Iron is one of the most common and important metals on earth and forms the basis of the most widely used group of metallic materials, steels. Steels can be manufactured cheaply, in large volumes, and provide a range of useful mechanical properties; hardness, strength, ease of machinability, heat resistance, corrosion resistance etc. The properties of steel can be altered by the addition or removal of chemical elements or by heat treatment. Hence, the performance and longevity of steel components often relies on correct property specification and manufacture. If, for instance, a steel application requires exemplary corrosion resistance, but the steel has been incorrectly manufactured or specified, the component will be unlikely to perform effectively and may fail prematurely.
A great example of a large structure made from steel is the Forth Bridge[1] in Scotland, built between 1883 and 1890 (before the advent of corrosion resistant steels). The Forth Bridge is an example of a steel structure which, up until 2011, had to be continuously painted to protect it from the effects of corrosion.
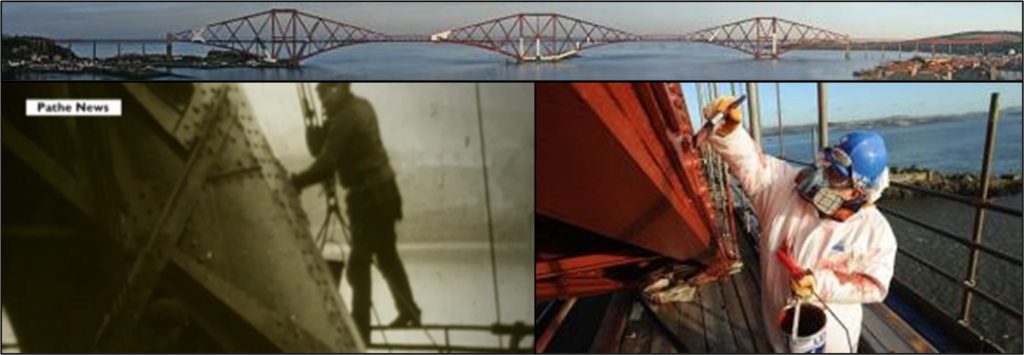
The painting of steel surfaces to protect them can be impractical, costly and is often only a short term solution. Although expensive for structural applications, the benefits of corrosion resistant steels can be easily recognised. In the last decade, large structures such as Azerbaijan’s Flame Sculpture and Chicago’s Cloud Gate have been manufactured from stainless steel; the term stainless steel is used to refer to those steels which are resistant to corrosion.
The term “stainless” was originally coined in the early development of these steels for cutlery products in 1913 by Harry Brearley (born in 1871) of Sheffield.
These new “stainless” cutlery products no longer required polishing to remove any tarnish from the surface. The term was widely adopted and is now used to describe a range of steel types and grades for corrosion or oxidation resistant applications.
HOW DO STAINLESS STEELS DIFFER FROM OTHER STEELS?
Stainless steels differ from plain carbon steels by the amount of chromium present in their chemical composition. Carbon steels corrode readily when exposed to both oxygen and moisture. In order for a steel to have corrosion resistant properties (and be considered a stainless steel) it must have a minimum chromium content of at least 10.5 wt% (more is often required depending on the other constituents of the steel). Other alloying elements such as nickel, molybdenum and nitrogen are added to modify the steel structure and enhance required properties, such as formability, strength etc. However, for stainless steels to be resistant to acids such as hydrochloric acid or sulphuric acid, even higher concentrations of chromium are required.
Steels containing sufficient chromium form a passive film of chromium oxide on the surface. This prevents corrosion by limiting oxygen diffusion to steel beneath, and is known as passivation. While this passive layer is extremely thin (and invisible) it adheres firmly to the surface of the steel and is self-healing, provided there is sufficient oxygen available. For example, if a stainless steel is scratched or dented, oxygen in the atmosphere combines with the chromium in the stainless steel, reforming the protective layer.
Nevertheless, the passive surface layer can be broken down in certain conditions, so it is vital that the appropriate grade of stainless steel is chosen for particular applications, or the stainless steel will corrode.
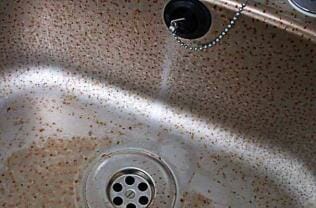
CATEGORIES OF STAINLESS STEEL
In engineering design, properties other than corrosion resistance are important and for this reason there are a variety of alloys available. This range of alloys can be classified into four main categories defined by the metallurgical crystals or phases present within the steel structure. These phases are known as ferrite, martensite and austenite and whilst most stainless steels are predominantly of one these phases, a duplex structure (a mixture of ferrite and austenite) is adopted in some cases. Micrographs showing the crystal structure of these phases are shown below.
The four main phases of stainless steel as marked. Micrographs credit to http://pwatlas.mt.umist.ac.uk/internetmicroscope/index.html
Austenitic stainless steels exhibit superior corrosion resistance when compared with ferritic or martensitic stainless steels, but austenitic grades are generally more expensive. Corrosion resistance in austenitic stainless steels can be varied to suit a range of corrosive environments by varying the carbon or molybdenum content.
Austenitic steels include both the “200 and 300 series” stainless steels. A few examples of common grades are given in the table below. Traditionally, nickel is the most commonly used element to produce the austenitic phase structure in 300 series steels, however in the late 1930s a shortage of nickel led to the substitution of nitrogen for nickel (which also forms the austenitic phase structure), which gave rise to the creation of the 200 series of stainless steels. In order to reduce the nickel content and maintain the austenitic phases structure, the amount of chromium is reduced and so that nitrogen can be safely added to the steel, manganese is also added. This has the overall effect of decreasing the chromium oxide passivation effect and therefore, reducing the corrosion resistance of the steel.
CHEMICAL COMPOSITION OF 201, 202, 205, 304 AND 316 GRADE STAINLESS STEELS:
Grade | Chemical composition (wt %) (max unless otherwise stated) | |||||||||
AISI | Cr | Ni | Mn | N | Mo | C | P | S | Si | |
316 | 16.0-18.0 | 10.0-14.0 | 2.0 | 2-3 | 0.08 | 0.045 | 0.03 | 1 | ||
304 | 18.0-20.0 | 8.0-10.5 | 2.0 | 0.08 | 0.045 | 0.03 | 1 | |||
201 | 16.0-18.0 | 3.5-5.5 | 5.5-7.5 | 0.25 | 0.06 | 0.03 | 1 | |||
202 | 17.0-19.0 | 4.0-6.0 | 7.5-10.0 | 0.25 | 0.15 | 0.06 | 0.03 | 1 | ||
205 | 16.5-18.0 | 1.0-1.75 | 14.0-15.5 | 0.32-0.40 | 0.12-0.25 | 0.03 | 0.03 | 0.5 | ||
200 AND 300 SERIES STEELS
Today, the high price of nickel means that it is much cheaper to manufacturer 200 series steels, which have a lower nickel content, than the 300 series steels, see Table 1.
Although the 200 series steels are corrosion resistant, the 300 series offers far superior protection against corrosion in high moisture and chlorine containing environments, due to the higher levels of chromium in the composition.
The 300 series stainless steels also offer protection against stress corrosion cracking (SCC), which is a progressive crack growth mechanism that occurs with some metal alloys when they are subjected to stress and corrosive chemicals. In order for SCC to occur the metal must be under stress and in contact with a specific corrosive chemical in a moist environment. For austenitic stainless steels, chlorine (which is often found in cleaning products, amongst other origins) is the most common species known to cause SCC. However, the 300 series stainless steels has increased resistance to corrosion and is also impervious to chlorine induced SCC below about 60 °C.
ABOUT THE AUTHOR
Dr Eleanor Jay is a materials science engineer with a background in energy generation and storage, risk and safety analysis and the nuclear industry. She has been involved in all aspects of product life cycle, from fabricating materials to designing against and investigating the causes of material failure. Materials engineering is at the heart of everything we touch and see, from those objects in our everyday life to space rockets. Our world is constantly producing new materials to meet novel and challenging environments. Appreciating the material properties, strengths and limitations is crucial in understanding the world we live in, particularly when things go wrong. Eleanor has particular expertise in metallurgy, polymers and ceramics.
At Hawkins she has investigated a range of failures of systems, structures and materials. For example, she has examined the causes of escapes of water from plumbing fittings and swimming pools, malfunction of a biomass boiler, failures of ceramic ware and glass panels, degradation of copper and one of the most fundamental material failure mechanisms, corrosion.
[1] http://www.bbc.co.uk/news/uk-scotland-edinburgh-east-fife-33397980