When you think about painting structures, you might think about the Forth Road Bridge spanning the Firth of Forth, which until recently was famously being repainted from one end to the other, in a continuous loop. The reason for this constant hive of activity was because the paint was constantly flaking off, allowing the underlying steel to become exposed to the rain and sea spray, the perfect environment for corrosion. Recent coating technologies and formulation of an epoxy glass-flake paint (which is much more durable to the environment and the stresses the bridge is under) has meant that this mammoth painting task now only needs to be carried out every 25 years.
Of course, we coat structures, such as steels, in order to protect them from corrosion (with the added benefit of being able to make things look more attractive); you may have read Dr Phillipa Moore’s article titled “Not Just Rust” and have a good appreciation of corrosion and how devastating it can be.
In shipping, corrosion damage can be a significant factor in insurance claims and the prolific use of coatings can help prevent this problem. But coatings can go wrong, and resolving coating failures does not just involve the cost of the paint. Repair of an existing structure can be extremely expensive, perhaps even entailing lost shipping time (for example if a vessel needs to be at a dry dock for many months to accommodate the coating repairs).
There are many different coating types involving different chemical formulations and curing processes. Failure analysis of paints and coatings is all about problem solving, which first involves understanding the basics of coatings and chemistry before considering environmental and usage factors. Personally, I find this the exciting bit; trying to find the ‘what dunnit’ and applying my knowledge to weird and wonderful situations, no matter if they are at sea or on land.
When it comes to coatings, one of the most important questions to answer is what they are going to be used for, as coatings can’t be all things at once. For example, a coating which provides superb corrosion resistance on structural steel, would not be much good as a coating on a wooden structure. Coatings cannot be both hard and soft, or glossy and flat. Most coatings comprise four basic ingredients, pigments, additives, solvents and a binder. Understanding how these elements interact is crucial when understanding how paints and coatings work, and therefore what can go wrong.
Paint Can Blister?
One of the most common types of coating failures that I see, often symptomises as blistering or bubbling of paint. This is not only aesthetically displeasing, but also means that the coating system itself is failing for some reason.
An example of blistering to paint can be seen in Photograph 1. In this case, large steel structures (for use in the transportation industry) were painted and then loaded as cargo onto a vessel. Whilst onboard, the structures were wrapped in a soft fleece, which in turn was wrapped in a plastic mesh and tied down with ropes. When the structures were discharged it was found that the wrappings had become wet, and blistering of the new paintwork was identified. Photographs 2 and 3 show a cross section of one of the blisters which I removed from the side of the structure; a liquid resin had formed within the lower coating layers which had forced the outer paint surface to bulge.
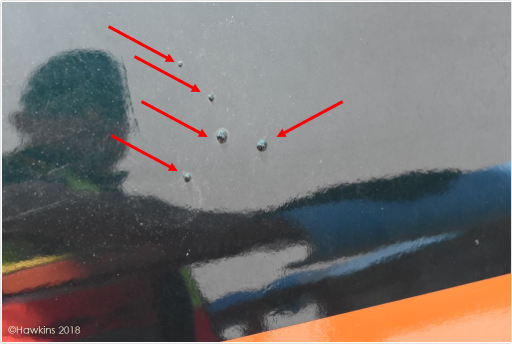
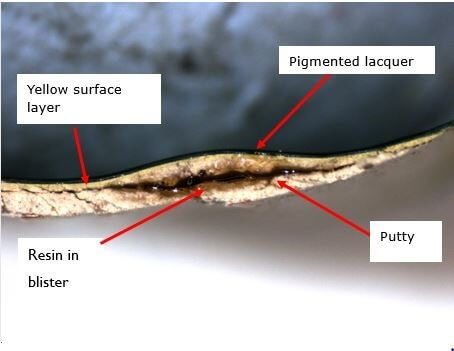
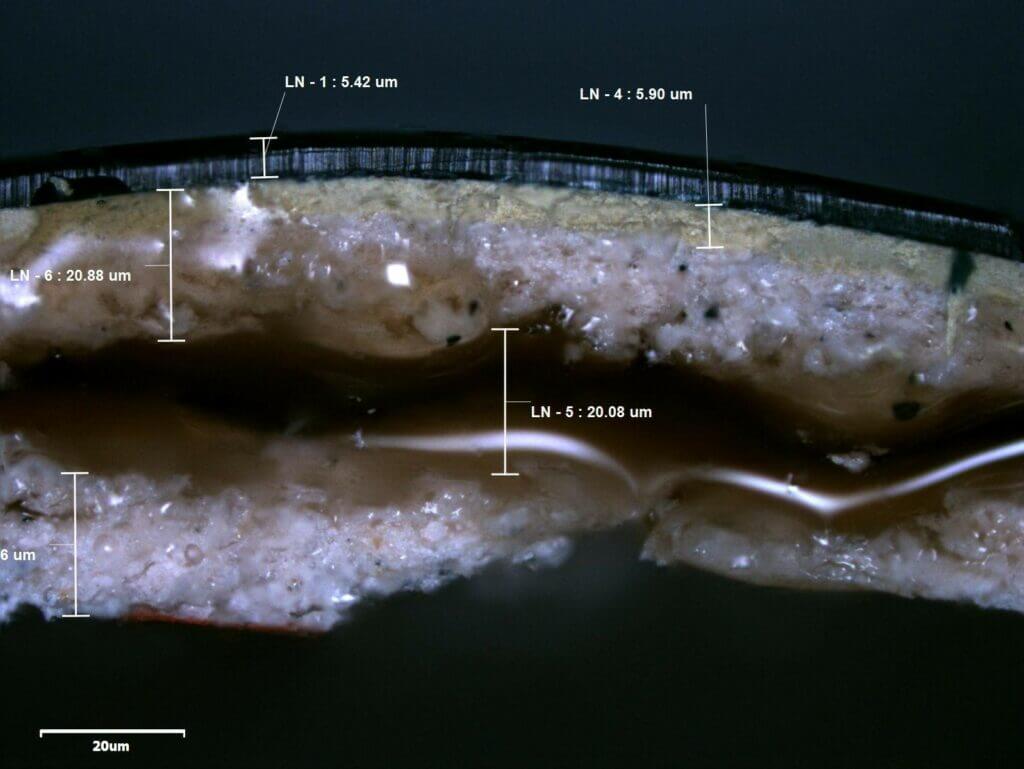
Fourier transform infrared spectroscopy (FTIR), and scanning electron microscopy (SEM) combined with energy dispersive X-ray spectroscopy (EDX) were used to identify the chemical composition of the coating layers, and in particular the composition of the resin found in the blisters. (Image 1 shows the resin under SEM examination).
FTIR analysis of a sample of the resin indicated that it was likely to be algin and was similar to Trilon, a proprietary chelating agent (this is a compound which reacts with metal ions to form stable, water-soluble complexes). The SEM examination of the paint samples confirmed the presence of pores in the surface of the top coat of the paint, through which it would have been possible for water (a relatively small molecule) to permeate. Although water can permeate through most organic based coating systems, this would not necessarily cause premature failure of a coating. However, if there is a water-soluble species behind the coating, or within a lower coat of a multiple layer system, and where water is continuously held against the paint surface, water can permeate the layers and can cause problems.
When a normal amount of water permeates the coating and comes into the water-soluble species below the coating layer(s) it will dissolve it, and if the species is absent in the water on the outside of the coating, an osmotic cell is created.
The osmotic cell comprises a semipermeable membrane (in this case the outer coating layers) that separates a solution of high concentration (i.e. the water-soluble species in the coating layer) from a solution of low concentration (i.e. rain water). This is a non-equilibrium condition and there is a strong driving force to equalise the concentration of these two solutions to make them equal (i.e. to equalise the concentration gradient). Therefore, more water than might otherwise be expected will penetrate the coating layers and will collect behind the coating film. The result of this process is an osmotic blister (i.e. a blister of a water-based solution held behind the layers of paint). The build-up of liquid causes the paint layer to lift from the substrate causing water blisters to form. In dry weather, these blisters can temporarily recede, although the paint layer will have degraded because it is separated from the substrate.
In this case, the liquid or dried resin did not appear below the putty coating layer, i.e. it was not in contact with the underlying metal. However, any degradation in the coating system would lead to a reduction in the life of the bodywork of the painted metal structure.
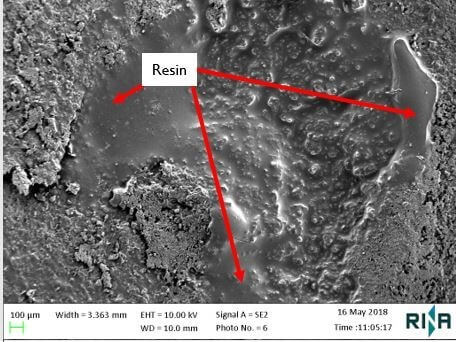
What About Surface Preparation?
Not only can coatings fail when they are kept in unusual environments, they can also fail when the coatings themselves are applied poorly. For example, a colleague of mine examined tanks in a vessel which had been used to store palm oil for about six months. The tanks had been painted, although some of the painted areas appeared to be more recent, as though a paint repair had been made at some stage, see Photograph 4.
Although the palm oil had been in contact with all the painted surfaces of the tanks, for the same length of time, only those areas which had been more recently painted exhibited damage to the paint, such that it had lifted off, see Photograph 5.
The underlying steel structure was corroded and was in a poor state of repair. New and old paint samples were analysed and found to be chemically indistinguishable; i.e. the new paint should have been suitable for use in the holding tanks. The cause of the damage was almost certainly due to poor surface preparation, such that moisture and other contaminants had been trapped beneath the paint, ultimately allowing the steel to corrode and the paint to be forced away from the surface, leaving the steel open to the environment to undergo yet more corrosion.
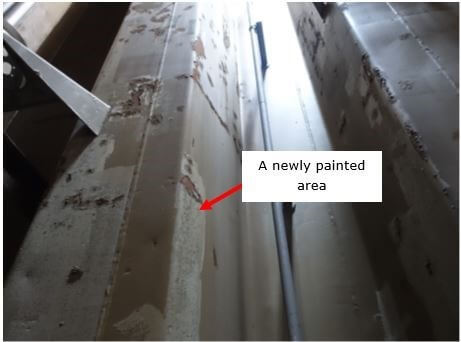
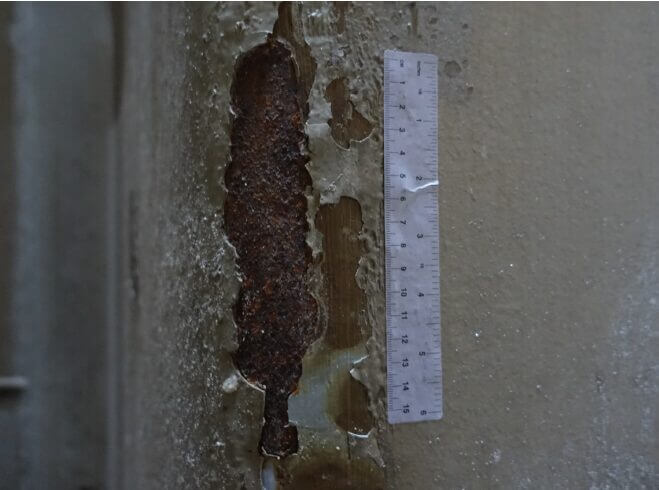
Coating Conclusions
There are of course numerous ways in which coatings can fail, and all of them are likely to be frustrating and possibly expensive to remedy. The most important thing to consider from the outset is whether the coating has been specified correctly, and if it has; is it being used in a suitable environment? If the coating does need to be reapplied or managed in some way (i.e. repair after mechanical damage), are the conditions for reapplication correct or are the seeds of future destruction being sown as the repair is taking place? After all, we all want structures to leave their coats on!
About the Author
Dr Eleanor Jay is a material science and engineering expert with Hawkins & Associates. She specialises in materials failures, escape of water and oil, and mechanical and engineering failures. She has provided expertise on topics related to materials science & metallurgy, failure modes in metals, structural integrity and continuity of fire damaged structures on cases worldwide. She has also published conference and journal papers on her academic research, and on topics supporting her involvement in the energy and nuclear fuel industries.