Investigations to identify both the origin and cause of fires form a large portion of Hawkins’ cases. An experienced fire investigator will make their initial observations at the fire scene to identify where the damage is most severe, whether there are anomalies in the damage and debris, and whether a source of the ignition can be identified.
The heat of the fire causes damage to different materials in different ways. Organic materials such as wood and paper can be completely consumed to ash, and plastics may be melted and burnt to almost unrecognisable residues. However, a fire will not always cause complete destruction. Following the patterns of burnt and unburnt wood damage, or where plastics or paint coatings have either charred, softened, or melted, can help track the fire spread and identify where the most damage occurred, which is often where the fire started.
Broken Glass
Glass windows will not usually reach temperatures hot enough to melt in a fire, but broken windows are often present at fire scenes, not least because the heat of a fire can crack glass panels due to thermal stress. Broken windows can be a result of someone breaking in to deliberately set a fire or may have been broken by the fire service to gain access or to assist with clearing smoke from the building. A fire investigator needs to recognise glass fracture patterns consistent with a thermally cracked window, differentiating them from those that have been deliberately broken, as this can have significant consequences for the potential recovery or repudiation of a claim. Cracks from heat damage initiate from the edge of a window and propagate around the glass panel in a gently curving shape. In contrast, a glass window that has been hit or struck will show an impact mark with cracks propagating radially from the point of impact where the glass may be crushed.
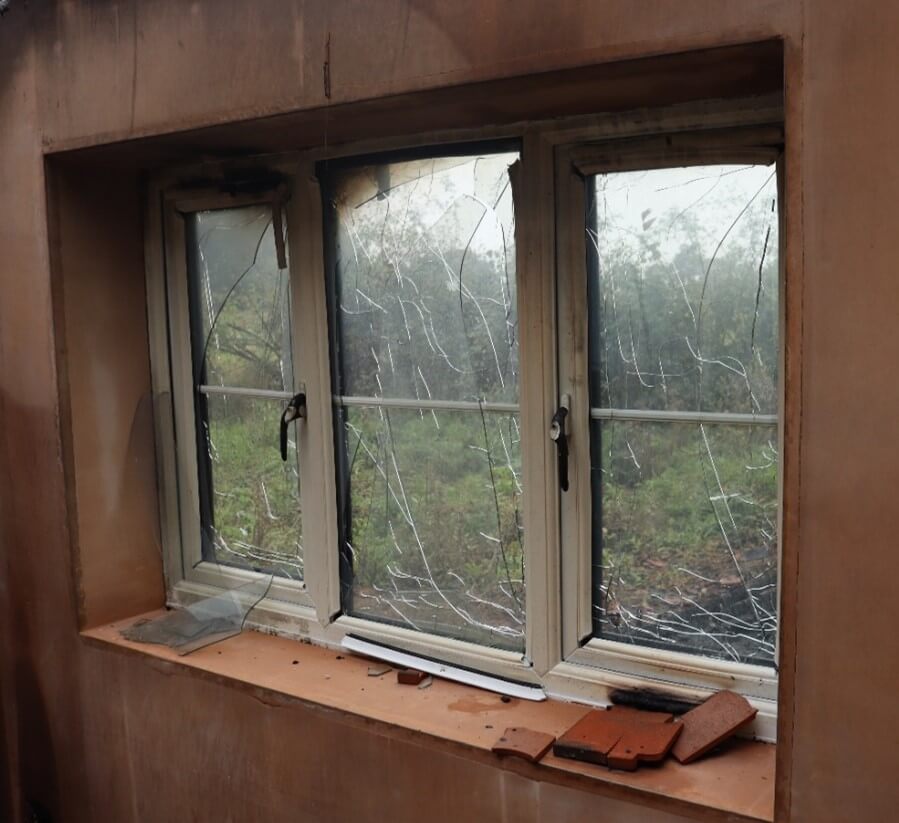
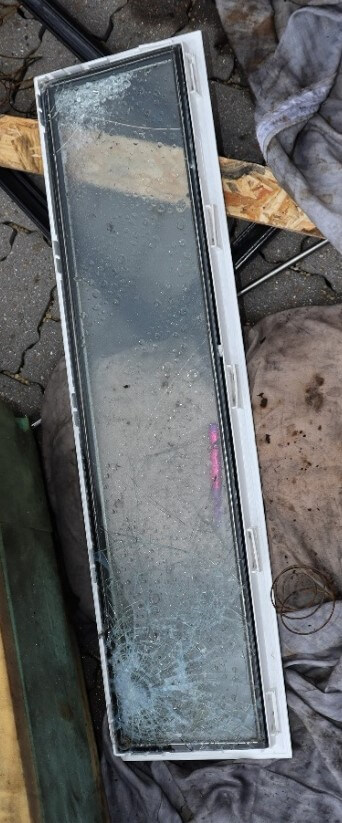
Heat-damaged windows (left) and impact damage to a glass door panel indicated with an arrow (right).
In addition to recognising the cracking patterns, investigators will also examine any glass fragments that have fallen from the window. Identifying if the fragments are soot-stained, and whether the glass has fallen inside or outside the window, will determine when and how the window was broken.
Fire Damage to Structural Steel
After large fires, the majority of identifiable materials that remain are metals, because they do not burn in fires, but they may melt or soften. A typical domestic or vehicle fire can reach temperatures in excess of 900°C. The fire is unlikely to get hot enough to melt iron and steel (above 1500°C), but even metals that don’t melt will nonetheless be affected by the heat of a fire, as the yield strength of metals and alloys reduces at higher temperatures. The strength of steel can be reduced by half when it is heated above 500°C. This means that steel beams can bend, distort, and buckle, and can cause the collapse of a roof structure under the heat of a fire. This presents a significant risk because the temperature will be highest at the roof level in an enclosed building fire.
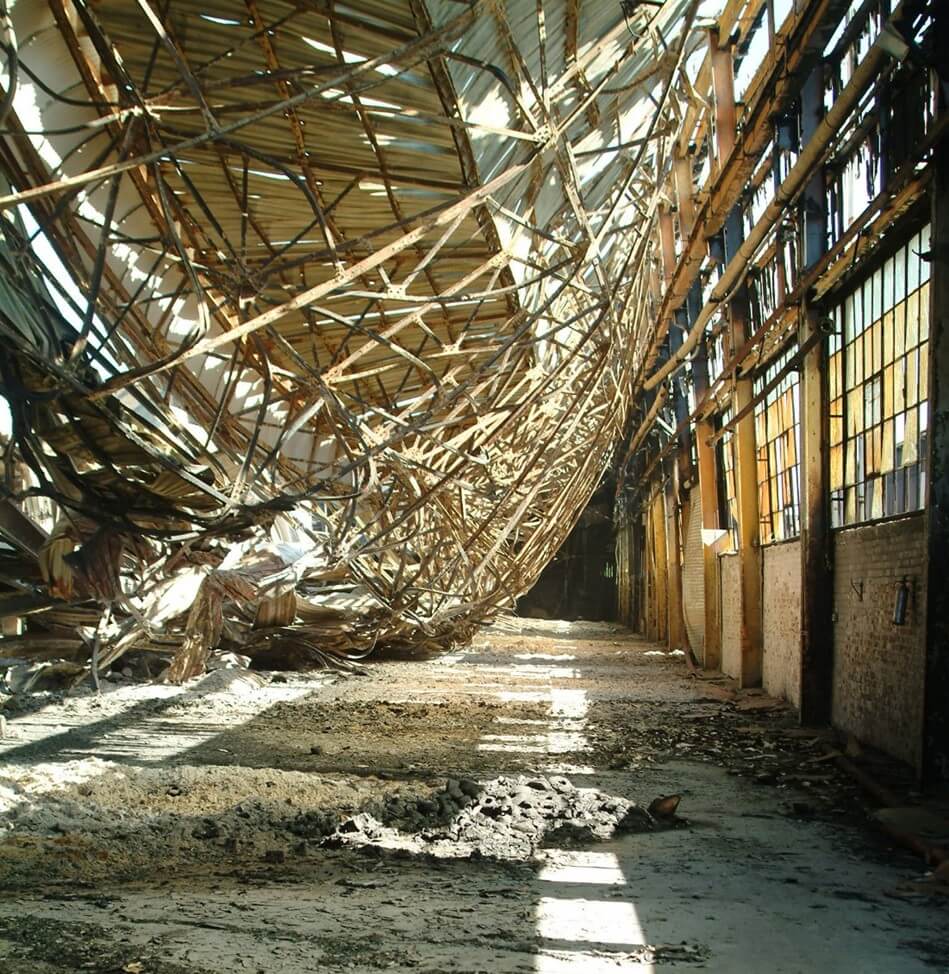
When steels are heated above 723°C they go through what is known as a ‘phase change’ and the microscopic crystalline structure of the solid steel (i.e. its microstructure) changes. When it cools back down again, a steel that has been through a phase change usually ends up with a different set of room temperature properties; i.e. after a phase change the steel has been permanently altered by the heat of the fire. In contrast, steel that has been exposed to a heat lower than 723°C retains the same microstructure once it cools down, and therefore returns to its original room temperature strength. Whether a steel beam or component has been permanently affected by the heat of a fire can have implications for the insurance claim value and the possible repair options. By looking at the microstructure of the steel, it is possible to determine whether steel has been fundamentally damaged by the fire.
To reveal a metal’s microstructure, the metal sample’s surface is first polished to a mirror finish. This is done by grinding, using increasingly finer grades of sandpaper and then polishing with diamond polishing paste. The polished surface is then etched with an acid, which eats away at the boundaries around the crystalline grains in the metal microstructure. The etched surface can then be examined using a microscope to reveal the microstructure, i.e. the size, shape, and arrangement of the crystals of different constituent phases of the metal. For metal components in service, the microstructure can be captured using the local preparation of a small polished and etched surface, and then laying a softened sheet of thin acetate over the surface which embeds into the etched grain boundaries. A replica of the microstructure is captured on the acetate sheet, which can then be taken from the site for a microscopic examination at a laboratory. Comparing the microstructures from undamaged areas to those that have been in the fire, can show whether a steel has been heated sufficiently to be permanently affected, or whether it remains structurally sound.
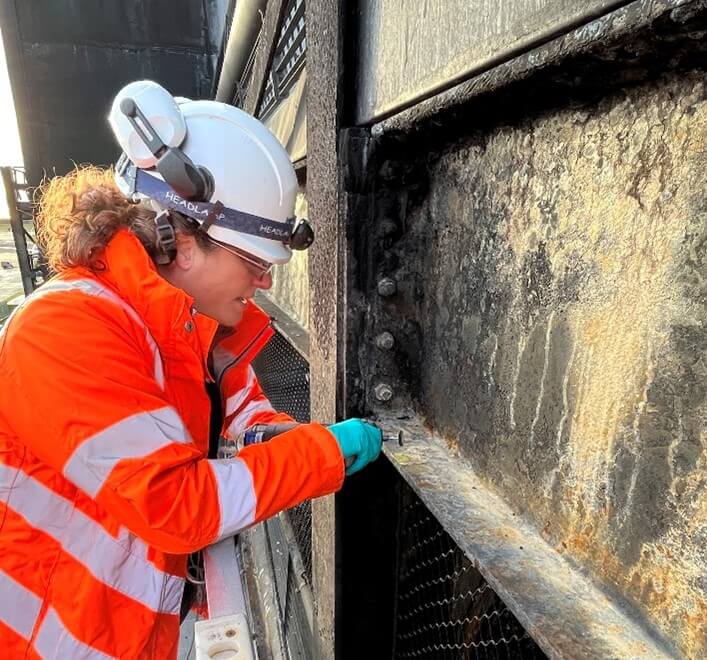
Other Metals and Alloys
In addition to steel, there can be many different metals and alloys present in a fire scene. Understanding of the thermal behaviour of various common metals and alloys, such as those shown in the melting temperature given in Table 1, can help to understand the temperatures that have been reached in a fire. While it may not be immediately obvious what a particular metal is, some techniques can help identify metals in the debris of a fire scene.
A magnet will stick to mild steel, structural steel and cast iron, but not to austenitic stainless steel, aluminium or copper alloys. Looking at the colour of the metal.; dull grey metals could be iron, steel or lead; brighter grey is typical of aluminium or zinc-galvanised steel; the orange colour of copper is characteristic; as is the yellow-golden colour of some brasses.
The acidic constituents of smoke, combined with the water from extinguishing a fire, can cause many metal surfaces to corrode after a fire. The colour of the corrosion products can also help identify a metal. Orange coloured rust is characteristic of iron and steel, while blue/green coloured corrosion occurs with copper. A white oxide could mean lead is present.
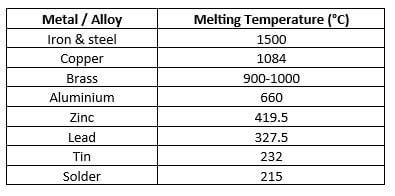
Metal Behaviour in a Fire
Two particular metallurgical features to look out for in fire scenes are arc strikes and contact alloying.
An arc is a single-event electrical discharge across conductors, often copper wires. The localised heat from the arc is enough to melt the copper at the arc contact point. An arc will often leave a notch or groove where molten material is transferred between conductors. Finding evidence of an electrical arc is significant because a spontaneous arc strike from a faulty or damaged electrical item could provide sufficient heat to ignite a fire. However, arcs can occur as both a consequence and the cause of a fire. The heat from an established fire melts or burns the insulation from energised cable or flex, which then allows arc strikes to occur.
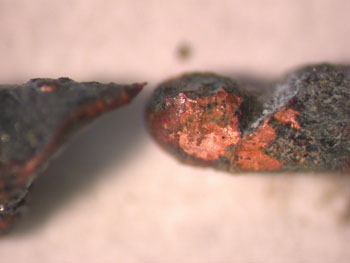
Fire investigators interpret the location and patterns of arc strikes, together with other fire damage or melting around the arc site, as part of the evidence they use to build up their impression of what caused the fire. Identifying arc strikes in wires and conductors can help track fire progression, in a process known as arc mapping. Between two wires, for instance, the furthest arc from the electrical supply must have been the first one to occur. This is because if an arc occurred closer to the electrical power supply first, that would prevent the current from travelling further down the wires. The sequence of various arc strike events can be mapped in this way.
Contact alloying, also known as eutectic melting can occur when molten metal drops onto a solid component of a different metal. Often the initial liquid metal is aluminium, which can be present in sufficient amounts in some fire scenes that when it melts above 600°C it can trickle and drip.
An alloy is a mixture of two (or more) different metallic elements. An effect of this is that the alloy can have different properties to either of the individual constituents; an example is that yellow brasses behave differently to pure copper or pure zinc, its two constituent elements. When liquid aluminium drips onto solid copper, for instance, the interface between them forms a thin layer of aluminium-copper alloy. At certain proportions of aluminium to copper, these alloys can have melting points lower than pure aluminium. At a specific composition, called the eutectic composition, the melting point will be at its lowest. In the aluminium-copper example, the eutectic has 35% copper and 65% aluminium and melts at only 542°C. Therefore, liquid aluminium at 600°C dripping onto solid copper, can form a liquid alloy, with the copper appearing to ‘melt away’; hence the term ‘eutectic melting’. Without understanding how contact alloying can occur, the risk is that the discovery of melted copper at a fire scene might lead to an assumption that temperatures had exceeded 1000°C, or that there was an arc-strike to the copper, potentially misleading the investigator in their interpretation of the fire damage.
When molten liquid metals that have re-solidified in an unusual manner are found in fire debris, they can be identified by further laboratory work, including metallography to identify the microstructures and mixing in the alloy, and chemical analysis to determine the elements present.
Summary
An understanding of the general behaviours of metals, plastics and glass when exposed to fire is a necessary part of a fire investigator’s experience. Consulting with a forensic materials engineer when further analysis is needed can help get to the root cause of the fire, identify if there are prospects for recovery or repudiation and help scope the size of a claim relating to damaged steelwork that might appear smoke-blackened, but is fundamentally undamaged.
About the Author
Materials expert Dr Philippa Moore specialises in materials failures, escape of water and oil, and mechanical and engineering failures. Philippa graduated from the University of Cambridge with MA and MSci degrees in materials science and metallurgy. She then spent 18 years working at TWI Ltd and developed an international reputation in fracture toughness testing, and engineering failure investigations, often of welded steel structures, through her project work and consultancy. Philippa previously led forensic investigations of metallic and/or non-metallic components that had cracked, fractured, or failed, and is an expert on topics related to welding engineering, materials science & metallurgy, failure modes in metals, and structural integrity.
With extensive experience in forensic investigations, Philippa has published over 45 conference and journal papers on her academic research, and on topics supporting her involvement on British and International standards committees for fracture testing.