Modern logistical requirements have driven companies to store as much stock as possible in the minimum amount of space, whilst trying to keep material and operational costs low. Warehouses are now designed with high-rise racking, which is made out of the cheapest material possible and where minimum aisle widths are the norm. Historically, racking structures were over-engineered, but modern warehouse design has led to them being designed specifically for individual requirements and with smaller safety margins.
These changes have resulted in racking structures that are more susceptible to collapse due to their space-optimising design, likely installation deviations and external factors, such as contact by forklift trucks. Modern design has also resulted in larger scale collapses rather than localised damage, due to the proximity of the racks. The key to finding the root cause of a collapse is to identify the origin, which can be a challenge when faced with a large scale collapse.
WHAT CAUSES RACKING TO COLLAPSE?
There are a number of different factors that could result in a racking collapse. The cause might not be a single factor, but can be a number of combined factors which ultimately weaken the structure to a point where it collapses.
The most widely used racking type is adjustable pallet racks (APRs). The main components of this racking system are the racking frame, which usually consist of two uprights and diagonal supports, and the pallet beams, which are supported by the frames.
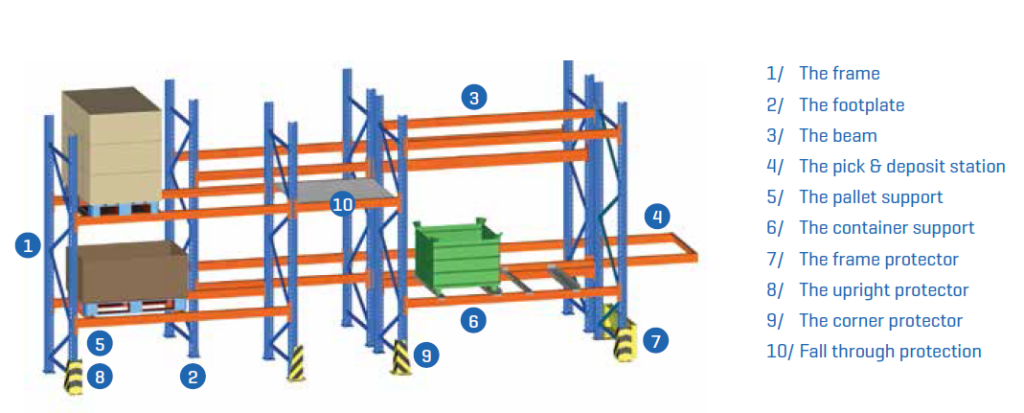
The design of the uprights is such that they are slender members, making them very strong in compression but susceptible to buckling. This type of racking transfers the loads on the pallet beams, caused by the weight of the goods stored on the racking, through the uprights to the floor. If an upright is damaged, installed incorrectly, or moves in such a way that the downwards forces act eccentrically relative to the upright, then it is prone to failure due to buckling.
The main causes of racking collapses are;
- Inadequate design;
- Incorrect installation;
- Overloading at pallet locations;
- Damage
- Mechanical handling equipment (MHE) impacts;
- Supporting floor failure;
- Environmental or chemical deterioration;
- Change of configuration away from that for which the racking was designed;
- Poor weight distribution on pallets, or pallet failure.
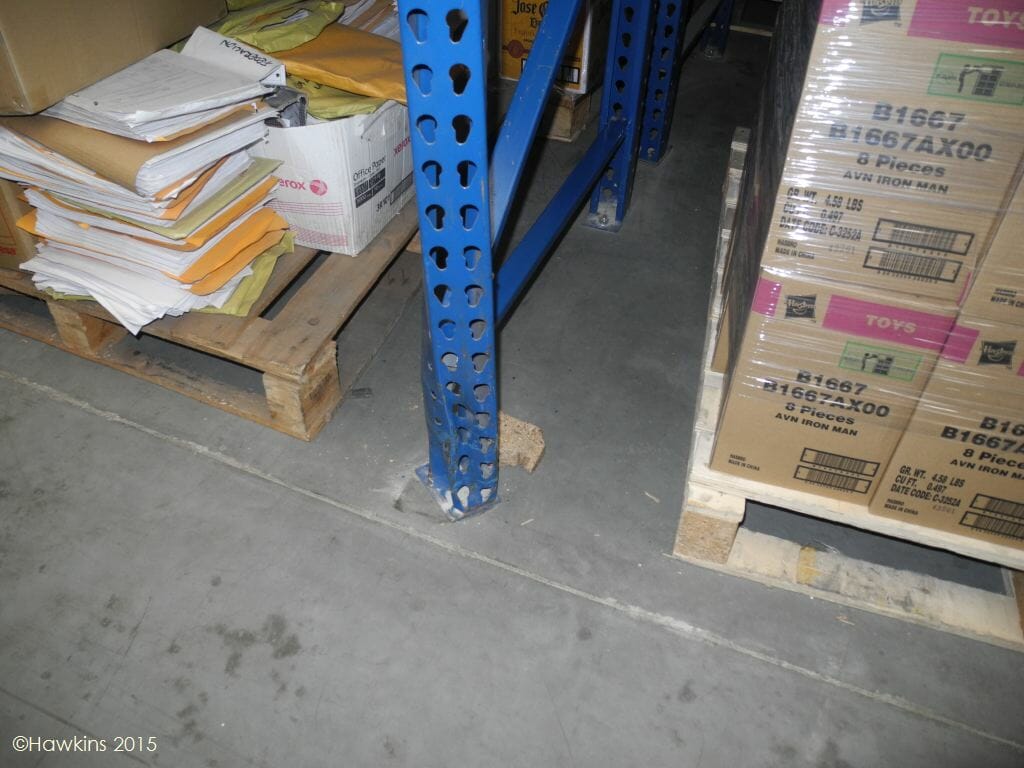
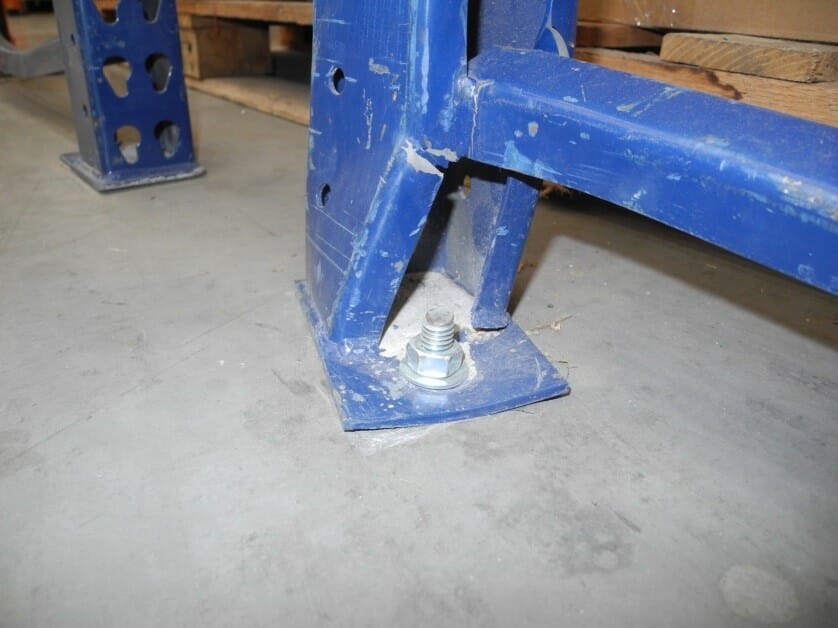
HOW RACKING COLLAPSES ARE INVESTIGATED
The result of a racking collapse is a twisted pile of metal and stock. Therefore, the origin of a collapse is rarely identifiable just by looking at the collapsed state of the racking. In some cases, when a localised collapse occurs, the area of origin is easily identifiable, but these cases tend to be rare. This is because when a rack fails, stock tends to fall away from the rack and the top levels of racking tend to fall laterally, hitting adjacent racks, resulting in a ‘domino’ effect.
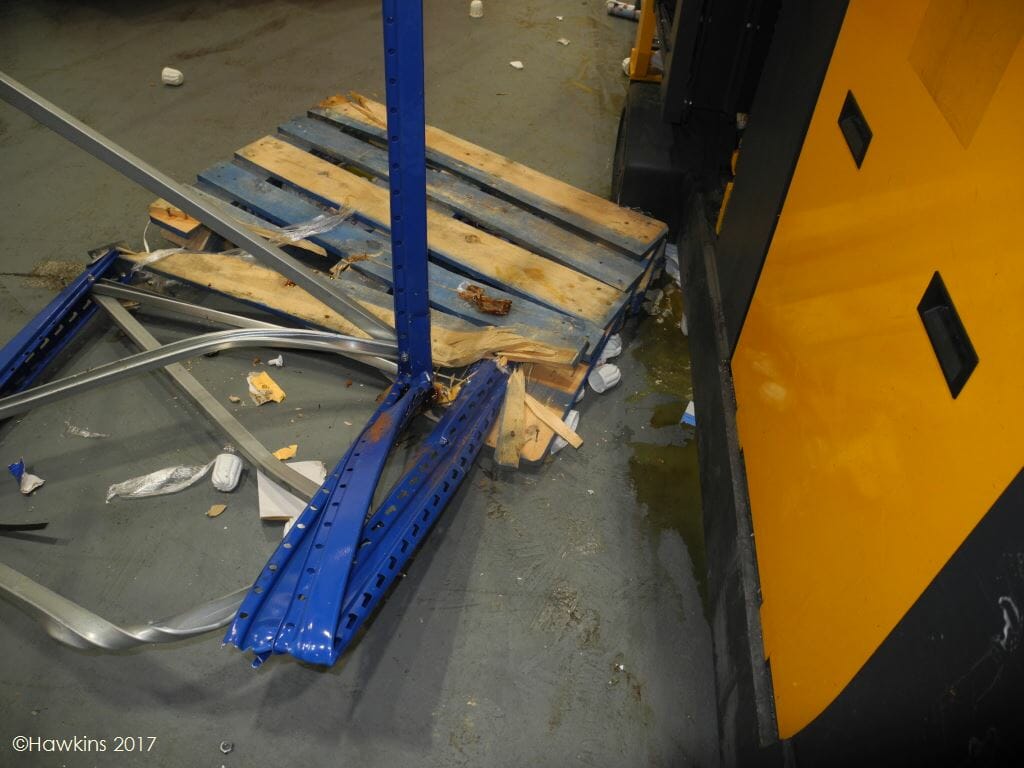
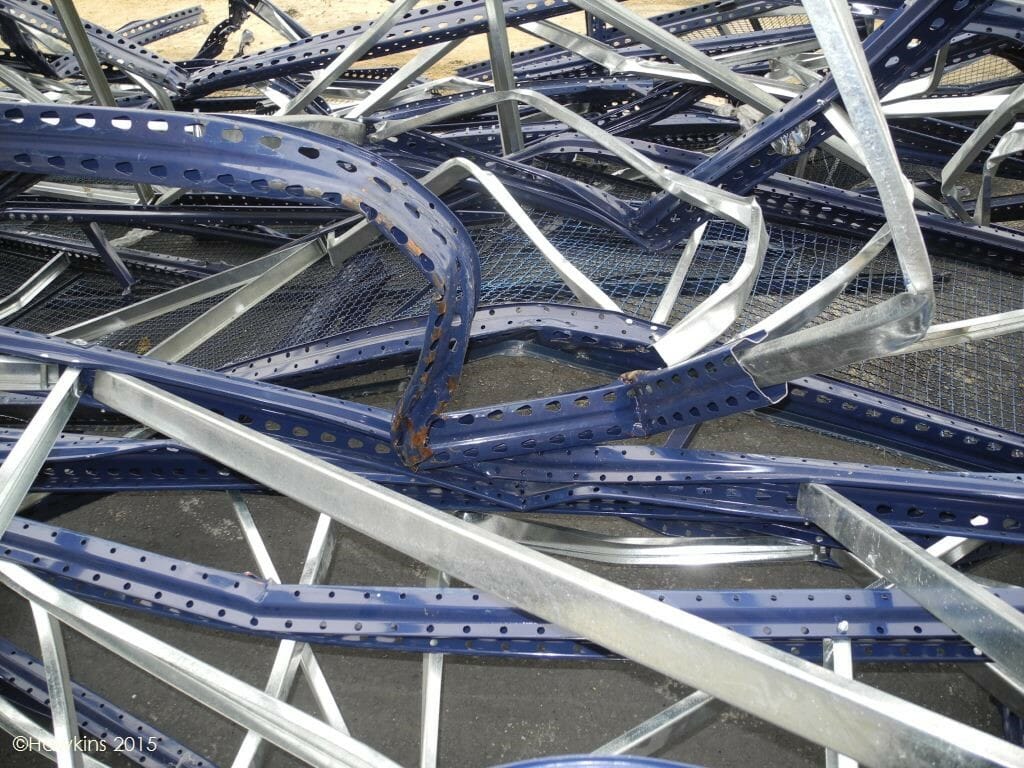
The first steps of an investigation are to obtain witness evidence, any CCTV footage of the incident and to carry out an aerial survey of the collapse. The last areas of racking to fall in a collapse tend to fall radially, away or towards, the area of origin, leaving a radial collapse pattern. Close to the origin, the racks collapse in such a way that at first sight there appears to be no discernible pattern of collapse. At the point of origin, racking first collapses downwards, as uprights buckle at low level, and the tops of these racks then tend to move laterally. The area of origin can sometimes be located by looking for the lowest point of debris. There are exceptions though, because an MHE impact can result in the toppling of a rack resulting in a domino-like pattern and structural components of the building can affect the way a collapse propagates. Therefore, it is essential to ascertain the position of all MHEs within a warehouse at the time of the collapse and the layout of the racking and building structure.
Once areas of interest have been identified, other information, such as MHE movements, pallet bay loading (most logistical organisations now maintain live databases and track movement of pallets through their warehouses), and records of pre-existing damage, should be reviewed, which might provide relevant information as to the cause. Once sufficient clearance of the stock and racking has been carried out and access to the area of interest is available a detailed examination of the remaining racking can be carried out. The positions of adjacent racks, beams and pallets, all of which are usually labelled, can provide information on how the racks collapsed and in what order. This provides an indication of the origin of the collapse.
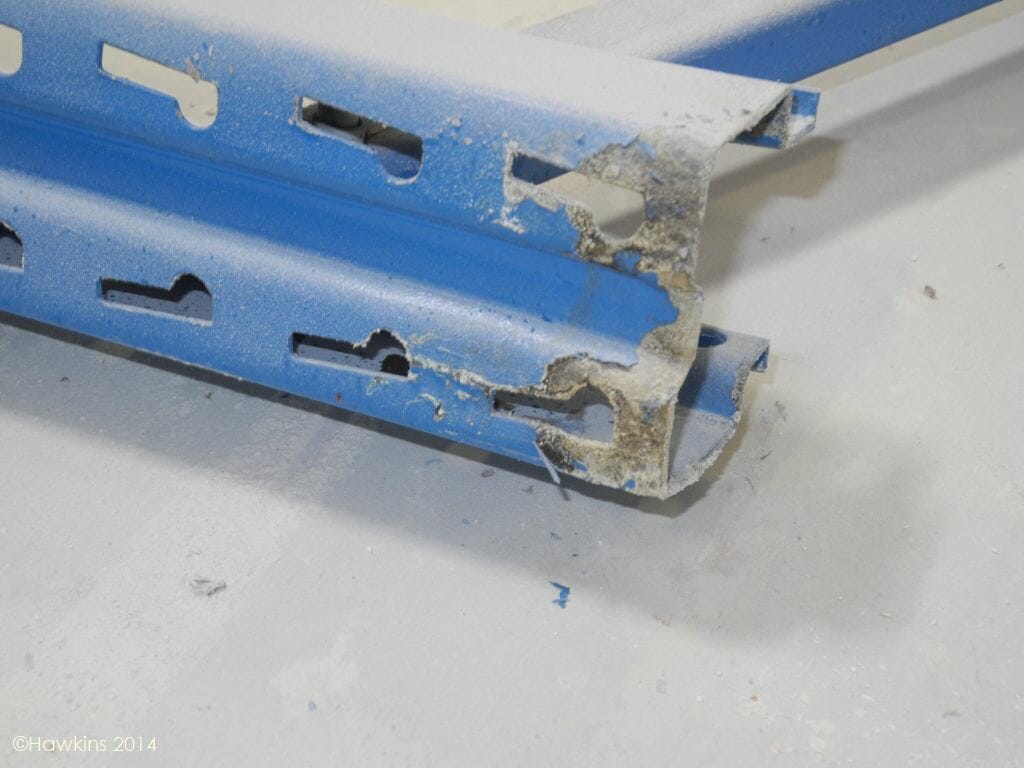
A detailed examination revealed that it was not secured to its foot plate. Uprights should be connected to footplates and footplates in turn anchored to the floor with at least one anchor bolt per upright. Whilst this might not have resulted in the collapse, it is evidence of poor installation which may have contributed to the severity of the collapse. It also makes the upright susceptible to excessive displacement, as a result of external factors (i.e. an MHE impact), which can result in a collapse.
HOW LONG DOES A RACKING COLLAPSE INVESTIGATION TAKE?
Racking collapse investigations can be time consuming. It is normal for the clearance of a warehouse to take months. Investigations can be complicated, especially if the stock in the warehouse poses a health and safety risk. Business interruption can be a significant cost in a racking collapse and therefore, in some instances, insurers might not want the additional delays created by a lengthy investigation.
With this in mind, one option is 3D scanning of the collapse as clearance takes place, which can be carried out using a handheld metrology-grade scanner. 3D scanning will generate a point cloud of the collapse allowing investigators to work remotely to record the position and orientation of racking and stock as the clearance proceeds. A detailed visual inspection of an area of collapse is still essential, but using a remote recording technique, which allows for the initial clearance to commence without delay, reduces the time taken and the business interruption.
Once remotely recorded information is available, the positon and orientation of the racking needs to be interpreted in order to find the origin and hence the cause.
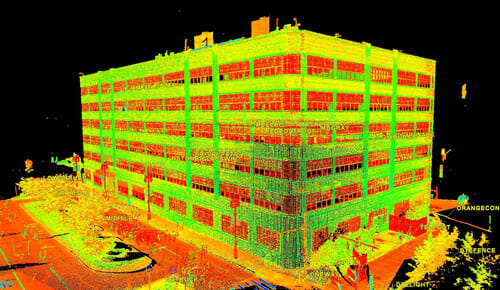
INVESTIGATING WAREHOUSE RACKING COLLAPSES
The interpretation and understanding of racking collapse patterns is essential to finding the origin of a collapse. Much of the evidence required to identify the trigger of a collapse is often altered in the collapse or hard to find due to the size and nature of a collapse. Therefore, careful documentation and consideration of the remaining evidence is necessary to determine the origin and likely cause. When considering this evidence, along with other information, such as witness accounts and CCTV footage, it is usually possible to eliminate a number of potential factors, and in some instances, this is sufficient to determine the most likely cause.
The clearance of a racking collapse can be lengthy. Therefore, techniques which do not hinder clearance activities, but still allow detailed recording of the damage patterns are beneficial, if not essential. Such techniques include aerial drone surveys and 3D scanning from which a computer model of the collapsed state of the racking can be prepared for further assessment. Ultimately, a detailed visual examination of areas of interest needs to be undertaken but this is very much guided by the scanned images. Previous experience of collapse patterns and their interpretation form an important part of the investigation.
ABOUT THE AUTHOR
Mr Gareth Dobinson joined Hawkins in August 2011 after having spent more than 5 years working for Xerox, a role which included assignments to Venray in the Netherlands, Oregon in USA, Senai in Malaysia, and Singapore. During his time at Hawkins, Gareth has investigated over 250 incidents, including fires, mechanical failures and personal injury accidents and has specialised in racking collapse investigations. He is a Chartered Engineer with the IMechE and has undertaken a number of major loss racking collapse investigations, in the UK, Europe and South America.