The Use of Gas Turbine Engines in The Energy Industry
Gas turbine engines have been a product of choice for many years across the energy industry, operating throughout the world to provide power on demand in a variety of applications.
The industrial revolution of the late 1700’s and early 1800’s instigated rapid economic growth through faster and more reliable manufacturing and production, as well as an improvement in the standard of living. These socioeconomic advances were enabled by the availability of large quantities of power on demand, which came from the chemical energy stored in fossil fuels.
In today’s society, there is an expectation that energy will be continuously available to maintain the safe, comfortable and convenient lives that much of the world’s population has become accustomed to. Gas turbine engines continue to play an important role in delivering this expectation. In power generation applications, gas turbine engines can respond quickly to changes in the grid electrical demand. Although this has always been an important factor, it is becoming even more relevant in terms of maintaining the grid demand, as the energy transition is leading the world towards increased renewable energy, which is irregular and unpredictable. This can be seen in the chart below, which shows the varying power level that gas turbines contributed to the UK power generation production on a single day in 2023. In the oil and gas sector, gas turbines are an attractive option for providing power because of the favourable power density, resulting in a large quantity of power capacity for a relatively lightweight installation, with a small footprint.
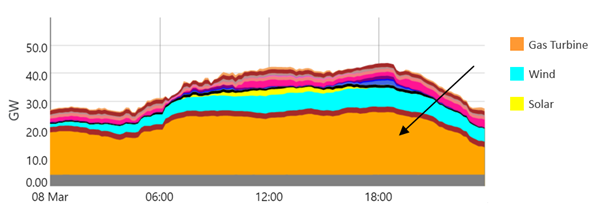
The Economics of Operation and the Benefits of Identifying Emerging Issues
The comfort, safety and convenience, which is brought by the availability of energy has led to energy becoming a valuable commodity. Reliability and availability of equipment is not only important to meet the energy demands, but also to generate revenue. For example, a single gas turbine engine on an oil platform might typically produce 25,000 barrels of oil per day, which at today’s oil price equates to £2m in revenue. In a power generation application, a large gas turbine might typically generate 300 MW of electrical power, which at a wholesale price of £200 per MWh, equates to £1.4m of revenue per day.
If an engine component or system were to fail such that the engine is unavailable, the operator is not only faced with the cost of repair to the equipment, but also the loss of revenue for the duration of the outage. Gas turbine performance monitoring can be one of several tools that can provide early detection of the onset of a failure, which if left unresolved, could escalate into a bigger failure with a higher cost of repair and a higher cost of unavailability.
The following two cases highlight emerging issues with gas turbine engines and the benefits that could have been achieved through prompt maintenance and resolution.
Case 1 – Gas Turbine Operating in Natural Gas Production
A gas turbine engine was in continuous operation at a facility that processes and compresses natural gas. The gas turbine power capacity was being monitored using some simple rules that had been implemented, and the power capacity trend showed a sudden drop in power.
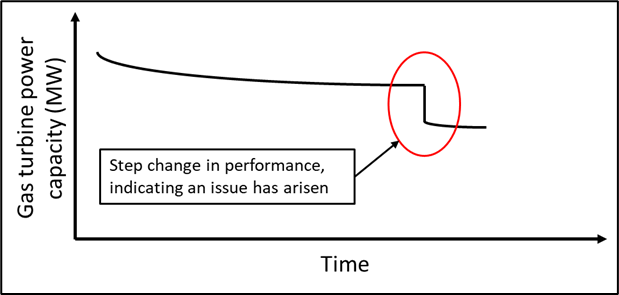
Further investigation of the operating data suggested that one of the on-engine bleed valves (which by design should only be open either at low power or during a fast deceleration) had failed into the open position, resulting in the reduction of engine power that had been observed. This led to the situation where compressor delivery air was flowing through the bleed valve ducting at higher temperature, pressure and flow rate, relative to the design intent.
Upon notification that the bleed valve had failed open, the engine could have been shut down and the failed component replaced within approximately 8 hours, with a spare part that was in stock at the site. However, the engine was not stopped and continued to run with the bleed valve in the open position and at a power level that was above the normal bleed valve closing point. This continued for several days and resulted in the steel ducting rupturing. This rupture caused the package temperature to exceed the shutdown limit, due to the hot compressed air now leaking into the package, resulting in the engine control system to command an emergency stop.
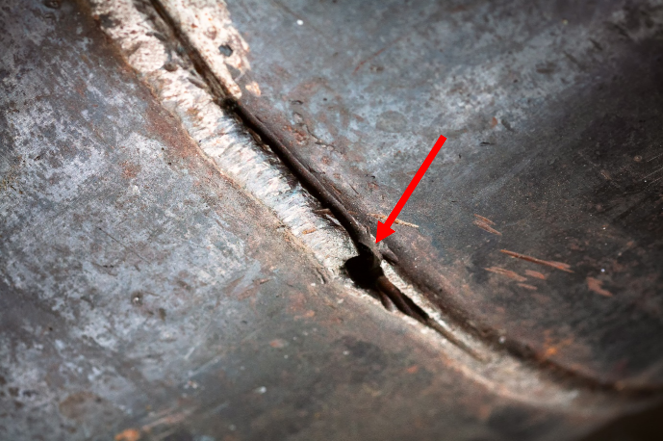
Rather than an 8-hour outage to replace the bleed valve, the gas turbine engine was unavailable for several weeks whilst replacement steel ducting was manufactured.
Case 2 – Gas Turbine Operating In Power Generation
This case occurred on a gas turbine engine operating in a power station that competes in the peaking power generation market. As in the previous case, the gas turbine power capacity was being monitored and showed a sudden but small drop in power.
Further investigation showed that in addition to the small drop in power, there had also been an increase in vibration, and the data analysis indicated that there had been a reduction in efficiency of one of the turbine stages. The whole engine was inspected in the berth using a borescope and as no damage was identified, normal operation continued. Although a borescope inspection is a useful tool in terms of being able to quickly inspect many parts of an engine, there are limitations and not all of the important areas of the engine are accessible using this method.
Four weeks later, a much larger reduction in power occurred, accompanied by a significant increase in vibration. The engine was once again inspected with the borescope, and on this occasion, significant damage was found within the engine. The engine was rejected from service and was returned to the workshop for a full repair.
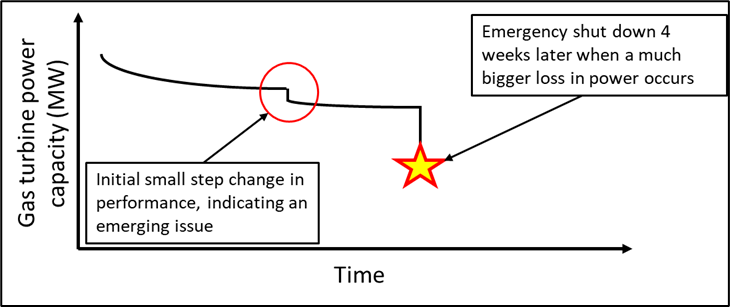
Had the engine been returned to the workshop after the initial observation of a reduction in power capacity, the scope of work to repair the engine could have been much less significant and much less costly. However, by leaving the engine in service following the initial observation, the emerging failure became more serious and led to a more extensive and expensive repair.
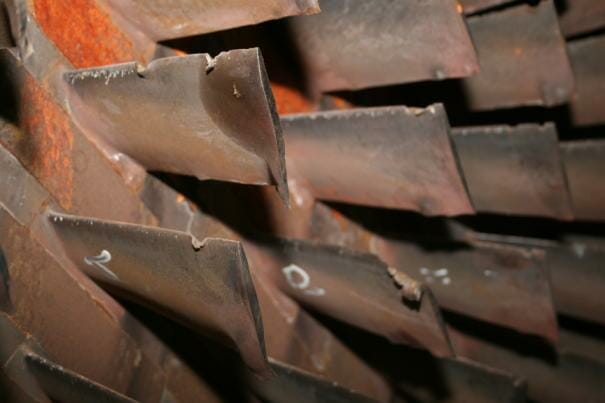
Summary
Gas turbine engines are heavily relied upon within the energy industry to provide the power on demand that society has become accustomed to, and they will continue to remain relevant in their applications throughout the energy transition.
Emerging failures can be disruptive, both in the supply of power, but also to the revenue of the operators. Furthermore, if emerging failures are left to propagate, the cost of repair can increase substantially.
Data analysis can provide a useful method of identifying the onset of a failure and if acted upon quickly enough, can reduce the potential financial loss associated with the failure. Data analysis can also be performed following a failure to determine when engine behaviour changes, what has happened and in what sequence. This not only provides the benefit of being able to understand what happened in an event, but can also help to educate the operators and avoid repeated incidents on other units.