What do I see when I look at rusty steel? Lots… and potentially much more if I can take samples to examine in the laboratory.
At any scene where something has broken, exploded, leaked, or injured someone, and I have been asked to find out ‘What happened?’, I often find that materials science will lead me to the root cause of the failure.
As an engineer specialising in steel structures, metals and welds, this often means there will be some kind of corrosion. In shipping, corrosion damage can be a significant factor in the claims managed, and some examples of common types of incidents investigated by Hawkins are; corrosion of steel cargo, hull corrosion, and wire rope damage.
Rust and corrosion are a natural consequence for steels, and corrosion must be kept at bay through the constant application of corrosion protection methods. For a ship’s hull, deck and machinery, the most commonly used methods are paints and coatings, often used in conjunction with sacrificial anodes for cathodic protection below the water line. For steels used in fluid containment or transport, corrosion inhibitor chemicals can be added to the fluid to prevent internal corrosion. For cargoes of steel products, keeping the goods dry and protected from rain, sea water or sea spray is vital to maintaining the product quality to prevent rusting during transport, so that they arrive in the best condition to be manufactured into their finished product such as may be cars, building frame beams or other machinery or structures. The iron in steel wants to corrode, and we need to actively prevent it from doing so for the duration of the service life, while we exploit the strength and performance of modern steels.
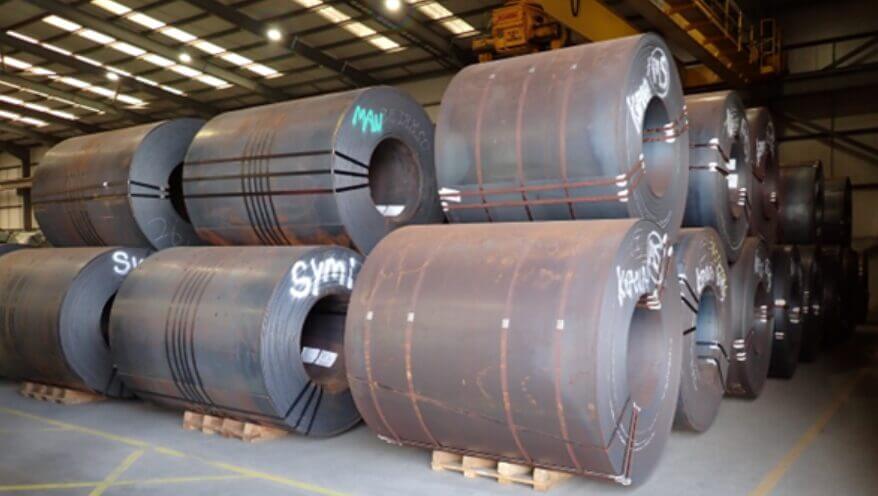
But is it Art?
The first ‘rust’ that forms when iron or steel start to corrode when exposed to moist atmospheric conditions is the bright orange powdery oxide that can be brushed off. Over time another oxide starts to form that is darker bronze or brown colour that forms more evenly over the surface of the iron. While the bright orange coloured oxide is loose and falls off, the brown oxide remains on the surface and provides a more protective patina. Iron can also corrode in water under low-oxygen conditions to form a black coloured oxide. Steel radiators corrode internally to produce this black oxide, which flakes off to form the black sludge inside heating systems. In principle, once the oxygen in the water inside the closed system has been used up, the corrosion rate reduces.
In cast irons, the brown oxide patina can be sufficiently stable to provide permanent protection from further corrosion. Some iron and steel objects make use of progression of corrosion to deliberately create a ‘weathered’ surface appearance. Some garden ornaments are intended to rust, and give a nostalgic charm to a garden design. So rust is not always a problem, and can even be aesthetic.
One of the tempting questions to ask when looking at rust is “How long has it been corroding?”, and/or “How long will it survive?” These are questions that are almost impossible to answer in practise, because the thermodynamics of corrosion depends on a large number of variables, such as:
- exposure to moisture
- exposure to oxygen
- environmental temperature
- steel surface roughness
- condition of paints and coatings
- exposure to chemicals that can accelerate corrosion, such as salt water
So while it is possible to identify that those parts of a fracture surface that have darker brown or black rust will have been exposed to the environment for longer than parts that are freshly fractured, or recently rusting with bright orange rust, it may not be possible to quantitatively say whether that pre-existing damage, for example, has been there for two weeks, six months, or even longer before final failure occurred.
In marine cases, testing the corroded surface with silver nitrate solution can detect the presence of chlorides and help identify whether exposure to sea water has played a part in accelerating the corrosion.
Local Does Not Mean Better
Uniform corrosion is not generally a problem; it eats away at iron and steel slowly over time, and a corrosion allowance of a few millimetres on a nominal plate thickness can accommodate it over a twenty-year design life of a structure under atmospheric conditions. The problems occur when corrosion happens in localised areas, or when the corrosion rate is accelerated. The culprit is almost always the chemical environment.
This type of corrosion can occur without the presence of damaging chemicals. In crevices where water can accumulate, oxygen can deplete, and a stagnant water chemistry forms inside the crevice that can be very different to the general environment. This localised chemical environment can cause corrosion rates to accelerate. This is known as ‘crevice corrosion’. The design of a steel structure can help avoid crevices that might be susceptible, but it can commonly occur around welded features, in the corners of shipping holds, and at overlapping plates, or bolt holes. In wire ropes, such as those used in hoisting assemblies, the steel strands can suffer crevice corrosion from water ingress if the rope’s lubricant has not been maintained.
A localised corrosion mechanism that is similar to crevice corrosion, but which can form on the surface of steel is pitting. Pitting occurs underneath little ‘scabs’ of solid corrosion products (like oxides) that form on the steel, called tubercles. Instead of protecting what’s underneath, they also create a very localised chemical environment that is depleted of oxygen. This localised chemical environment might be sufficient to accelerate the corrosion of the metal surface underneath the tubercle forming pitting that can progress to pinholes in the steel.
Tubercles can form when the initial oxide coating on a metal surface has not formed in a uniform manner. Sometimes tubercles form in closed water systems, such as inside radiators on central heating circuits, when the water treatment has been insufficient to prevent corrosion from occurring. Another cause is bacteria. Microorganisms inside closed water systems form biofilms over the steel surface, and this can result in locations providing ideal conditions for colonies of certain bacteria, with different bacteria thriving in either oxygen-depleted environments or oxygenated water. Tubercles formed of a mixture of corrosion products and biofilm products protect the bacteria beneath, which can eat through the steel causing pitting. This is called microbially induced corrosion, or MIC.
Cracking Under the Stress
When stress is applied to the steel, the corrosion mechanisms can become even more damaging as environmental cracking occurs. Environmental cracking is defined as the brittle fracture of a normally ductile material in which the corrosive effect of the environment is a causative factor. Mechanisms of environmental cracking include stress corrosion cracking (SCC), and sulphide stress cracking (SSC) in steels. Stress-driven cracking mechanisms require the critical combination of the susceptible alloy, its corrosive environment, plus the application of stress. But this stress could be residual stress from welding, or the effect of stress concentrations at machined threads or changes of section, in addition to the applied stresses inherent to the application. Environmental cracking is one of the most damaging corrosion mechanisms as it can propagate quickly and cause catastrophic failure of equipment in some cases.
Steels are affected by any corrosion or degradation mechanism that generates atomic hydrogen inside the steel. Hydrogen atoms are highly mobile within steel, and will migrate to locations of high stress, such as at crack tips. Although modern engineering steels are generally ductile, the hydrogen atoms embrittle the steel crystal structure, making it locally brittle and so it cracks a small amount, allowing the crack tip to move forward, in an incrementally repeating way as the cracking propagates. For carbon steels there are three main types of environmental cracking, which all generally show a branched-type of cracking. On a fracture surface, this might appear as secondary cracks that propagate perpendicular to the fracture face, particularly around grain boundaries.
When steels are exposed to wet hydrogen sulphide (the gas that has a rotten egg smell), the chemical reactions on the steel surface pump hydrogen into the steel, and cracking known as sulphide stress cracking can occur rapidly. Keeping the steel surface below the susceptible hardness limit is key to avoiding this type of cracking. While sulphide stress cracking is mainly a concern in the petrochemical industry and the extraction of ‘sour’ oil and gas, there are means by which hydrogen sulphide can occur in other environments and attack steels.
Stress corrosion cracking in carbon steels can occur when they are exposed to high pH (i.e. alkaline) conditions from chemicals such as carbonate or bicarbonate environments. The cracking propagates along the steel’s grain boundaries (called ‘inter-granular’ cracking). Even under near-neutral wet conditions, steels can suffer from a different kind of SCC where the cracking propagates through the steel without being affected by the microstructure’s grain boundaries (‘trans-granular cracking’).
Corrosion Conclusions
There are many ways that the environment can corrode and damage steels, and a forensic materials engineer will look for clues from the appearance of the corrosion products and the corroded surface, and details of the exposure conditions, to help identify when the damage could be something more significant, because corrosion is Not Just Rust.
About the Author
Dr Philippa Moore is a materials expert with Hawkins & Associates. She specialises in materials failures, escape of water and oil, and mechanical and engineering failures. She has provided expertise on topics related to welding engineering, materials science & metallurgy, failure modes in metals, and structural integrity on cases worldwide and has published over 45 conference and journal papers on her academic research, and on topics supporting her involvement on British and International standards committees for fracture testing.