Broad estimates put the cost of corrosion to 1 to 4 % of GNP in the USA. Whilst an accurate figure would be elusive to even the most rigorous rational, it is fair to say that repairing the consequences of corrosion is a costly business. Brass and austenitic stainless steel are widely used in engineering applications to convey liquids, such as water, or for pressurised applications, such as heat exchangers, steam generating equipment and pipework. As such, stress corrosion cracking can result in catastrophic, and costly, failures of this equipment.
WHAT IS STRESS CORROSION CRACKING?
Stress corrosion cracking is a specific type of corrosion that often causes failures of engineering components. Stress corrosion cracking occurs over time, with little readily apparent evidence of the degradation of the metal. In addition, it occurs at stresses much lower than those required to produce a spontaneous failure due to overload (i.e. below the yield strength and often at normal service stresses).
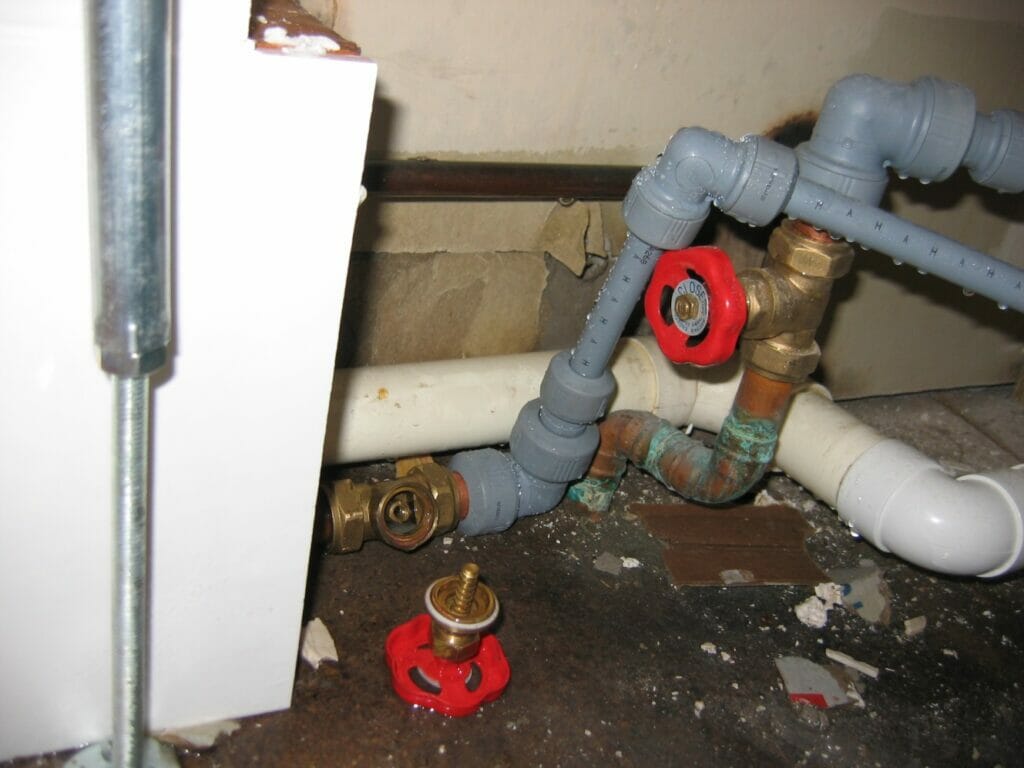
SIGNS OF STRESS CORROSION CRACKING
Branched cracking is a common characteristic of stress corrosion cracking. When viewed at high magnification the fracture surface of a component that has failed due to stress corrosion cracking has a faceted and granular appearance (Photograph 2 below). In contrast to this the fracture surface of a component that has failed due to a ductile overload failure typically has a dimpled appearance (Photograph 3 below). The facets and granular appearance actually reveal the small individual crystals (grains) that comprise the microstructure of the majority of engineering metals.
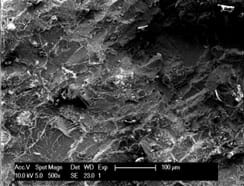
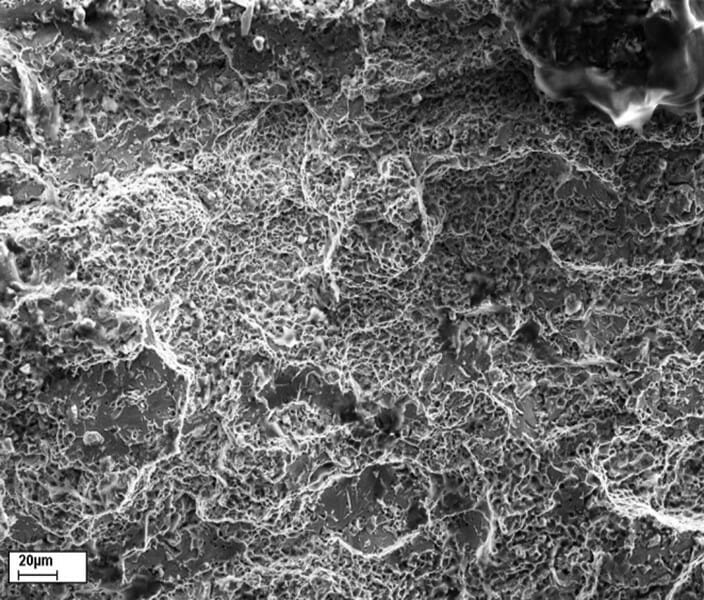
SOURCES OF STRESS
A susceptible material, a tensile (pulling) stress and a specific corrosive species all need to be present simultaneously for stress corrosion cracking to occur. The stress can be from two sources:
- The first source of stress is from an applied stress. Applied stresses are those produced by service, such as the water pressure within a pipe, stresses produced by assembly of the item or the weight hanging from a fixture.
- The second source of stress is from residual stress in the material. To some extent residual stresses are present in all materials and are often produced by relatively rapid cooling from elevated temperatures during manufacture.
REDUCING THE LIKELIHOOD OF STRESS CORROSION CRACKING
- Efforts can be made to reduce the stress that the component is subjected to; simply by adding more metal or removing stress raising features.
- Operating stainless steels below 60°C can also be beneficial in avoiding stress corrosion cracking, but this does not hold true in all circumstances.
- Annealing the component post manufacturing. Annealing is a thermal process where the metal is heated to a specific temperature and then cooled slowly. This relieves the residual stresses in the metal and thus significantly reduces the pre-disposition of a component to fail by stress corrosion cracking.
- Where possible, avoid using alloys that will be exposed to the chemicals known to cause stress corrosion cracking for that alloy type.
Examples, of known species that cause stress corrosion cracking and the metals they affect are:
Specific Chemical Species |
1. Aqueous (water based) chloride, bromide and iodide solutions 2. Aqueous chloride solutions 3. Nitrate, hydroxide and carbonate/bicarbonate solutions 4. Ammonia (and ammonia containing chemicals such as urea) and nitrates |
Affected Metal(s) |
1. Aluminium and titanium alloys 2. Austenitic stainless steels and magnesium alloys 3. Carbon steels 4. Brasses. Brass is principally an alloy of copper and zinc
|
ABOUT THE AUTHOR
Neville Tranter started investigating mechanical failures in 2005. Since then he has investigated the failure of a wide range of components, systems and structures; from medical devices such as stents and prosthesis, to bulk storage tanks, drilling Derrick and oil well drilling equipment, through aerospace and rail components, plumbing systems and many things in between. His background in Metallurgy makes him ideally placed to understand the design of equipment, the materials they are made out of, manufacturing processes used to produce them, service life and how these factors can result in failure.