The Engineering industry is a broad church and the effective management of any machinery, equipment, or process over its lifetime involves many skill sets. However, what is an incontrovertible truth is that an integral part of the effective life cycle management of any such equipment is maintenance. A UK HSE briefing document describes maintenance as follows:
Maintenance is carried out on buildings, plant, equipment, and vehicles to enable it to perform the function required of it. Corrective (repair/breakdown) and ongoing preventative maintenance tasks are carried out in all sectors and all workplaces.
Maintenance includes preventative routine actions such as cleaning, lubrication, inspection, and thorough examination. It includes corrective actions when a fault is detected or a break-down occurs such as repairs, replacing parts or clearing blockages.
In my experience, the fundamental reason for undertaking maintenance is to preserve the economic worth of an asset and to ensure that it functions safely, and in line with its design intent. A popular term amongst the maintenance fraternity is maximising equipment ‘uptime’.
Anyone who is involved in the Hawkins’ core business of investigating fires, engineering failures, unscheduled releases to the environment, and personal injuries cannot escape the impact that maintenance has in preventing such incidents, but also must be aware that maintenance activities often actually contribute to or even directly cause these types of incidents. Those who have worked with loss adjusters will recognise the optimism and expectation when they tell you that the loss they are working on involves their insured’s equipment having just been maintained by a third party, or the reservation in their voice when they tell you that their insured has recently maintained an item of equipment for a third party and now there has been a fire.
The Health and Safety Risks Associated with Maintenance
Grim statistics suggest that one in three workplace fatalities are caused by maintenance related incidents.
A consistent theme of improvements to industrial safety standards over the last 150 years, is that machinery and processes are more and more designed to be inherently safe during normal operation. As early as the 1844 Factories Act, a provision was introduced to prohibit children and women from cleaning moving machinery. This trend has continued, and modern legislative and safety directive requirements specify the highest levels of engineering controls, such as guarding, interlocking, noise abatement and exhaust ventilation, to make equipment safe in normal operation.
However, by inherent definition, maintenance activities require a deviation from normal operation. They almost always involve some form of invasive activity that requires the engineering controls to be rendered inoperative. Maintenance often requires the removal of guards and covers, the removal of pipes and the exposure of electrical conductors. If maintenance work is to be planned and executed safely it requires a Safe System of Work (SSOW) that addresses the dangers inherent in the maintenance task. An SSOW for maintenance typically relies on procedural and management systems based upon the assessment of risk, and the implementation of control measures such as locking off equipment, Permits for Work, supervision and the competence of staff.
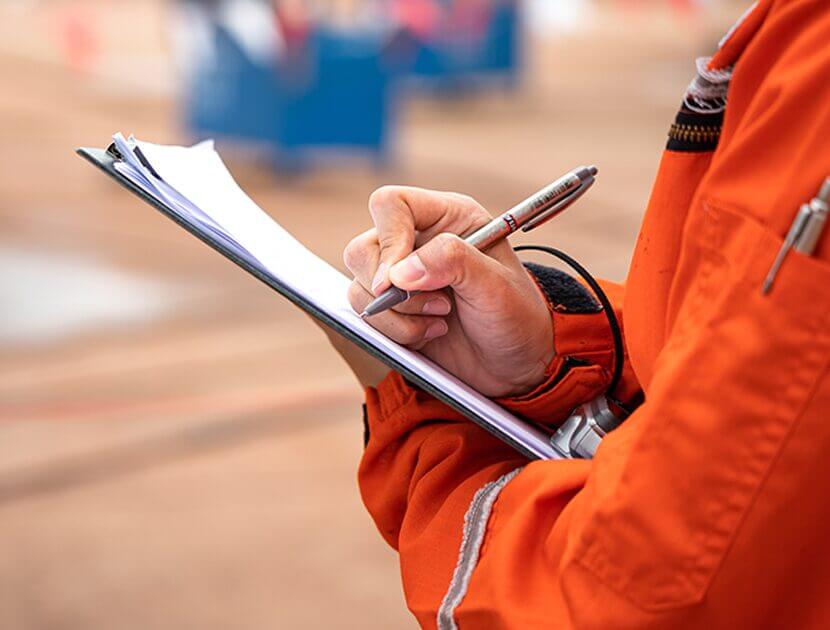
The complexity of an SSOW for any maintenance task will depend on a variety of factors such as the type of equipment, its operating environment and the work to be undertaken. The appropriate SSOW for maintaining lighting equipment in a warehouse is different to that required during a major maintenance overhaul of a refinery, or maintaining a piece of heavy plant in a quarry. Hawkins engineers are experienced in all aspects of mechanical and electrical maintenance, on all types of machinery and process engineering plants.
It can often be overlooked that the very activity of making something safe to work on, can itself be hazardous. A fundamental part of an SSOW is providing safe access. Typically, in process plants and factories this involves the use of scaffolds. My experience has highlighted that the dangers and hazards presented to those erecting scaffolds are often underestimated as two of the three workplace fatalities that I have witnessed during my maintenance career have involved scaffolders engaged in providing safe access for others.
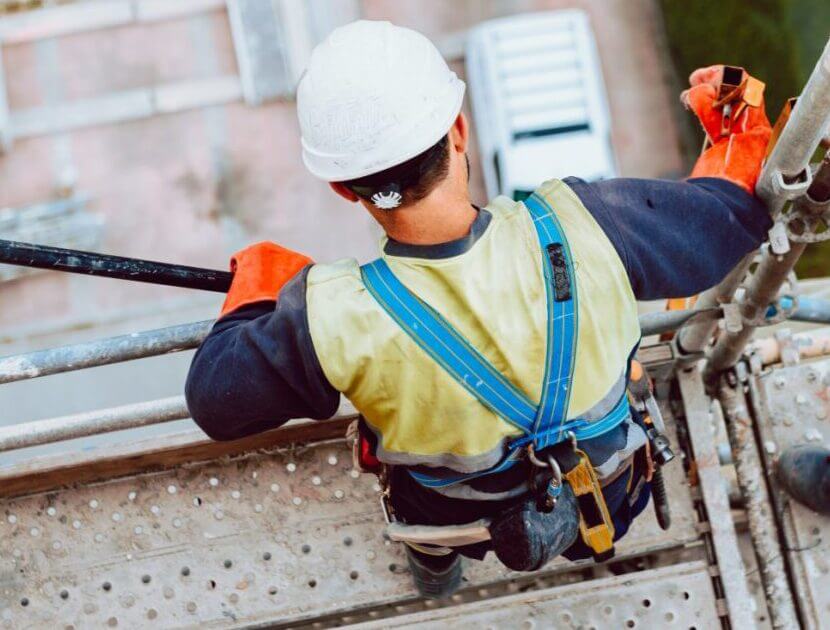
Safe maintenance of pressure vessels, silos and tanks typically requires those vessels to be depressurised, drained, purged and vented. If not correctly managed, these activities, which involve the safe dissipation of potential energy, can cause injury as well as present the risk of accidental releases to air and water.
Equally hazardous is the return to service phase, where plant and equipment are being recommissioned and tested, but are not in a fully operational condition with all protection systems in place.
It has historically been perceived that there has been a disconnect between the objectives of the designers of equipment and the end user’s requirements in terms of long-term maintainability. The Construction and Design and Management Regulations require the following:
CDM 2015 Regulation 9 requires designers to eliminate or reduce risks to those involved in maintenance so far as reasonably practical or, if that isn’t possible, to provide information on significant residual risks.
This is a positive step in improving maintenance safety, by designing maintainability at the start of any project. However, many maintenance tasks occur on facilities constructed before the CDM Regulations were in force and perhaps more importantly, the legislation itself does not make the world a safer place. The maintainability of new equipment requires the correct specification for that equipment and the proactive management of the overall procurement process.
The Unintended Consequences of Maintenance
The unintended consequences of maintenance typically fall into the following categories:
- An adverse outcome associated with the work process;
- A deficiency in the quality of the maintenance work, leading to maintenance induced failures.
One of the most common adverse outcomes associated with an inappropriately managed maintenance work process is fires caused by hot works. Flame cutting, grindings, welding and brazing are fundamental ‘tools of the trade’ of most maintenance work. Other very specific activities such as roofing work and plumbing can also involve hot work. Hawkins’ Engineers are experienced in hot work processes as well as investigating hot work fires and interpreting hot work policy endorsements.
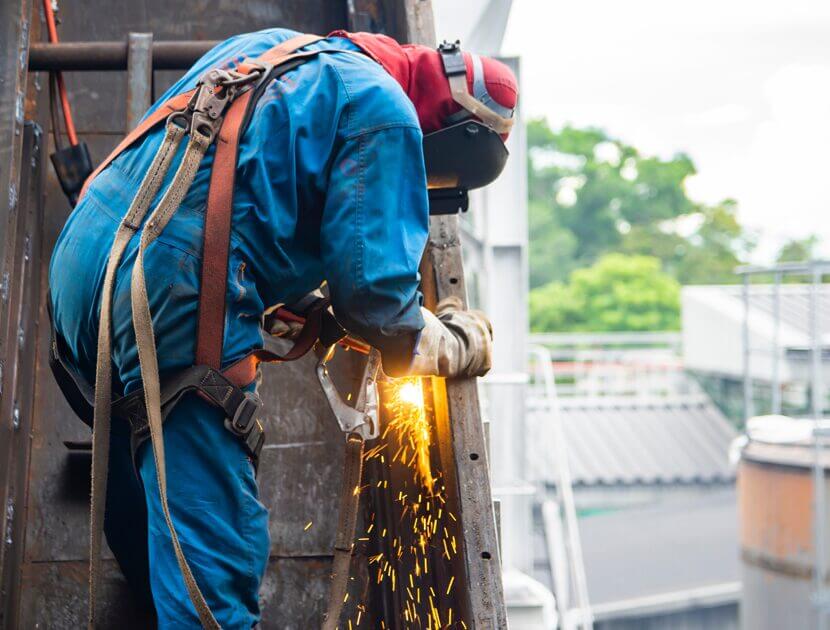
However, it is not just hot work processes that present a risk; a whole manner of maintenance work processes can have unintended consequences. Chemicals used for both cleaning and disinfecting can cause corrosion to pipework systems and heat exchangers if not correctly flushed after maintenance procedures. Some high-temperature fasteners can be adversely affected by certain types of grease and lubricants.
Adverse effects due to poor quality control during maintenance itself can range from a simple one-off error such as installing seals the wrong way around or the incorrect tightening of fasteners, to the incorrect alignment of a rotating steam turbine component. Nevertheless, however simple the error, the impact on lost production and the associated repair time can be hugely disproportionate. This highlights why all phases and activities within a maintenance task are of equal importance and require the highest levels of planning and scrutiny.
There is nothing magical or unattainable about ensuring consistent quality during maintenance activities. However, it does require attention to detail in terms of specifying the task, assessing the work, ensuring that the correct resources are employed to undertake the work, and ensuring that they are correctly supervised and supported.
A particular and often neglected risk associated with the wider maintenance process is change control. Anyone who works in the world of risk management will be familiar with the concept of change control, yet it is easy to view it as a dull topic only relevant to high-risk but well-managed industries such as nuclear power or petrochemicals. However, in all industries, not only those perceived as high risk, obsolete equipment is routinely replaced with new modern equipment. Many engineering losses occur as a result of wider system failures, not just individual equipment item failures. Equipment items typically interface with a wider system, and a failure to adequately assess the impact of changing a single component to a similar, but slightly different, design can be catastrophic. It should never be forgotten that the 1974 Flixborough disaster, where an explosion at a chemical plant resulted in 28 fatalities, was most likely linked to an improperly assessed plant modification. The disaster gave impetus to the 1974 Health and Safety at Work Act.
Maintenance work can be safely managed in many different ways. It may be undertaken by in-house staff, third-party contractors or often by a combination of the two. Whichever approach is adopted, the correct management of maintenance cannot be ignored however simple the task is perceived.
Hawkins frequently investigates cases where companies have acted responsibly and appointed specialist contractors, yet things have still gone tragically wrong. All organisations should remember that the management of Health and Safety at Work regulations requires the sharing of health and safety information between organisations. You simply cannot contract out your health and safety responsibilities.
Summary
If undertaken correctly, maintenance ensures that equipment designed to be safe during normal operation continues to be safe over its life cycle, and preserves the economic worth of that asset.
The process of maintenance itself contains inherent hazards as a result of the equipment departing from its normal ‘safe’ operational design condition.
Safe Systems of Work during maintenance work typically involve procedural systems and high levels of supervision.
About the Author
Nick Ashby is a Chartered Engineer, who has more than 35 years of practical operations and maintenance experience of heavy electrical and mechanical equipment in the power generation industry.
Prior to joining Hawkins, Nick was an Operations Manager at Seabank Power Station where he was responsible for a department of 24 Engineers and Technicians and managing all aspects of Health, Safety and Environmental compliance. Following this, he progressed to the position of Maintenance Manager, taking responsibility for the engineering integrity of all electrical and mechanical assets.
Hawkins Engineers are experienced in all aspects of maintenance, maintenance management and accident investigation, and can support you in any failure with a maintenance element. If you would like to know more about our services and how we can help, visit our website or get in touch.