-job training, certification schemes are available to support professional development and competence, such as the Construction Skills Certification Scheme (CSCS), the Association of Plumbing and Heating Contractors (APHC), or the Water Regulations Approval Scheme (WRAS). When investigating a failure that might be due to an installation error, it is prudent to ask for evidence of the installer’s qualification(s) and certification. Although mistakes can happen, installers should have the appropriate skills and knowledge to understand how best to avoid them.
Service Conditions
Even the best materials and installation are at the mercy of the conditions the pipework and equipment will experience in service, in terms of temperature, stresses, and chemical environment.
For welded steel structures, the main concerns are avoiding brittle fracture at low temperatures, preventing fatigue cracking when in service under variable or cyclic loads, and preventing atmospheric corrosion (rust). Welds can also be susceptible to stress-driven environmental cracking such as stress corrosion cracking (SCC) because the intrinsic residual stresses at the weld joint can be sufficient to drive cracks in susceptible combinations of materials and chemical environments. There are many potential in-service damage mechanisms for industrial piping. However, both industry and domestic plumbing can suffer SCC of austenitic stainless steel when exposed to chloride (i.e. salt). In your home, this is more likely to be found in the bathroom as it affects the woven metal in flexible hose connectors. The outer layer is made from woven stainless-steel wire and provides the mechanical strength to support the rubber inner tube containing the water. But exposure to certain cleaning products or bathroom chemicals, or where the metal does not have enough alloying in the steel to be sufficiently resistance, the wires can corrode and the fibres crack. This will be seen as rusting and fraying of the weave, allowing a hole to open for the inner tube to burst.
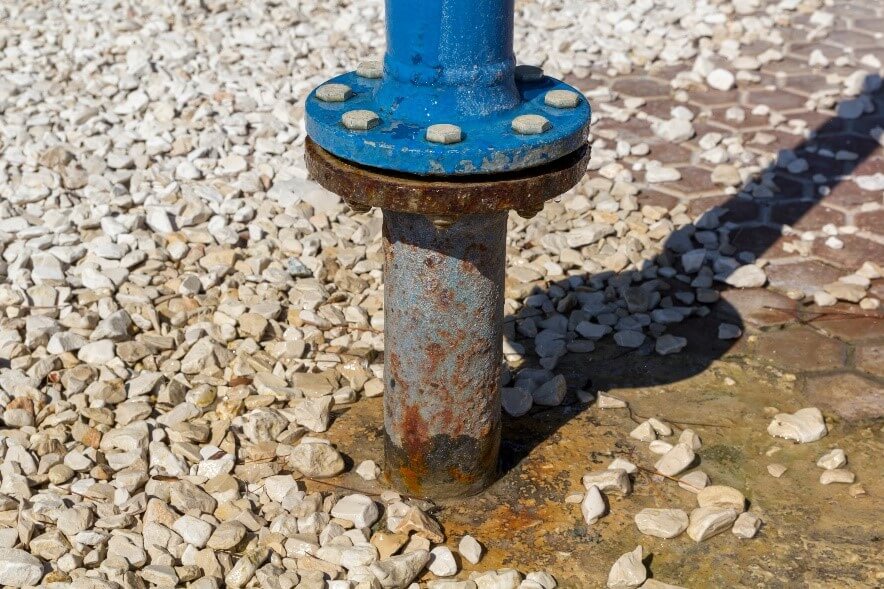
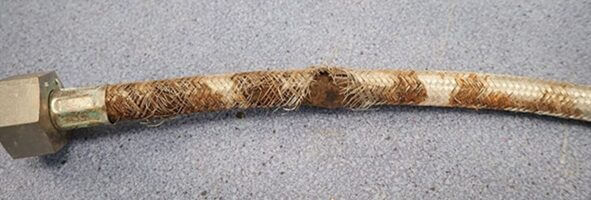
Fatigue is a major issue for welded structures in service, particularly under vibrations, or rotating equipment, as cyclic loads incrementally propagate cracks from stress concentration locations – often weld toes. The magnitude of stress cycles can be low, but can still grow a crack over time, causing the structure to ultimately fail from a secondary failure mode. This is often a ductile overload of the remaining thinned ligament. Fatigue in plumbing fittings is rarer, as they do not usually experience thousands of loading cycles, but can occur in installations where pipework is under high constraint or bending loads. Fatigue cracks in plumbing will initiate from stress concentrations intrinsic to the fitting, such as the threads in compression fittings.
Low temperature in service is a concern for both industrial components and in plumbing, but for different reasons. Ferritic steels undergo a transition from ductile to brittle behaviour as the temperature drops, increasing the risk that they could fail in a catastrophic brittle manner. In domestic settings, low temperatures are more likely to cause pipes to freeze if they are not well insulated. When the water inside a pipe freezes, it causes localised blockages in the pipe, and the water trapped in between these ice plugs experiences an increase in pressure due to the expansion in volume of the freezing ice. The resultant pressure increase can cause copper pipe to burst, or pipe fittings to separate. Upon thawing, the subsequent escape of water can cause significant property damage.
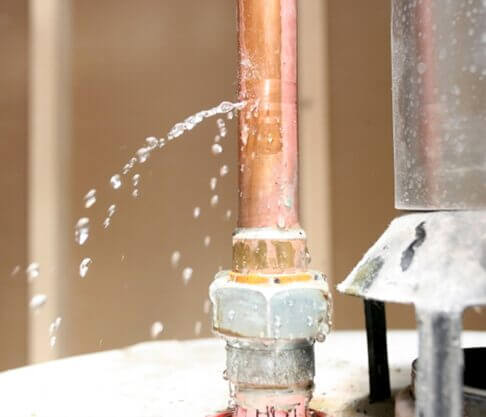
Summary
For cases involving leaking pipework or fluid-containing cylinders, the common themes in the ways they fail can help steer the forensic investigation and ensure all appropriate evidence is gathered. Examination and analysis of the broken component will provide a materials engineer with plenty of information. Their hypothesis must consider whether the damage relates to the materials that have been used, the fabrication methods and the skill of the fabricator, or the conditions experienced in service. The forensic investigator will then be able to seek specifications, documents, records, certificates, or request testing, that can help determine the ultimate cause of leaking pipes and cylinders.
About the Author
Materials expert Dr Philippa Moore joined Hawkins in 2022 and is based in our Cambridge office, where she specialises in materials failures, escape of water and oil, and mechanical and engineering failures. Philippa graduated from the University of Cambridge with MA and MSci degrees in materials science and metallurgy. She then spent 18 years working at TWI Ltd, and developed an international reputation in fracture toughness testing, and engineering failure investigation, often of welded steel structures, through her project work and consultancy. With extensive experience in forensic investigations, Philippa has published over 45 conference and journal papers on her academic research, and on topics supporting her involvement on British and International standards committees for fracture testing.
References
[1] BS EN 10025-2:2019 “Hot rolled products of structural steels – Technical delivery conditions for non-alloy structural steels”, 2019.
[2] API Specification 5L, 46th Edition, “Line Pipe”, American Petroleum Institute, 2018.
[3] BS EN 1057:2006+A1:2010, “Copper and copper alloys. Seamless, round copper tubes for water and gas in sanitary and heating applications”, 2010.
[4] BS 7291-1, 2010 Edition, November 10, 2020 – Thermoplastics pipe and fitting systems for hot and cold water for domestic purposes and heating installations in buildings Part 1: General requirements.
[5] BS EN 1254, “Copper and copper alloys. Plumbing fittings” twenty part standard, 2021.
[6] ISO 15614-1:2017 “Specification and qualification of welding procedures for metallic materials — Welding procedure test — Part 1: Arc and gas welding of steels and arc welding of nickel and nickel alloys”.
[7] ASME BPVC-IX 2023 American Society of Mechanical Engineers, Boiler and Pressure Vessel Code, Section IX: Welding, Brazing, and Fusing Qualifications.
[8] ISO 9606-1:2012, “Qualification testing of welders — Fusion welding — Part 1: Steels”.